Инструмент для проверки станков на точность
Инструмент для проверки станков на точность включает проверочную линейку, щупы, уровень, контрольные оправки, индикатор и угольники.
Линейки
Проверочные линейки служат для проверки прямолинейности поверхностей; длинные линейки применяют для проверки прямолинейности направляющих станин.
Рис. 254. Инструменты для проверки станков на точность: а — проверочная линейка, б — щупы, в — уровень, г — контрольная оправка
Проверочные линейки (рис. 254, а) изготовляют из чугуна или из стали; для жесткости и увеличения устойчивости против коробления их снабжают ребрами. Линейки бывают длиной от 500 до 1000 мм и шириной от 30 до 120 мм. С линейками нужно обращаться очень бережно: рабочие поверхности их нужно беречь от ударов и износа, а также смазывать для предохранения от коррозии; когда линейка не в работе, ее рабочая поверхность должна быть покрыта деревянной крышкой.
Щупы
Щупы представляют собой стальные пластины различной толщины от 0,03 до 1 мм. Обычно щупы изготовляют в виде набора (рис. 254, б). Щупы служат для определения зазора между обработанной плоскостью детали и плоскостью положенной на нее линейки или угольника. Щупами промеряют также зазор между поверхностями сопряженных деталей. Обращаться со щупами нужно очень бережно: щуп нельзя вдвигать в зазор с усилием — он может легко согнуться.
Уровнки
Уровень предназначен для проверки горизонтальности направляющих плоскостей станины (рис. 254, в). В металлическом корпусе 1 уровня расположена запаянная с обоих концов стеклянная трубка 2, наполненная жидкостью таким образом, что в трубке остается небольшое количество воздуха, образующего очень подвижный пузырек.
Когда уровень находится в строго горизонтальном положении, пузырек стоит точно посредине трубки между нулевыми штрихами. При наклоне уровня в какую-либо сторону вдоль оси трубки пузырек перемещается в сторону подъема. Если для уровня известна цена деления шкалы, то по перемещению пузырька можно точно определить наклон измеряемой поверхности. Таким образом, установив уровень на проверяемую плоскость (вдоль нее, поперек или по диагонали), можно быстро определить величину и направление ее наклона.
Контрольные оправки
Контрольная оправка 1 (рис. 254, г) представляет точный шлифованный валик диаметром от 25 до 50 мм с точными центровыми отверстиями или с коническим хвостовиком, вставляемым в коническое отверстие шпинделя 2.
Похожие материалы
Точность станка. Испытания металлорежущих станков на точность
Общие замечания
Испытание станков на точность является одним из основных разделов программы испытаний при приемке серийных станков и опытных образцов новых моделей.
Измерения геометрической точности станков относятся к области метрологических работ.
Под геометрической точностью станка, характеризующей качество его изготовления и установки, понимается:
- степень приближения поверхностей, базирующих заготовку и инструмент, к геометрически правильным поверхностям;
- соответствие перемещений в направляющих опорах основных узлов станка, несущих заготовку и инструмент, расчетным геометрическим перемещениям;
- точность расположения базирующих поверхностей относительно друг друга и относительно направляющих опор, определяющих основные перемещения и обусловливающих формообразование обрабатываемых поверхностей;
- точность установки линейных и угловых размеров и точность кинематических цепей передачи.
В процессе обработки изделий возникают усилия, вызывающие деформацию узлов станка, обрабатываемой заготовки и инструмента, а также выделяется тепло, вызывающее тепловые деформации их.
Геометрическая точность станка является важной его характеристикой, но не может в полном объеме характеризовать точность обрабатываемых на станке изделий.
Геометрическая точность станка определяется рядом проверок с помощью измерительных инструментов и приборов. Измерение обработанных на чистовых режимах образцов является косвенной оценкой этой точности и дополняет указанные проверки.
Установка станков перед испытанием на точность
Перед испытанием на точность станок устанавливается на испытательном стенде или на фундаменте на опоры, предусмотренные конструкцией станка. Это должно быть проделано очень тщательно, так как геометрическая точность станка в ряде случаев зависит от точности его установки. Существуют следующие виды установки станков при испытании:
1. Установка станка на три точки опоры обычно применяется для прецизионных станков небольших размеров с жесткой станиной, работающей без дополнительного повышения ее жесткости фундаментом.
Установка станка в горизонтальное положение производится регулировкой опор. Выверка производится уровнями, устанавливаемыми в продольном и поперечном направлениях.
При установке станка все его перемещающиеся части (столы, каретки, суппорты, бабки и др.) должны занимать средние положения.
Следует учитывать возможность изменения положения станка на опорах во время испытания; для исключения ошибок необходимо контролировать положение станины дополнительным уровнем.
2. Установка станка (при эксплуатации) на число опор более трех является наиболее распространенным способом. Станина станка при этом жестко связывается с фундаментом болтами, чем увеличивается ее жесткость.
При установке такого станка для испытания на стенде или фундаменте выверкой с помощью клиньев или башмаков станина станка, не обладающая достаточной жесткостью, деформируется под действием собственного веса и веса смонтированных на ней узлов.
Поэтому установка станка на многих опорах производится с помощью измерения уровнями деформаций станины в отдельных ее частях. Регулировкой опор станина устанавливается в положение, при котором ее деформации будут наименьшими. В процессе испытания станка на точность может иметь место дополнительная регулировка опор в пределах допустимых деформаций станины с проверкой взаимного расположения отдельных частей станка.
При испытании станков, станины которых обладают достаточной жесткостью и работают без закрепления их фундаментными болтами или на виброизолирующих опорах, не допускается в процессе испытания на точность дополнительная регулировка опор.
Установка станка перед испытанием должна быть произведена согласно установочному чертежу, но без затяжки фундаментных болтов.
Точность установки станка перед испытанием указана в каждом разделе приведенных ниже норм точности.
Определение основных отклонений
Основные понятия отклонений формы и расположения линейчатых поверхностей, применяемых в стандартах на нормы точности в соответствии с общими условиями испытания станков на точность по ГОСТ 8-53:
1.
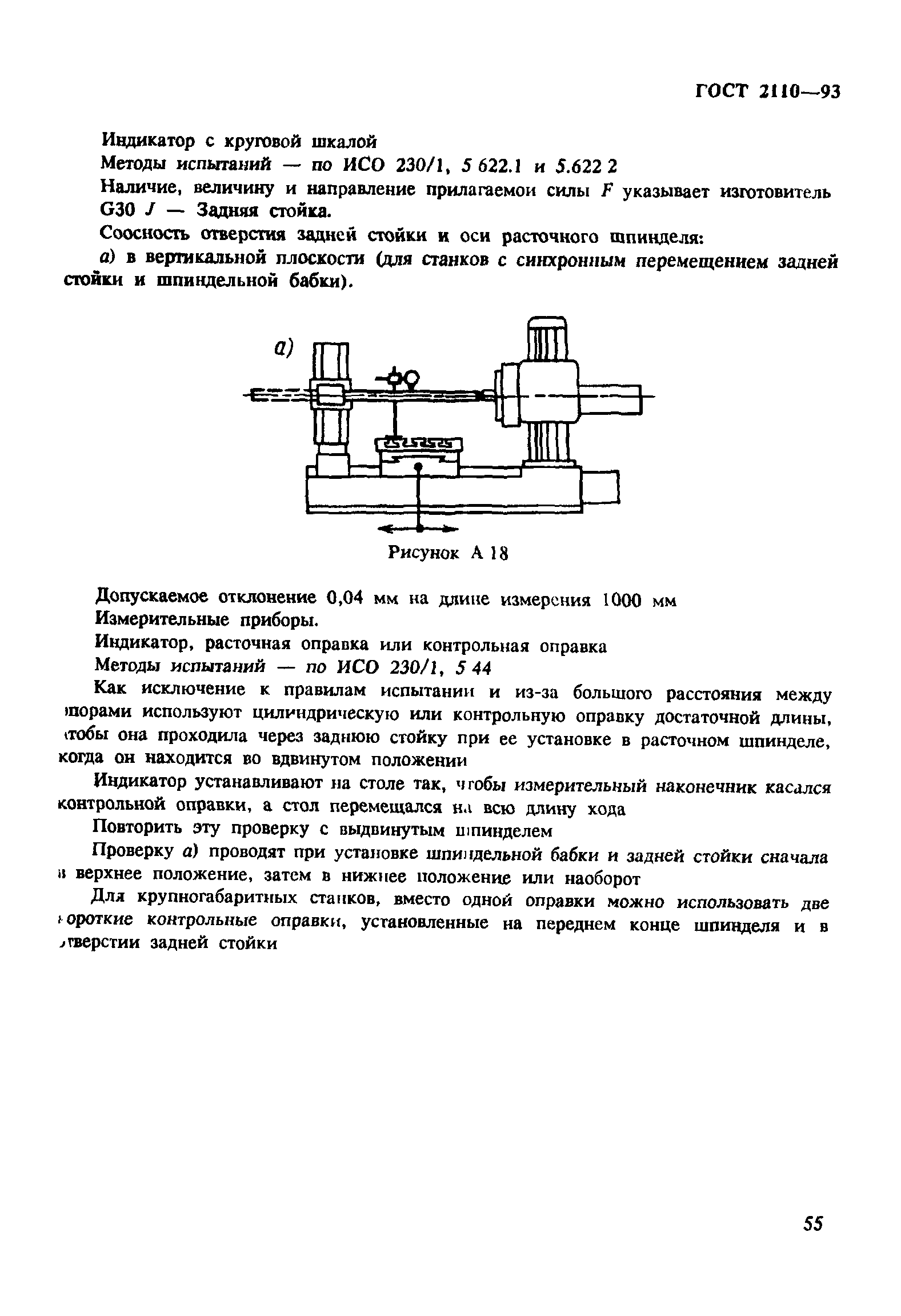
Определение
Наибольшее отклонение от прямой линии (AB) профиля сечения проверяемой поверхности, образованного перпендикулярной к ней плоскостью (I), проведенной в заданном направлении; прямая линия проводится через две выступающие точки (a, b) профиля сечения.
2. Неплоскостность поверхности (рис. 125)
Определение
Наибольшее отклонение проверяемой поверхности от плоскости, проведенной через три выступающие точки поверхности (а, Ь, с).
3. Непараллельность поверхностей (рис. 126)
Определение
Наибольшая разность расстояний между плоскостями, проходящими через три выступающие точки каждой из поверхностей (Н и H1), на заданной длине (L).
4. Неперпендикулярность поверхностей (рис. 127)
Определение
Наибольшее отклонение угла, образованного двумя поверхностями и измеренного в заданной точке линии их пересечения или в двух крайних и средней точке этой линии (углы a, γ. δ), от прямого угла.
5. Овальность (рис. 128)
Определение
Наибольшая разность между наибольшим и наименьшим диаметрами в двух крайних и среднем сечениях или в одном обусловленном сечении (D — d; D
6. Конусность (рис. 129)
Определение
Отношение наибольшей разности диаметров двух поперечных сечений проверяемой поверхности (D — d) к расстоянию между этими сечениями (L).
7. Огранка (рис. 130)
Определение
Наибольшая разность между диаметром окружности, в которую вписан контур сечения проверяемой поверхности, и расстоянием между двумя параллельными плоскостями, касательными к этой поверхности.
8. Непрямолинейность образующей (рис. 131)
Определение
Наибольшее отклонение профиля осевого сечения проверяемой поверхности от прямой линии (АВ; CD), проведенной через две выступающие точки профиля.
9. Радиальное биение (рис. 132)
Определение
Наибольшая разность расстояний (а) от проверяемой поверхности до оси ее вращения.
10. Торцовое биение (рис. 133)
Определение
Наибольшая разность измеренных параллельно оси проверяемой торцовой поверхности расстояний до плоскости, перпендикулярной к оси вращения (l2—l1) на заданном диаметре.
11. Осевое биение (рис. 134)
Определение
Наибольшее перемещение (x) проверяемой детали вдоль оси ее вращения в течение полного ее оборота вокруг этой оси.
12. Несовпадение осей (рис. 135)
Определение
Наибольшее расстояние (с) между центрами поперечных сечений проверяемых поверхностей в пределах заданной длины (l)•
Примечание. В ГОСТ 10356—63 приведены определения отклонений формы и расположения поверхностей, несколько отличающиеся от приведенных выше определений, принятых по действующему ГОСТ 8—53.
Измерение прямолинейности и плоскостности направляющих поверхностей станков
Прямолинейное движение в металлорежущих станках наряду с круговыми представляет главный и наиболее распространенный вид движения и перестановки подвижных частей станка относительно его базовых деталей (станины, стоек, траверс и т д.) и осуществляется с помощью направляющих поверхностей.
Прямолинейность движения определяет точность формы и взаимное расположение обрабатываемых на станке поверхностей, точность координатных и расчетных перемещений, точность установки переставляемых деталей, узлов и механизмов, взаимодействие механизмов, соединяющих подвижные и неподвижные части станка.
В свою очередь, точность прямолинейного движения определяется точностью изготовления и монтажа направляющих поверхностей базовой детали, т. е. степенью приближения их по форме и взаимному расположению к заданным геометрическим формам.
Измерение прямолинейности системы направляющих включает:
- проверку прямолинейности отдельных направляющих поверхностей или следов их пересечения;
- определение взаимного расположения в одной или параллельных плоскостях двух направляющих поверхностей или следа пересечения двух поверхностей и третьей направляющей.
Реальные направляющие поверхности не представляют геометрически правильных плоскостей из-за погрешностей, вносимых в процесс их формообразования совокупностью технологических и других факторов, и только в большей или меньшей степени приближаются по своей форме к плоскостям.
Измерение прямолинейности направляющей поверхности имеет целью установление ее действительной формы с помощью координат, выраженных в линейных величинах и определяющих отклонения направляющей поверхности от исходной геометрической плоскости или следа пересечения поверхностей от геометрической прямой.
Методы и средства измерения прямолинейности основываются на двух видах измерений:
- измерение линейных величин, определяющих координаты элементарных площадок поверхности направляющей относительно исходной прямой линии;
- измерение угловых величин, определяющих углы наклона отдельных участков направляющей, ограниченных элементарными площадками относительно исходной прямой линии
За исходную прямую линию принимаются: линия горизонта, прямолинейный луч света, проекция горизонтально натянутой струны на горизонтальную плоскость, материализованный эталон прямой — линейки и т. д.
Сущность методов измерения линейных величин (оптическим методом визирования, измерением по струне, гидростатическими методами) заключается в том, что координаты элементарных площадок поверхности направляющей определяются непосредственным измерением. Изменение определяет координату элементарной площадки относительно исходной прямой.
Измерение каждой данной площадки не зависит от измерения координат других площадок, за исключением крайних, по которым устанавливаются относительно друг друга измеряемый объект и исходная прямая.
Сущность методов измерения угловых величин (уровнем, коллимационным и автоколлимационным методами) заключается в том, что положение элементарных площадок не измеряется относительно исходной прямой, а определяется взаимное расположение двух соседних площадок последовательно по всей длине направляющей.
Кроме проверки прямолинейности отдельной направляющей, возникает необходимость проверки идентичности формы двух направляющих, которая осуществляется с помощью уровня.
Сущность метода проверки идентичности формы направляющих (извернутости или винтообразности направляющих) заключается в определении посредством уровня углов поворота мостика, установленного в поперечном направлении на две направляющие и перемещаемого вдоль этих направляющих.
Так как допуски на извернутость направляющих назначаются в угловых величинах (часто в делениях шкалы уровня), то результаты измерения непосредственно отражают идентичность формы направляющих. Извернутость определяется наибольшей разностью показаний уровня.
Измерение точности кинематических цепей металлорежущих станков
При проверке точности винторезных цепей токарно-винторезных, резьбофрезерных и резьбошлифовальных станков необходимо измерение точности всей винторезной цепи, включая передаточные зубчатые колеса и механизм ходового винта. Отдельные погрешности, определяющие точность этой цепи: осевое биение шпинделя, прямолинейность направляющих, осевое биение ходового винта и т. д. регламентируются рядом самостоятельных проверок.
Измерение точности винторезной цепи производится с помощью эталонного винта, устанавливаемого в центрах испытываемого станка, и измерительного прибора (отсчетного или самопишущего), устанавливаемого на месте режущего инструмента.
Измерение осуществляется на ходу путем непосредственного контакта измерительного стержня прибора витка эталонного винта при настройке станка на шаг этого винта. Таким образом, проверка производится в условиях аналогичных нарезанию резьбы.
При проверке точности кинематических цепей зуборезных станков применяется теодолит с коллиматором или специализированная аппаратура.
Измерение точности абсолютных перемещений по шкалам производится, главным образом, на прецизионных координатно-расточных станках, координатные системы которых перемещаются на заданные размеры с помощью штриховых мер (шкал и масштабных устройств) или по ходовым винтам, снабженным коррекционными устройствами.
Проверка точности абсолютных перемещений производится по образцовым штриховым мерам с помощью отсчетного микроскопа.
Испытания точности координатно-расточных станков должны производиться высококвалифицированным персоналом в особых температурных условиях по аттестованным образцовым штриховым мерам.
Замеренная точность координатных перемещений будет зависеть от места установки образцовой меры в рабочем пространстве станка. При этом следует выбирать наиболее часто встречающиеся зоны обработки в рабочем пространстве.
Необходимо также учитывать отклонения образцовой штриховой меры по ее аттестату с тем, чтобы определить действительные величины координатных перемещений.
Средства измерения точности металлорежущих станков
Приборы и инструмент общего назначения, применяемые для большинства испытаний точности станков (контрольные линейки и угольники, уровни, щупы, концевые меры, контрольные оправки, индикаторы и микрокаторы и т. д.), достаточно просты и не требуют специальных указаний по их применению.
Все средства измерения, применяемые для проверки точности станков, должны быть соответствующим образом проверены и аттестованы, а их погрешности учтены при проведении измерений.
Необходимо иметь в виду, что в ряде случаев погрешности измерительных приборов и инструмента могут быть автоматически исключены из результатов измерений путем известных в измерительной технике приемов, например: перестановки контрольных оправок с поворотом их на 180°, «раскантовки» уровня при проверке горизонтальности, «раскантовки» угольника при проверке перпендикулярности, измерения прямолинейности двумя гранями проверочной линейки с учетом их непараллельности и др.
Такие приемы измерения обеспечивают высокую точность проверок и должны применяться во всех случаях, где это представляется возможным.
Относительно небольшое количество ответственных проверок, характеризующих точность станка, требует применения специальных измерительных приборов.
Применение этих приборов предполагает наличие квалифицированного персонала, владеющего навыками работы с такими приборами.
К числу специальных измерительных приборов относятся:
- оптические приборы для измерения прямолинейности направляющих — коллимационные и автоколлимационные приборы, визирные трубы, применяемые также для проверки соосности и других целей;
- оптические приборы для измерения углов — теодолиты и коллиматоры, делительные диски с отсчетными микроскопами, применяемые для проверки делительных цепей станков, делительных механизмов и др.
;
- эталонные винты и специальные измерительные и самопишущие приборы для проверки точности винторезных цепей токарно-винторезных, резьбофрезерных и резьбошлифовальных станков;
- прецизионные штриховые меры и отсчетные микроскопы для измерения точности перемещений координатных систем прецизионных координатно-расточных и некоторых других станков;
- приборы для непрерывной проверки делительных цепей зуборезных станков.
При проведении измерений специальными приборами и при обработке результатов измерения необходимо руководствоваться инструкциями и наставлениями к этим приборам.
Методы проверки и средства измерения, указанные в стандартах на нормы точности станков являются обязательными; применение других методов и средств измерения допускается при условии, что они полностью обеспечивают определение требуемой стандартами точности станков. При проверке станков на точность (без резания) движения узлов станка производятся от руки, а при отсутствии ручного привода — механически на наименьшей скорости.
Если конструктивные особенности станка не позволяют произвести измерение на длине, к которой отнесен допуск, последний пересчитывается на наибольшую длину, на которой может быть произведено измерение. Для длин, значительно отличающихся от той длины, для которой указан допуск, правило пропорциональности допусков неприменимо.
Классификация металлорежущих станков по точности
По разработанной в СССР классификации станков по точности они подразделяются на пять классов, приведенных в табл. 171.
Таблица 171
Класс точности станка | Обозначение класса точности | Соотношение основных допусков точности станков |
Нормальной точности станки | Н | 1 |
Повышенной точности станки | П | 0,6 |
Высокой точности станки | В | 0,4 |
Особо высокой точности станки | А | 0,25 |
Сверхточные станки | С | 0,15 |
Как видно из табл. 171 соотношение между величинами допусков при переходе от класса к классу для большинства показателей точности принято равным φ = 1,6.
Это соотношение позволяет согласовать требования к точности станка с требованиями к точности обрабатываемых на нем изделий, так как коэффициент 1,6 учитывается в системах допусков параметров, характеризующих точность поверхностей изделий широкого применения. Станки повышенной точности, как правило, изготавливаются на базе станков нормальной точности, отличаясь от них, в основном, более точным изготовлением и подбором отдельных деталей и повышенным качеством монтажа.
Станки высокой и особо высокой точности отличаются от предыдущих специальными конструктивными особенностями отдельных элементов, высокой точностью их изготовления и специальными условиями эксплуатации.
Сверхточные станки предназначены для обработки деталей наивысшей точности — делительных зубчатых колес и дисков, эталонных зубчатых колес, измерительных винтов и т. п.
При приемке станков более высокого класса точности, чем регламентируется приведенными ниже нормами, можно использовать принятое соотношение основных показателей точности при переходе от более низкого к более высокому классу путем умножения допускаемых отклонений на 0,6.
Сравнение норм точности ГОСТ и иностранных стандартов
Сравнивая стандарты СССР (ГОСТ) на нормы точности металлорежущих станков с аналогичными стандартами других стран, следует отметить:
- По количеству и номенклатуре охваченных стандартами на нормы точности станков (около 65 действующих ГОСТ) СССР занимает ведущее место.
- Объем испытаний станков на точность, регламентированных в ГОСТ, в основном соответствует принятому в большинстве иностранных стандартов.
Различие, главным образом, касается проверок отдельных деталей (станин, ходовых винтов, делительных дисков), которые контролируются при их изготовлении и сборке и в ГОСТ, как правило, не включаются. - Величины допускаемых отклонений параметров, приведенные в ГОСТ на нормы точности, также в, основном, соответствуют принятым в большинстве иностранных стандартов.
Возросшие требования промышленности к качеству выпускаемых станков, в особенности к их точности, надежности и долговечности, а также условия поставки станков на экспорт, ставят перед станкостроительной промышленностью Советского Союза задачу обеспечения достаточной продолжительности работы станков с заданной точностью.
В частности, при изготовлении станков, поставляемых на экспорт, разрешается использовать только часть поля допуска на точность станков. Представляется необходимым в отдельных случаях, там, где это целесообразно, предъявлять более жесткие требования к точности и вводить проверку новых параметров.
В ближайшее время будут выпущены новые и пересмотренные ГОСТ с более высокими требованиями по ряду показателей точности станков и добавлением повышенных классов точности в соответствии с разработанной классификацией. - Следует иметь в виду, что в отдельных случаях допуски, указанные в иностранных стандартах, неоправдано завышены и поэтому, при сравнении их с нормами точности ГОСТ нужно проверять целесообразность этого завышения, а также анализировать влияние пониженных требований к точности отдельных параметров на точность работы станка в соответствии с его назначением.
- В приведенных таблицах сравнения норм точности ГОСТ и иностранных стандартов (табл. 172—192) не всегда даются совершенно идентичные проверки как по методике их проведения и применяемой контрольной аппаратуре, так и по длинам, к которым отнесены допуски на точность.
В таких случаях в таблицах приведены соответствующие оговорки. Допуски пересчитываются в зависимости от длин, к которым они отнесены. Нужно, также, учитывать, что в различных стандартах принята своя собственная система взаимосвязи отдельных проверок, и буквальное сравнение точности их без учета этой взаимосвязи не всегда дает возможность судить о действительной точности работы станков.
В этих случаях требуется более глубокий анализ сравниваемых показателей точности, а также проверка точности работы станков в совершенно одинаковых условиях. - При сравнении допускаемых отклонений по ГОСТ и иностранным стандартам следует учитывать, что при изготовлении станков, поставляемых заводами Советского Союза на экспорт, разрешается использовать только часть поля допуска на точность по ГОСТ:
0,6 — от величины допуска — для станков нормальной и повышенной точности;
0,8 — от величины допуска — для станков высокой и особо высокой точности.
- Полторацкий Н.Г. Приемка металлорежущих станков, ВнешТоргИздат, 1968
- Батов В.П. Токарные станки, 1978
- Схиртладзе А.Г., Новиков В.Ю. Технологическое оборудование машиностроительных производств, 1980
- Тепинкичиев В.К. Металлорежущие станки, 1973
- Чернов Н.Н. Металлорежущие станки, 1988
Список литературы:
Читайте также: Методика проверки токарно-винторезных станков на точность и жесткость
Полезные ссылки по теме
Каталог справочник металлорежущих станков
Паспорта и руководства металлорежущих станков
Проверка токарных станков на точность: ГОСТ, видео
Говоря о точности токарного станка имеется ввиду соответствие данных паспорта оборудования следующим параметрам:
- перемещение тех элементов, на которых располагается заготовка;
- расположение тех поверхностей, с помощью которых базируется инструмент или заготовка;
- форма базовых поверхностей.
После окончательной сборки и проверки на заводе, а также после ремонтов станки получают акт о приемке, и только после этого, вводятся в эксплуатацию.
Требования к точности указываются в паспорте станков.
Выполнение измерения для выявления погрешностей следует производить регулярно в соответствии с нормативами ГОСТ.
Скачать ГОСТ 8-82 «Станки металлорежущие. Общие требования к испытаниям на точность»
Скачать ГОСТ 18097-93 «Станки токарно-винторезные и токарные. Основные размеры. Нормы точности».
В процессе использования токарного оборудования происходит износ его деталей, т.к. при обработке изделий появляются силы, которые производят различные деформации. При работе станок нагревается и под воздействием температуры образуются тепловые деформации. Все эти дефекты оказывают отрицательное влияние на качество обрабатываемых деталей. И для того чтобы восстановить паспортные показатели станка периодически следует ремонтировать изношенные детали.
Качественное испытание токарных станков в соответствии с государственным стандартом во многом зависит от того, насколько правильно он установлен на испытательном стенде. Установка на стенд должна происходить строго, соблюдая установочный чертеж. Самым распространенным методом, является установка на количество опор более 3-х. Отметим, что все двигающиеся части проверяемого станка должны находится в средних положениях.
Геометрическая точность токарного станка характеризует качество изготовления деталей, поэтому установка заготовки должна осуществляться на геометрическую правильную поверхность.
Для определения степени износа нужно установить линейку поочередно на каждую из направляющих станины. После этого, щупом определяется расстояние между направляющими и контрольной линейкой. Допустимое значение такого износа согласно государственного стандарта не должно превышать 0,02 мм.
Не мало важным фактором является соответствие горизонтальности направляющих станины. Определить ее можно с помощью перемещения специального уровня вдоль поверхности направляющих, который покажет значение имеющегося отклонения. Предельно допустимое отклонение по ГОСТ не может превышать значение 0,05 мм. А параллельность между направляющими станины для упорной (задней бабки) и каретки можно проверить с помощью специального измерительного индикатора. Его необходимо закрепить на каретке с суппортом и с помощью перемещения каретки выявить величину отклонения.
- Проверка параллельности направляющих
- Проверка горизонтальности направляющих станины
Также точность токарного станка поможет определить биение вращающегося шпинделя, в который крепится заготовка. Обязательно при этом соблюдать параллельность между осью шпинделя и направляющими станины. Во время проверки в отверстие вала устанавливают специальную контрольную оправку и на протяжении всей ее длины проверяют ее на биение.
Осуществляя технологическую проверку на точность стоит обратить внимание также и на вращение шеек вращающегося вала. Биение при их вращении — не допустимо. В резцовой головке необходимо закрепить индикатор, затем уперев его штифт в шейке шпинделя произвести измерения. По ГОСТ значение не должно превышать 0,01 мм. Не допустимым будет при вращении шпинделя, чтобы он отклонялся от оси.
Проверка биения шпинделя: а — проверка биения шейки шпинделя; б — проверка осевого перемещения шпинделя; в — проверка биения переднего центра
Также одним из важных измерений при проверке токарного станка на точность является определение точности шага ходового винта. Величина отклонения в соответствии с ГОСТ определяется с помощью следующей методики:
- в центры передней и задней бабки устанавливают резьбовую оправку;
- на эту оправку накручивают гайку в форме цилиндра и имеющую паз;
- в паз этой цилиндрической гайки устанавливается шарик державки;
- индикатор, закрепленный в державке, упирается в торцевую часть цилиндрической гайки;
- токарный станок настраивается на шаг резьбы;
- индикатор определяет отклонения.
Проверка точности шага ходового винта
Основные погрешности формы обрабатываемых заготовок:
- непрямолинейность;
- конуснообразность;
- отсутствие параллельности;
- некруглость;
- неконцентричность.
Инструмент, применяемые при испытаниях:
- контрольная линейка;
- уровень;
- щуп;
- угольник;
- измерительный индикатор;
- резьбовая оправка;
- контрольная оправка;
- цилиндрическая гайка;
- державка.
При выполнении измерений следует использовать только те инструменты, которые прошли метрологическую поверку с учтенной погрешностью.
Оборудование, применяемое при работе | СервисТЕХ
Беспроводная система Renishaw QC20-W Ballbar System
Беспроводная система QC20-W с использованием датчиков ballbar применяется для проверки точностных параметров станков. Эта система дает реальные преимущества для пользователей с точки зрения производительности и удобства в работе.
Использование беспроводной технологии Bluetooth позволяет устранить все проблемы, связанные с наличием проводов, а также обеспечивает работу при «закрытых дверях» и снижает вероятность повреждения системы.
Стандартный комплект QC20-W ballbar входит датчик в сборе длиной 100 мм и удлинители длиной 50, 150 и 300 мм. Используя различные комбинации удлинителей, можно выполнять тесты с радиусом 100, 150, 250, 300, 400, 450, 550 или 600 мм.
Держатели шариков измененной конструкции (новый центральный держатель и удлинитель магнитной опоры, имеющей углубление) позволяют, пользуясь системой QC20-W, выполнять дополнительные тесты по «неполной» дуге 220° в плоскостях, проходящих через ось центрального держателя. Это означает, что теперь можно выполнять ballbar-тесты в трех взаимно перпендикулярных плоскостях, не меняя положения центрального держателя, что ускоряет проведение проверки (для выполнения проверки по «неполной» дуге с радиусом больше 150 мм необходимо предусмотреть дополнительные крепежные приспособления).
Функциональные возможности системы QC20-W ballbar могут быть расширены за счет использования различных принадлежностей:
- Пользуясь дополнительными удлинителями, можно выполнять тесты по окружностям с радиусом вплоть до 1350 мм;
- Комплект принадлежностей для диагностики по окружности малого радиуса позволяет выполнять тесты по окружности радиусом 50 мм;
- На двухкоординатных станках тестирование может выполняться с использованием VTL-адаптера, а на многих токарных станках — с использованием соответствующего комплекта принадлежностей для токарных станков.
Все эти дополнительные средства, а также возможность использования различных скоростей подачи делают систему QC20-W исключительно универсальным средством тестирования станков.
Содержимое комплекта системы
Стандартный комплект системы QC20-W поставляется в прочном чемодане; в состав комплекта входят следующие компоненты: беспроводная система QC20-W ballbar, батарея, шпиндель и держатели для монтажа на столе (поворотные), удлинители для системы длиной 50, 150 и 300 мм (для выполнения тестов при различных диаметрах) и соответствующий инструмент. Программное обеспечение Ballbar 20 и руководство к нему поставляются вместе на одном компакт-диске (CD), а видеоруководство по началу работы дается на отдельном компакт-диске (DVD).
Комплект также включает калибратор, который обеспечивает дополнительные возможности для анализа результатов. (этот калибратор позволяет получать абсолютные значения ошибок шкалы, а также является удобным средством проверки правильности работы датчика ballbar).
Кроме того, к комплекту прилагаются сертификаты калибровки для датчика ballbar и калибратора с полными данными о метрологической прослеживаемости измерений, а также этикетки для регистрации времени проведения теста на станке.
Является мерительным средством сертифицированным Государственным реестром средств измерений (Росреестр)
Контрольно-измерительные оправки EWS (WSW) — Osnastka.pro
Контрольные оправки EWS (WSW) с хвостовиком SK по DIN 69871
|
Контрольные оправки EWS (WSW) с хвостовиком SK. |
|
||||||||
Контрольные оправки EWS (WSW) с хвостовиком BT по JIS B 6339 (MAS 403 BT) |
||||||||||
Контрольные оправки EWS (WSW) с хвостовиком BT. Для диагностики станков по рекомендациям ISO-R230 или для наладки шпинделя. |
|
Контрольные оправки EWS (WSW) по DIN 2080 |
||||||||
Контрольные оправки EWS (WSW) с хвостовиком SK. Для диагностики станков по рекомендациям ISO-R230 или для наладки шпинделя. Поставляется с протоколом испытаний. |
|
Контрольные оправки EWS (WSW) с хвостовиком HSK-A по DIN 69893 / ISO 12164-1 |
||||||||
Контрольные оправки EWS (WSW) с хвостовиком HSK-A. Для диагностики станков по рекомендациям ISO-R230 или для наладки шпинделя. Поставляется с протоколом испытаний. |
|
Контрольные оправки EWS (WSW) с хвостовиком CAPTO по ISO 26623-1 |
||||||||||||||||||||||||||||||||
Контрольные оправки EWS (WSW) для диагностики станков по рекомендациям ISO-R230 или для наладки шпинделя.![]() |
|
|||||||||||||||||||||||||||||||
Контрольные оправки EWS с хвостовиком VDI по DIN 69880 |
||||||||||||||||||||||||||||||||
Контрольные оправки EWS с хвостовиком VDI по DIN 69880 |
|
|||||||||||||||||||||||||||||||
Регулировочный держатель инструмента EWS с хвостовиком VDI по DIN 69880 |
|
|||||||||||||||||||||||||||||||
Футляр для оправок EWS c с хвостовиком VDI по DIN 69880 |
|
|||||||||||||||||||||||||||||||
Печать
Проверка токарного станка на точность
04.05.2018
Когда речь идет о геометрической и технологической точности токарного станка проверяются следующие параметры оборудования:
-
точность перемещения частей, на которых располагается деталь;
-
расположение поверхностей, на которых должен находиться инструмент или материал;
-
форма базовых поверхностей.
Оборудование должно начать эксплуатироваться только после проверки точности и получения акта о приемке. При этом такой акт составляется не только после сборки на заводе-изготовителе, но и после проведения ремонтных работ.
Параметры точности агрегата должны быть указаны в его паспорте. Измерять точность и выявлять погрешности нужно регулярно. Частота проверок оборудования регламентируется соответствующим ГОСТом.
Во время эксплуатации токарного станка его элементы постоянно изнашиваются. Во время работы агрегат неизбежно нагревается, соответственно, происходит тепловая деформация. Кроме этого, на рабочие части и механизмы постоянно воздействуют различные силы, приводящие к изменению их формы и снижению четкости оборудования. В конечном итоге износ и деформации негативно сказываются на качестве изготавливаемой продукции. Чтобы восстановить правильность работы агрегата, следует постоянно проверять его на степень износа и своевременно производить замену деталей и узлов.
Как правильно проверять токарный станок
Качество проверки во многом зависит от того, насколько правильно оборудование установлено на испытательном стенде. Устанавливать станок необходимо строго следуя чертежу. Наиболее популярным и надежным способом является установка агрегата на несколько опор (более трех). Все подвижные узлы и элементы должны быть установлены в среднее положение.
Качество изготавливаемых изделий зависит от геометрической точности оборудования. Поэтому устанавливать заготовку нужно на геометрически правильную поверхность.
Чтобы определить степень износа линейка устанавливается по очереди на каждую направляющую станка. После чего при помощи щупа нужно измерить зазор между линейкой и направляющей. ГОСТ определяет максимально допустимое значение этого зазора – не более 0,02 мм. При большем отклонении обрабатываемые детали могут иметь недопустимую погрешность на выходе.
Точность во многом зависит и от горизонтальности направляющих станка. Этот показатель измеряется при помощи специального уровня. Предельное отклонение должно быть не более 0,05 мм.
При проверке оборудования на исправность обращайте внимание на все вращающиеся детали. Их движение должно осуществляться строго по оси, биение во время вращения недопустимо. Если любой элемент отклоняется от оси вращения, это не только сказывается на качестве изготавливаемых изделий, но и угрожает безопасности оператора. При «биении» заготовки в станке есть риск получения травмы из-за вылетевшей из держателей детали или сломавшегося инструмента.
Во время проверки оборудования важно определить также точность шага винта. Для определения погрешности и отклонения имеется специальная методика:
-
в бабки станка устанавливается оправка;
-
на нее фиксируется цилиндрическая гайка с пазом;
-
в паз гайки фиксируется державка с индикатором, который должен упереться в торец гайки;
-
аппарат нужно настроить на резьбовой шаг;
-
в процессе работы индикатор фиксирует погрешность.
Основные геометрические дефекты, вызванные низкой точностью станка:
-
изделие получается не прямолинейным;
-
цилиндрическое изделие может получиться конусообразным;
-
основные линии заготовки не параллельны друг другу;
-
в сечении изделие не круглое, а овальное или иной формы;
-
места разного сечения не концентричны.
-
контрольная линейка;
-
специальный уровень;
-
измерительный щуп;
-
угольник;
-
оправка, державка с индикатором;
-
пазовая гайка.
Во время проведения испытаний оборудования на четкость используйте только те приспособления и инструменты, которые прошли метрологическую проверку. Испытания непроверенными измерительными инструментами могут дать неправильный результат, который непременно скажется на качестве работы оборудования.
коленчатая оправка — это… Что такое коленчатая оправка?
- коленчатая оправка
Automation: support arm , supporting arm
Универсальный русско-английский словарь. Академик.ру. 2011.
- коленчатая камера сгорания
- коленчатая ось
Полезное
Смотреть что такое «коленчатая оправка» в других словарях:
ГОСТ 22267-76: Станки металлорежущие.
Схемы и способы измерений геометрических параметров — Терминология ГОСТ 22267 76: Станки металлорежущие. Схемы и способы измерений геометрических параметров оригинал документа: 25.1. Ме тоды измерения Метод 1 при помощи прибора для измерения длин при прямолинейном движении рабочего органа. Метод 2… … Словарь-справочник терминов нормативно-технической документации
Описание — 3.2. Описание СИЗОД фильтрующие с принудительной подачей воздуха, используемые с масками, полумасками и четвертьмасками обычно состоят из следующих элементов: а) одного или нескольких фильтров, через который (которые) проходит весь воздух,… … Словарь-справочник терминов нормативно-технической документации
Описание ме тодов измерения — 14.2. Описание ме тодов измерения 14.2.1. Метод 1 Средства измерения: коленчатая оправка с прибором для измерения длин, контрольная оправка. При измерении на станках классов точности А и С применяют коленчатую оправку, несущую два одинаковых… … Словарь-справочник терминов нормативно-технической документации
Описание метода измерения — 12.
2. Описание метода измерения 12.2.1. Метод 1 Средства измерения: коленчатая оправка, прибор для измерения длин, контрольная оправка. Схема измерения указана на черт. 42. Черт. 42 Проведение измерения Коленчатую оправку 1 устанавливают на… … Словарь-справочник терминов нормативно-технической документации
Описани е методов измерения — 9.2. Описани е методов измерения 9.2.1. Методы 1а и 1б Средства измерения: поверочный угольник с углом 90° и прибор для измерения длин. Схема измерения указана на черт. 34. Черт. 34 Проведение измерения Поверочный угольник 2 опорной поверхностью… … Словарь-справочник терминов нормативно-технической документации
Узнайте больше о том, что такое расширительные оправки на токарном станке
Существует множество устройств, таких как патроны, цанги, планшайбы, приводные пластины, оправки и токарные центры, которые используются для удержания и привода заготовки во время ее обработки на ручном токарном станке.
имеют коническую ось, которая вдавливается в отверстие в заготовке, чтобы поддерживать ее между центрами. Вы бы использовали оправку на токарном станке, когда заготовку невозможно захватить для точной обработки. Затем оператор устанавливал заготовку на оправку и вращал ее между центрами на токарном станке, как в моделях RKL, продаваемых LeBlond.
Раздвижные оправки на токарном станке — это тип оправки, которая зажимает внутренний диаметр или внутренний диаметр заготовки.
На разжимной оправке вал и втулка имеют соответствующие конусы и изготовлены из закаленной стали. Втулка имеет прорези и расширяется при вдавливании в конический вал.
Оправки расширительные на токарном станке:
- используется для деталей с большим диапазоном размеров
- работает как патрон в том смысле, что захваты могут быть выдвинуты наружу к внутреннему отверстию в заготовке
- используются для обработки внешнего диаметра (OD) заготовки с отверстием, которое ранее было рассверлено или просверлено.
- в основном предназначены для шлифовальных работ и контроля, но могут использоваться для токарного станка двигателя, когда вы хотите, чтобы заготовка работала соосно ID .
- Используются для поддержки узких заготовок, таких как фрезы и шкивы с клиновым ремнем.
- Используются на других станках, которые могут поддерживать работу между центрами, например, цилиндрический шлифовальный станок и инструментальный шлифовальный станок
Раздвижные оправки устанавливаются на токарном станке между центрами и приводятся в движение с помощью держателя токарного станка или «собачки токарного станка».”
Собака токарного станка:
- — это устройство из литого металла, используемое для создания прочного соединения между шпинделем передней бабки и заготовкой, установленной между центрами
- позволяет вращать заготовку с той же скоростью, что и шпиндель, пока оператор режет.
- имеет выступ в виде пальца, который либо прямой («прямой хвост»), либо изогнут под углом 90 градусов («загнутый хвостовик на токарном станке»).
Палец или «загнутый хвост» собачки токарного станка входит в паз в приводной пластине, установленной на передней части шпинделя ручного токарного станка.«Прямой хвост» приводится в движение специальным штифтом, который ввинчивается в лицевую часть приводной пластины.
При установке заготовки на К.О. Ли расширяющую оправку, проверьте на наличие заусенцев и очистите. Смажьте его легким маслом, чтобы заготовка не «замерзла» при повороте. Когда оператор поворачивает заготовку на токарном станке, он должен подавать ее к большему концу оправки, который должен быть ближе всего к передней бабке.
При расширении и сжатии К.О. Ли расширяет оправки на токарном станке, используйте молоток весом 8 унций, чтобы слегка постучать по оправке, чтобы она встала на место.Или вы можете использовать оправочный пресс, чтобы их затянуть.
Раздвижные оправки на токарном станке — это, в основном, специальный инструмент для закрепления заготовок, и обязательно следуйте этим рекомендациям при использовании их на токарном станке по металлу LeBlond RKL или Regal.
ЗАИНТЕРЕСОВАННЫХ:
LeBlond или K.O. Lee, щелкните этот запрос предложений…
OEM детали для LeBlond, K.O. Ли, Standard Modern, Johnson Press, Deka Drill или W.F. & Джон Барнс, щелкните эту форму…
ИЛИ позвоните нам по телефону +1 (888) 532-5663.
Новости | Прецизионный шпиндель и аксессуары
E-B Manufacturing представляет Flex-Ring, расширяющуюся оправку или разрушающийся на 360 градусов патрон
15 мая 2010 г.
Flex-Ring — это диск со скошенной кромкой, который при нажатии до более плоского состояния расширяется в отверстие заготовки или сжимается по внешнему диаметру заготовки. Это движение центрирует заготовку, захватывает ее и тянет назад, обеспечивая высокое зажимное усилие, способное передавать высокий крутящий момент с положительным откатом к рабочему упору и точностью 0.0001 ″ повторяемость
Несколько гибких колец можно уложить друг на друга, чтобы обеспечить необходимую длину зацепления с отверстием или внешним диаметром детали.
Flex-Ring может приводиться в действие двухтактным приводом зажимного патрона токарного центра, любым гидравлическим или пневматическим цилиндром для фрезерования или, в качестве альтернативы, автономным гидравлическим или пневматическим приводом типа «блинчик».
Flex-Ring может зажимать короткие диаметры, как внутреннего, так и внешнего диаметра, которые невозможно зажать цангами.
В любом применении для круглых заготовок, где Flex-Ring подходит и зажимает, вообще говоря, оно обеспечивает почти вдвое большую способность передачи крутящего момента по сравнению с цанговым зажимом.
Flex-Ring может изготавливаться для любого диаметра, для развальцовки оправок на внутренний диаметр 20 мм и более, для свертывания патронов на внешний диаметр 10 мм и более.
Разжимные оправки или зажимные патроны Flex-Ring могут быть изготовлены для зажима дифференциальных диаметров. Гибкое кольцо может быть встроено в промежуточные оправки или между центральными оправками, а также в контрольные оправки или контрольные оправки.
Spindel Corporation из Гранд-Рапидс, штат Мичиган, ремонтирует, заменяет высокочастотные приводы шпинделя и инверторы
23 апреля 2010 г.
Spindel Corporation ремонтирует и заменяет высокочастотные приводы шпинделя и инверторы
Типичные области применения: внутреннее шлифование, универсальное внутреннее / внешнее шлифование, профильное шлифование, шлифование отверстий, конусное шлифование, резьбошлифование, кондукторное шлифование, высокоскоростная обработка и фрезерование.
Инверторывключают следующие марки: SpindelMaster, Volkmann / Graseby / TB Woods, Acomel / Warner Electric / Danaher Motion, REFU / Rexroth / Indramat / Bosch, Sieb & Meyer, KaVo, Gamfior, PTI, Hitachi.
Мы также заменяем высокочастотные мотор-генераторы на высокочастотные приводы и инверторы.
Мы также производим шкафы привода шпинделя на заказ для новых и существующих станков. Некоторые особенности включают: заглушки для нескольких шпинделей, функцию устранения зазоров, интерфейс управления для конкретного станка, контакторы двигателя шпинделя, реле управления, источники питания, предохранители и предохранители для насосов охлаждающей жидкости, смазочное оборудование, корпуса Nema 12, предохранительные выключатели, ролики, индивидуальные краска
SKF MACHINE TOOL SERVICE, ранее находившийся в городе Дулут, штат Джорджия, в настоящее время переведен на предприятие по ремонту шпинделей в Техасе.
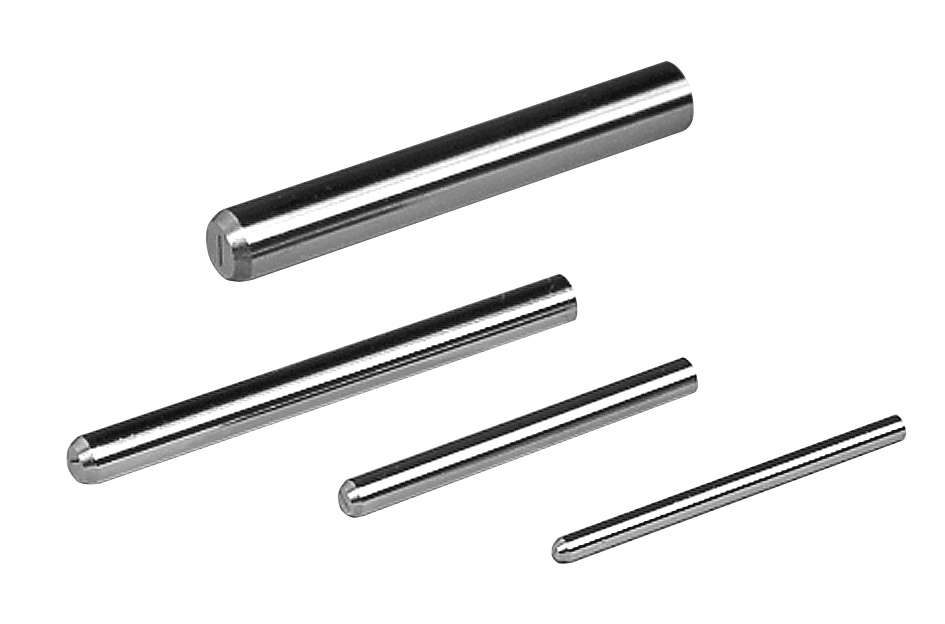
1 апреля 2010 г.
Наше предприятие по ремонту шпинделей SKF Machine Tool Service переехало в современное предприятие в Техасе.Завод в Дулуте, недалеко от Атланты, штат Джорджия, ранее назывался American Precision Spindles, 770-814-7540 и сейчас закрыт. Новый техасский ремонтно-сервисный центр работает.
Свяжитесь с нами для получения подробной информации.
Факты о гибке труб из нержавеющей стали на оправке
Что такое изгиб на оправке?
Гибка на оправке — это метод гибки с вращательной вытяжкой, при котором оправка, цельный вал оправки, имеющий до пяти сегментированных, кольцевидных шариков, которые лишь немного меньше внутреннего диаметра трубы / трубы, которую изгибают, — это вставляется в трубу / трубу для обеспечения внутренней поддержки во время изгиба.Установка оправки внутри трубы предотвращает такие повреждения, как деформация, сжатие, волнистость и сплющивание, и дает техническому специалисту больший контроль над овальностью или округлостью трубы / трубы.
Этот вариант изгиба трубы полезен для сложных работ, требующих изгибов с большим радиусом и большим радиусом, нескольких радиусов, высокой точности и повторяемости с минимальной деформацией. Помимо повышения качества проекта, гибка оправки может сэкономить более 50% затрат по сравнению с резкой и сваркой, поскольку сокращает время изготовления, материалы и затраты на контроль сварных швов.
Мифы и факты изгиба оправки
Существует много неправильных представлений о предполагаемых рисках изгиба нержавеющей стали на оправке по сравнению с фактическими преимуществами. На самом деле гибка оправки — один из самых точных и экономичных процессов обработки металлов давлением.
- Миф : Гибка не так прочна, как сварка.
Факт : Все фитинги отлиты или изогнуты, и нет никаких доказательств того, что одна из них слабее другой. Фактически, при изгибе некоторые материалы фактически твердеют и становятся прочнее. - Миф : Для труб из нержавеющей стали и их колен после гибки требуется термообработка.
Факт : Аустенитная нержавеющая сталь относится к основному металлу P-№ 8, который можно гнуть в холодном состоянии в соответствии с Кодексом ASME без какой-либо термообработки после изгиба. - Миф : Изгибы не обеспечивают постоянного диаметра, как готовые изгибы.
Факт : Изгибы оправки выдерживаются в рамках тех же требований к толщине стенки и овальности ASME, которые соблюдаются производителями фитингов.С помощью оправки, поддерживающей внутреннюю часть трубы, технические специалисты имеют больше возможностей для точных и повторяемых изгибов. - Миф : Изгиб трубы из нержавеющей стали невозможно выполнить до точного угла.
Факт : Гибка нержавеющей стали на самом деле более точна, чем сварка, из-за деформации сварного шва и посадки при сварке. Гибка с помощью оправки, в частности, предотвращает повреждение трубы, такое как волнистость, сплющивание и сжатие во время процесса.
Как только конечные пользователи и производители откажутся от мифов о гибке на оправке, они смогут воспользоваться преимуществами экономии времени, материалов и затрат, которые дает этот метод обработки металлов давлением.
Производственный процесс
Для крупномасштабных заказов, длинных труб, сложной геометрии или множества углов гибка на оправке становится все более популярным методом изготовления. Для традиционной оснастки требуется матрица для гибки с определенным радиусом, хотя на современных станках используются штабелируемые матрицы для создания деталей с несколькими радиусами изгиба. На некоторых станках гибочный рычаг может поворачиваться, что позволяет создавать симметричные детали на одном и том же инструменте.
Помимо простого управления сложными деталями, гибка на оправке имеет ряд преимуществ по сравнению со сваркой, в том числе:
- Экономия времени — При сравнении сварной трубы под углом 90 ° и трубы, изогнутой под таким же углом, гибка оправки сокращает количество часов изготовления, а также время, необходимое для проверки готовой детали.
Используя гибочные станки с ЧПУ, производители могут сэкономить до 75% времени, необходимого для выполнения каждого сварного шва вручную.
- Экономия затрат — Сгибание нержавеющей стали вместо сварки позволяет сэкономить более 50% затрат, особенно благодаря утомительному визуальному контролю, который требуется для некоторых сварочных норм. По завершении процесса сварки, если требуется неразрушающий контроль, сварные швы должны быть подвергнуты рентгеновскому сканированию, что обходится в сотни долларов за рентгеновское излучение. Для трубы с несколькими сварными швами затраты на осмотр быстро увеличиваются.
- Расходы на материалы и экономия места — Гибка не только сокращает потери материала, поскольку для этого требуются только оригинальные детали, но также экономит драгоценное пространство в вашем цехе, поскольку нет необходимости хранить какой-либо сырой сварочный материал, кроме трубы или сама трубка.
- Экономия трудозатрат — За счет внедрения технологии гибки можно значительно сократить трудозатраты на установку системы трубопроводов, что значительно снижает риск безопасности и / или производственных проблем на месте для владельца / ГК.
- Точность — Гибка труб облегчает создание нестандартных неизометрических углов и дает инженерам повышенную гибкость при создании сложных геометрических фигур. Оборудование для гибки обеспечивает высокоточные воспроизводимые результаты, а оправка поддерживает трубу для устранения деформации. Гибка также более последовательная и уменьшит любые дефекты, которые часто встречаются в процессе сварки.
Хотя характер гибки оправки снижает затраты и обеспечивает высокое качество, повторяемость результатов, принятие дополнительных мер во время процесса заказа может помочь обеспечить эти преимущества.По возможности используйте трубы стандартных размеров и толщины, чтобы сократить затраты и время выполнения заказа. Выбор общего радиуса также сэкономит ваше время и деньги, поскольку нестандартные размеры требуют изготовления штампов по индивидуальному заказу, на приобретение которых нужно время.
Подходит ли для вашей работы гибка труб на оправке из нержавеющей стали?
В следующем контрольном списке перечислены факторы, указывающие на возможности экономии средств и создания добавленной стоимости для вашего бизнеса и услуг. Вы можете обратиться к специалисту по гибке оправок, если:
- У вас есть приложение, в котором требуется полная дренажная способность, когда на внутреннем диаметре трубы или системы трубопроводов нет участков захвата.
- Расход имеет значение — если вашей трубе или системе трубок требуется максимальный расход с минимальными ограничениями
- Вам необходим внутренний диаметр вашей трубки / системы трубопроводов, который необходимо отполировать до определенной степени чистоты
- Для вашей системы требуются нестандартные углы, которых нет в стандартной арматуре
- Вам необходимо неизменно высокое качество ваших трубопроводных систем без возможности появления дефектов сварных швов
- Ваше приложение требует неразрушающего контроля после сварки труб и стыков труб, что требует больших затрат
Если ваш бизнес соответствует любому из вышеперечисленных критериев, вы можете рассмотреть возможность партнерства со специалистом по гибке оправок.
О HPS
Обладая более чем 30-летним опытом, High Purity Systems понимает, насколько высоки ставки в обслуживаемых нами отраслях; во многих случаях безопасность человека зависит от точности сварного шва и чистоты системы. Работая с нашими клиентами, мы стремимся предоставлять услуги высочайшего качества в соответствии со строгими требованиями вашей среды.
Для получения дополнительной информации о том, как HPS может помочь вам в следующем проекте по гибке труб по индивидуальному заказу, свяжитесь с нашей командой сегодня.
Цанговый расширительный стержень-дл | Режущие инструменты и доступ к станкам
Запрос продукта
Выберите CountryAfghanistanAlbaniaAlgeriaAmerican SamoaAndorraAngolaAnguillaAntarcticaAntigua и BarbudaArgentinaArmeniaArubaAustraliaAustriaAzerbaijanBahamasBahrainBangladeshBarbadosBelarusBelgiumBelizeBeninBermudaBhutanBoliviaBosnia и HerzegovinaBotswanaBouvet IslandBrazilBritish Индийский океан TerritoryBrunei DarussalamBulgariaBurkina FasoBurundiCambodiaCameroonCanadaCape VerdeCayman IslandsCentral африканских RepublicChadChileChinaChristmas IslandCocos (Килинг) IslandsColombiaComorosCongoCook IslandsCosta RicaCroatia (Hrvatska) CubaCyprusCzech RepublicDenmarkDjiboutiDominicaDominican RepublicEast TimorEcuadorEgyptEl SalvadorEquatorial GuineaEritreaEstoniaEthiopiaFalkland (Мальвинские) острова Фарерские IslandsFijiFinlandFranceFrance, MetropolitanFrench GuianaFrench PolynesiaFrench Южный TerritoriesGabonGambiaGeorgiaGermanyGhanaGibraltarGuernseyGreeceGreenlandGrenadaGuadeloupeGuamGuatemalaGuineaGuinea-BissauGuyanaHaitiHeard и Mc Острова ДональдаГондурасГонконгВенгрияИсландияИндияОстров Ма nIndonesiaIran (Исламская Республика) IraqIrelandIsraelItalyIvory CoastJerseyJamaicaJapanJordanKazakhstanKenyaKiribatiKorea, Корейская Народно-Демократическая Республика ofKorea, Республика ofKosovoKuwaitKyrgyzstanLao Народная Демократическая RepublicLatviaLebanonLesothoLiberiaLibyan арабских JamahiriyaLiechtensteinLithuaniaLuxembourgMacauMacedoniaMadagascarMalawiMalaysiaMaldivesMaliMaltaMarshall IslandsMartiniqueMauritaniaMauritiusMayotteMexicoMicronesia, Федеративные Штаты ofMoldova, Республика ofMonacoMongoliaMontenegroMontserratMoroccoMozambiqueMyanmarNamibiaNauruNepalNetherlandsNetherlands AntillesNew CaledoniaNew ZealandNicaraguaNigerNigeriaNiueNorfolk IslandNorthern Mariana IslandsNorwayOmanPakistanPalauPalestinePanamaPapua Новый GuineaParaguayPeruPhilippinesPitcairnPolandPortugalPuerto RicoQatarReunionRomaniaRussian FederationRwandaSaint Киттс и NevisSaint LuciaSaint Винсент и GrenadinesSamoaSan MarinoSao Томе и ПринсипиСаудовская АравияСенегалСербияСейшельские островаСьерра-ЛеонеСингапурСловакияСловенияСоломоновы Острова andsСомалиЮжная АфрикаЮжная Джорджия Южные Сандвичевы островаИспания Шри-ЛанкаSt.Елена Пьер и MiquelonSudanSurinameSvalbard и Ян Майен IslandsSwazilandSwedenSwitzerlandSyrian Arab RepublicTaiwanTajikistanTanzania, Объединенная Республика ofThailandTogoTokelauTongaTrinidad и TobagoTunisiaTurkeyTurkmenistanTurks и Кайкос IslandsTuvaluUgandaUkraineUnited арабских EmiratesUnited KingdomUnited StatesUnited Внешние малые islandsUruguayUzbekistanVanuatuVatican города StateVenezuelaVietnamVirgin острова (Британские) Виргинские острова (США) Уоллис и Футуна IslandsWestern SaharaYemenZaireZambiaZimbabwe
Представлять на рассмотрениеИспытания на изгиб оправки
|
Инструменты, оборудование и безопасность строительства | Руководство по охране труда
7.1 Определения Точка обработки означает точку, в которой выполняется резка, формовка, расточка или формовка на заготовке.
Толкатель — это узкая полоска дерева или другого мягкого материала с прорезью на одном конце, которая используется для проталкивания коротких или узких кусков материала через пилу.
Блок означает короткий деревянный брусок, снабженный ручкой, аналогичной ручке рубанка, и выступом на заднем конце, который используется для проталкивания короткой ложи через вращающиеся ножи.
Приспособления и приспособления — это устройства для удержания, поддержки или ограничения движения материала во время выполнения операций.
- Каждая машина должна быть сконструирована так, чтобы не допускать ощутимой вибрации, когда установлен самый большой инструмент и работает на холостом ходу на полной скорости.
- Оправки и оправки должны быть сконструированы таким образом, чтобы иметь прочную и надежную опору и не допускать люфтов.
- Рамы или столы пил должны быть сконструированы с проушинами, залитыми на раме, или с эквивалентными средствами для ограничения размера пильного полотна, которое может быть установлено, чтобы избежать чрезмерной скорости, вызванной установкой пилы большего размера, чем предполагалось.
- Ограждения для циркулярной пилы должны быть сконструированы таким образом, чтобы их можно было надежно прикрепить к столу или сборке стола без изменения их совмещения с пилой. Для пил с наклонными столами или поворотными опорами ограждение должно быть сконструировано таким образом, чтобы оно оставалось на одной линии, параллельной пиле, независимо от угла между пилой и столом.
- Все ремни, шкивы, шестерни, валы и движущиеся части должны быть защищены.
- По возможности, каждая механическая машина должна быть снабжена выключателем, который можно заблокировать в выключенном положении.
- Рамы и все открытые нетоковедущие металлические части переносных электрических машин, работающих под напряжением более 90 В относительно земли, должны быть заземлены. Другие переносные двигатели, приводящие в движение электрические инструменты, которые удерживаются в руке во время работы, должны быть заземлены, если они работают при напряжении более 90 вольт относительно земли. Заземление должно осуществляться через отдельный провод заземления и поляризованную вилку и розетку.
- На рабочем месте должны быть предусмотрены гребни (перина) или подходящие приспособления для использования в тех случаях, когда нельзя использовать стандартное ограждение, например, при нарезании канавок, стыковке, формовании и гребнечесании.
Защитное ограждение настольной пилы должно полностью закрывать часть пилы над столом и часть пилы над разрезаемым материалом. Колпак и крепление должны быть расположены так, чтобы колпак автоматически настраивался на толщину разрезаемого материала и оставался в контакте с ним, не оказывая значительного сопротивления вставке или прохождению распиливаемого материала.
Капюшон должен быть достаточно прочным, чтобы выдерживать удары и деформации, возникающие при разумной эксплуатации, регулировке и обращении.Он также должен защищать оператора от разлетающихся осколков и сломанных зубьев пилы. Он должен быть изготовлен из достаточно мягкого материала, чтобы исключить поломку зуба. Материал не должен разрушаться при разрыве, должен быть невзрывоопасным и не более легковоспламеняющимся, чем дерево. Колпак должен быть установлен таким образом, чтобы его работа была положительной, надежной и точно согласованной с пилой. Крепление должно иметь достаточную прочность, чтобы противостоять любому разумному боковому удару или другой силе, стремящейся выбить его из строя.
Необычные формы: Если защитный кожух не может быть использован из-за необычных форм или разрезов, необходимо использовать приспособление или приспособление, обеспечивающее равную безопасность для оператора. Гребни (перины) или подходящие приспособления должны использоваться, когда нельзя использовать стандартное ограждение, например, при нарезании канавок, стыковке, формовании и нарезке гребней. По завершении таких операций охранник должен быть немедленно заменен.
Толкающая ручка: Толкающая ручка должна использоваться на короткой или узкой ложи или когда есть вероятность контакта руки с лезвием.
Разбрасыватель и устройства защиты от отдачи: Каждая настольная пила должна быть снабжена разбрасывателем, чтобы материал не сдавливал пилу или не отбрасывался на оператора. Распределитель должен быть изготовлен из закаленной стали или ее эквивалента и должен быть тоньше пропила. Он должен быть достаточной ширины, чтобы обеспечивать достаточную жесткость или жесткость, чтобы противостоять любому разумному боковому толчку или удару, имеющему тенденцию сгибать или выбрасывать его из положения. Распределитель должен быть прикреплен так, чтобы он оставался в точном соответствии с пилой даже при наклоне пилы или стола, и должен быть размещен так, чтобы между распределителем оставалось не более половины (1/2) дюйма. и задняя часть пилы, когда в станке установлена самая большая пила.Предоставление расширителя при нарезании канавок, нарезании или выравнивании не требуется. По завершении таких операций следует немедленно заменить разбрасыватель.
7,4 ФуганокНож режущей головки строгального или фуговального станка не должен выступать более чем на одну восьмую (1/8 дюйма) за цилиндрический корпус головки.
Отверстие в столе должно быть как можно меньше. Зазор между краем заднего стола и режущей головкой не должен быть больше одной восьмой дюйма.Отверстие горловины стола не должно быть больше двух с половиной дюймов, когда столы установлены или выровнены друг с другом для нулевого среза.
Защитный кожух фуговального станка должен закрывать всю часть головки с рабочей стороны ограждения или колеи. Защитный кожух должен эффективно препятствовать контакту руки оператора с вращающимися ножами. Защитный кожух должен автоматически регулироваться, чтобы закрывать неиспользуемую часть головы, и должен постоянно оставаться в контакте с материалом.
Защитный кожух фуганка должен закрывать часть задней части калибра или упора.
7,5 Станок токарныйБезопасное и эффективное использование токарного станка по дереву требует изучения и знания процедур использования этого инструмента. Прочтите и полностью усвойте руководство по эксплуатации / эксплуатации. Всегда надевайте защитные очки или защитные очки, которые включают боковые протекторы и, при необходимости, маску, закрывающую все лицо.
Соберите длинные волосы назад. Не надевайте перчатки, свободную одежду, украшения или какие-либо болтающиеся предметы, которые могут зацепиться за вращающиеся детали или аксессуары.
Обратитесь к руководству пользователя / оператора для получения рекомендаций по правильной скорости.Используйте более низкие скорости для деталей большего диаметра или черновых деталей и повышенную скорость для деталей меньшего диаметра и сбалансированных деталей.
Убедитесь, что кожух или кожух ремня на месте. Убедитесь, что все зажимные устройства (замки), например, на задней бабке и упоре инструмента, затянуты.
Проверьте скорость, сверло или инструмент, чтобы убедиться, что они соответствуют размеру, толщине или типу обрабатываемого материала. Сверла и режущие инструменты должны быть острыми, под правильным углом к режущей кромке.Неправильная скорость может привести к поломке, перегреву или повреждению сверла или инструмента.
7.6 Пресс-службаПрессы должны эксплуатироваться в соответствии с рекомендациями производителя. Прессы должны иметь четкую маркировку с указанием грузоподъемности, заявленной производителем, и номинальные характеристики должны быть видны с места работы. Опасности включают опасность от разлетающихся частей деталей, которые могут расколоться или выскользнуть под большим давлением.
Защита операторов. Операторы должны стоять в таком положении или быть защищены охранником от возможных травм из-за отказа пресса, повреждения рабочего материала или других эксплуатационных опасностей.
Инструкция операторам. Операторы должны быть обучены и проинструктированы по безопасным методам работы перед началом работы на прессе. Сотрудник будет контролироваться, чтобы гарантировать правильное использование безопасных процедур.
Рабочая зона. Сотрудники должны поддерживать достаточное расстояние между машинами, чтобы движение одного оператора не мешало работе другого. Также необходимо поддерживать достаточно места для чистки машин, погрузочно-разгрузочных работ, деталей и лома.Все окружающие полы должны содержаться в хорошем состоянии, на них не должно быть препятствий, жира, масла и воды.
Перегрузка. Прессы могут эксплуатироваться только в пределах номинальной грузоподъемности и веса, указанных производителем.
Свобода передвижения. Нажимаемая деталь должна быть без проскальзывания или непреднамеренного движения.
7.7 Пилы радиальныеРадиальная пила может быть защищена фиксированным кожухом, фиксированным защитным ограждением, регулируемым вручную защитным ограждением или стандартным автоматическим регулируемым ограждением.В тех случаях, когда используется альтернативное ограждение фиксированного типа, оно должно обеспечивать защиту, эквивалентную защите, обеспечиваемой автоматически регулируемым ограждением.
Верхний кожух должен полностью охватывать верхнюю часть полотна до точки, которая будет включать конец оправки пилы. Верхний кожух должен быть изготовлен из такого материала, чтобы он защищал оператора от разлетающихся осколков, сломанных зубьев пилы и т. Д. И отклонял опилки от оператора.Стороны нижней открытой части лезвия должны быть защищены до полного диаметра лезвия с помощью устройства, которое автоматически подстраивается под толщину заготовки и остается в контакте с разрезаемой заготовкой, чтобы обеспечить максимальную защиту, возможную во время операции. выполняется.
Должен быть предусмотрен регулируемый упор для предотвращения перемещения лезвия вперед за пределы положения, необходимого для завершения резки.
Установка должна производиться таким образом, чтобы передний конец устройства был немного выше, чем задний, чтобы режущая головка возвращалась в исходное положение следующим образом при отпускании оператором:
- Режущая головка или каретка должны плавным движением вернуться в исходное или исходное положение
- Режущая головка или каретка не должны отскакивать или отскакивать при достижении исходного или исходного положения
- Режущая головка или каретка останутся в исходном или исходном положении
Каждая пила с радиальным захватом, используемая для продольной распиловки, должна быть снабжена пальцами или упорами без отдачи, расположенными с обеих сторон пилы, чтобы противодействовать толчку или тенденции пилы подбирать материал или отбрасывать его назад. Оператор.Они должны быть спроектированы так, чтобы обеспечивать достаточную удерживающую способность для разрезаемого материала любой толщины. Рыхление и вспашка должны производиться против направления вращения пилы. Направление вращения пилы должно быть четко обозначено на кожухе. Кроме того, постоянная этикетка размером не менее 1 ½ на дюйма со стандартными буквами в пропорциях должна быть прикреплена к задней части защитного кожуха примерно на уровне оправки, где зубья лезвия выходят из верхнего кожуха во время работы увидел, прочитав следующее: «Опасно: не срывайте и не пахайте с этого конца.«Цвет этикетки должен быть опасно красным.
Консультации специалиста по расширительным оправкам
Соберитесь, ваш рабочий день скоро претерпит значительные изменения. Как бы трудно ни было в это поверить, после прочтения этой статьи вам больше никогда не придется беспокоиться о выборе подходящей разжимной оправки для конкретной работы.
Шестерни бывают всех форм и размеров, и к ним предъявляются всевозможные требования к точности и геометрическим соотношениям. Производственные чертежи определяют, что нужно проверять, и что делает шестерню «хорошей» или «плохой».Но именно процесс проверки зубчатых колес определяет, соответствует ли зубчатое колесо спецификациям чертежа, а также определяет, правильно ли контролируется производственный процесс.
Старое эмпирическое правило гласит, что ваши измерения должны быть в 10 раз точнее, чем детали, которые необходимо проверить. В мире зубчатых колес это означает, что вам часто нужны оправки, способные удерживать детали в пределах одной или двух десятитысячных дюйма общего показания индикатора (TIR).По мере того, как ваш инструмент становится более точным, он, как правило, становится дороже. Но это также может стать дорогостоящим, если вы отправляете плохие шестерни своим клиентам или если вам нужно выбросить хорошие шестерни из-за того, что используемая оправка не имела необходимой точности. Выбор неправильной оправки для работы может быть дорогостоящим.
Эта статья предназначена для того, чтобы пролить свет на несколько типов оправок, которые используются в процессе проверки зубчатых колес. В частности, в нем рассматриваются типы оправок, которые используются для удержания шестерен между центрами контроля.Пять из наиболее распространенных типов оправок, которые я видел в отделах контроля зубчатых колес, включают 3-кулачковые расширительные оправки LeCount, гидравлические оправки, оправки с прорезями втулки, конические оправки и оправки для гаек. У каждого типа есть свои сильные и слабые стороны.
Трехкулачковые расширительные оправки LeCount сочетают в себе высокую точность с большим диапазоном расширения. В общей сложности 12 оправок покрывают все отверстия диаметром от 0,25 ″ до 7 ″. Эти расширяющиеся оправки будут удерживать шестерни в пределах 0,0001 ″ TIR во всем диапазоне расширения.Для загрузки и разгрузки деталей не нужны инструменты. Просто поместите шестерню на губки, оттяните втулку, пока она не коснется отверстия шестерни, а затем слегка постучите концом оправки по твердой поверхности, например, наковальне или верстаку. Легкое постукивание по противоположному концу освободит деталь. На этих инструментах нет частичных упоров, поэтому осевое положение шестерен будет варьироваться от нагрузки к нагрузке.
Эти раздвижные оправки стоят от 1000 до 2000 долларов каждая, и даже если стоимость может напугать вас на начальном этапе, вложения быстро окупаются, если у вас много деталей разных размеров, большие объемы или жесткие допуски.К особым изменениям этой оправки относится возможность удерживать шестерни с внутренними шлицами. Обладая данными о внутренних шлицах, эти оправки могут быть спроектированы так, чтобы контактировать с зубчатым колесом по его делительному диаметру, малому диаметру или большому диаметру. Эти оправки не рекомендуются для операций механической обработки.
Гидравлические оправки — или «оправки для смазки», как их иногда называют — обладают способностью расширяться примерно на 0,003 дюйма на дюйм в диаметре. Внешняя оболочка оправки вынуждена расширяться, когда гидравлическая жидкость находится под давлением с помощью привода, обычно поворота винта.Они могут быть очень точными, с МДП до 0,00005 ″, хотя 0,0001 ″ МДП кажется рекламируемой нормой. Некоторые компании предоставляют готовые гидравлические оправки для стандартных размеров, но в большинстве случаев они разрабатываются специально для конкретной детали. Ожидается, что срок изготовления нестандартных оправок для консистентной смазки будет в диапазоне от 10 до 15 недель.
Стоимость этих инструментов варьируется от нескольких сотен долларов за готовый продукт до нескольких тысяч долларов за высокоточные инструменты, разработанные по индивидуальному заказу.Изготовить гидравлические оправки для малых отверстий — сложная задача, поэтому не ожидайте их использования на шестернях с внутренним диаметром менее полдюйма. Если ваши шестерни имеют внутренние шлицы, эти оправки могут быть изготовлены со шлицевой внешней оболочкой, которая предназначена для контакта с делительным диаметром или большим диаметром (никаких модификаций для контакта с меньшим диаметром не требуется). Гидравлические оправки могут использоваться для обработки, если они предназначены для обработки.
Оправки втулки с прорезями состоят из двух основных компонентов: конического вала и втулки с прорезями.Прорези во втулке позволяют ей увеличиваться в диаметре по мере того, как она приводится в движение по конической оправке с помощью гайки или оправочного пресса, и они имеют диапазон расширения около 0,015 дюйма, а в некоторых случаях — до 0,125 дюйма. Если вы можете жить с 0,0005 ″ TIR, типичным для этих инструментов, диапазон расширения — в сочетании с низкой стоимостью (часто менее 100 долларов США) — делает этот элемент очень популярным. Чтобы снизить цену, вы часто можете найти наборы, которые имеют одну коническую оправку с несколькими сменными шлицевыми втулками разного диаметра.Оправки с шлицевой гильзой можно использовать как для обработки, так и для контроля. Некоторые стили предлагают повторяемое осевое расположение шестерен, а другие — нет. Часто заказчику необходимо отшлифовать шлицевую втулку до диаметра, подходящего для шестерни. Конические оправки — наименее дорогие и самые простые из расширительных оправок, и их часто изготавливают на собственном производстве. Эти оправки отшлифованы с небольшим сужением от одного конца до другого. Конусность может составлять всего 0.0002 ″ на дюйм и до 0,0005 ″ на дюйм. На малый конец оправки помещается шестерня, которая скользит вдоль оси до контакта с оправкой. Легкое постукивание по большому концу оправки установит шестерню. Эти инструменты особенно популярны для обработки отверстий малого диаметра, где сложно изготовить механическую расширительную оправку.
Самым большим недостатком этого типа инструмента является то, что шестерня удерживается только на одном конце отверстия (на противоположном конце будет зазор), что делает вероятным, что он не будет удерживаться прямо.В зависимости от допусков это может быть проблемой, а может и не быть. Кроме того, если допуск на диаметр отверстия больше, чем на конус, вам потребуется более одной оправки для работы. Поиск оправки с правильной посадкой может занять много времени, поскольку вы обрабатываете шестерню за шестерней, а если у вас много деталей разных размеров, вы можете получить довольно большое количество оправок. Фактически, я получил письмо от клиента, в котором говорилось, что он смог выбросить 500 конических оправок и заменить их одной расширительной оправкой с 3 кулачками.Это на 499 меньше оправок, которые нужно периодически инвентаризировать и калибровать!
Если используется оправочный пресс, для обработки можно использовать конические оправки. Коническая оправка обеспечивает наихудший случай повторяемости осевого расположения; изменение диаметра на одну десятую дюйма может изменить осевое положение на дюйм. В эти оправки можно шлифовать конические шлицы, что делает их пригодными для использования на шестернях с внутренними шлицами.
Оправки для гаек — еще один распространенный инструмент для удержания шестерен.Этот инструмент имеет посадку с зазором в отверстии шестерни. Гайка используется для зажима шестерни до упора на оправке. В этом случае первичной точкой отсчета является поверхность шестерни, а не отверстие. У этой оправки должен быть достаточный зазор, чтобы соответствовать допуску отверстия, в противном случае вам может потребоваться более одной оправки. В любом случае повторяемость радиального биения будет не лучше половины диаметрального зазора между отверстием и оправкой.
Преимущество оправки для гаек заключается в том, что деталь всегда находится в одном и том же осевом положении, независимо от изменения размера отверстия в партии, а стоимость относительно невысока; За несколько сотен долларов вы получите специальный инструмент для работы.Также не редкость, когда эти инструменты изготавливаются собственными силами, если на вашем предприятии есть инструментальный цех, поскольку их довольно просто построить. Оправки для гаек также довольно распространены в процессах обработки.
Теперь, вооружившись этими знаниями, вы готовы взяться за работу — любую работу — с душевным спокойствием, которое может принести только использование правильного расширительного стержня.
.