Оправки контрольные для проверки станков
Контрольные оправки KEMMLER с хвостовиком SK по DIN 69871
Высококачественные расширяющиеся оправки Em Ms2 Ms3 Ms4 Ms5 Станки Токарный станок с ЧПУ Держатель инструментаРАСШИРЕННЫЕ МАНДРЕЛИ
Добро пожаловать на ссылку, чтобы узнать больше.
У нас есть собственный завод, у нас 220 рабочих и 12 инспекторов.
Наши инженеры работают в этой области более 3 лет, и у них богатый опыт и они очень серьезны.
Мы создали независимую коммерческую компанию в 2003 году, у нас 20 продаж.
Наши продукты были одобрены многими странами, включая Германию, Турцию, Бразилию, Италию, Англию, Америку, Индию и так далее.
Добро пожаловать на наш сайт! Www.ht-tools.net
Преимущества продукта:
1. Богатая продукция
2. Длительный срок службы, стабильное качество продукции и стабильная точность
3. Сосредоточение внимания на деталях производства продукции
4. Твердая и красивая упаковка
5. Можно настроить
Наши услуги
1.OEM сервис
2.Быстрый ответ в течение 24 часов
3. Большая емкость
4. Короткое время доставки.
Скидки на продукт
Все продукты
Преимущество компании:
1.Имеют сильную команду продаж и богатый опыт в области экспорта внешней торговли
2. Бренд HT-TOOLS имеет долгую историю
3. Компания основала внешнеторговую компанию с 2003 года и обладает богатым опытом и ресурсами в течение 16 лет.
4. Четкое разделение труда между департаментами
5. Компания расположена на крупнейшей в Китае базе для производства и обработки принадлежностей для станкостроения, и в ней насчитывается до 200 заводов по изготовлению деталей для простых станков.
Мастерская
Основная продукция:
Комплектующие для станков, пожалуйста, проверьте ниже, чтобы узнать наши основные позиции.Держатели инструмента
Хвостовики: держатели инструмента BT, держатели инструмента DIN69871 SK, оснастка NT, держатели инструмента CAT30 CAT40, держатели инструмента HSK, держатели инструмента
DIN 69880 VDI, конус Морзе, держатели инструмента с прямым хвостовиком и т. Д.
: цанговые патроны, патроны фрезерные, торцевые фрезы, держатели концевых фрез Weldon, переходники конусности Морзе
, патроны сверлильные, патроны резьбонарезные, патроны концевые фрезерные, держатели инструмента концевых фрез,
винт в держателях фрезы и т. Д. Коллет: Цанги ER, Цанги ERC, Цанги ERG, Набор фрезерных патронов, Прямые цанги, Цанги OZ и т. Д.Принадлежности
: втулка держателя инструмента, гайка и гаечный ключ, цапфа, зажимное устройство держателя инструмента
, тиски станка, живой центр и т. Д.
FAQ
1. Вы фабрика или торговая компания?
Мы индустрия и торговая интеграция.
2. Не могли бы вы предоставить образцы?
Да, мы можем.
3. Куда вы экспортируете?
Весь мир.
4. Можете ли вы производить нестандартную продукцию?
Да, мы можем.Пожалуйста, предоставьте образцы или чертеж.
5. Какова точность ER Collet?
У нас есть три вида. 0,005 мм 0,01 мм и 0,015 мм.
6. Какие способы доставки?
Международный экспресс, по воздуху и по морю все в порядке.
7. У вас есть минимальный объем заказа?
Обычные продукты не имеют. Минимальный объем заказа нестандартной продукции составляет 50 шт.
8. Какой способ оплаты?
T / T, Pay Pal, Western Union и так далее.
9. Каков срок доставки?
5-20 дней после подтверждения заказа
10. Какая у вас посылка?
Нейтронная упаковка без марки, пластиковая коробка, коробка и тд. Если ваше количество хорошо, мы можем упаковать с вашим требованием.
Для получения дополнительной информации, пожалуйста, свяжитесь со мной
,станок | Описание, история, типы и факты
Станок , любой стационарный станок с механическим приводом, который используется для формовки или формирования деталей из металла или других материалов. Формирование осуществляется четырьмя основными способами: (1) путем вырезания из детали лишнего материала в виде стружки; (2) срезая материал; (3) путем сжатия металлических частей до желаемой формы; и (4) применяя к материалу электричество, ультразвук или едкие химические вещества. Четвертая категория охватывает современные станки и процессы для обработки сверхтвердых металлов, не обрабатываемых старыми методами.
буровой пресс Бурильный пресс. Plbcr Станки, которые формируют детали путем удаления металлической стружки из заготовки, включают в себя токарные станки, формовочные и строгальные станки, сверлильные станки, фрезерные станки, шлифовальные станки и электропилы. Холодное формование металлических деталей, таких как кухонная утварь, автомобильные кузова и подобные предметы, выполняется на штамповочных прессах, в то время как горячее формование каленых заготовок в штампы соответствующей формы выполняется на ковочных прессах.
Современные станки режут или формируют детали с допуском плюс-минус одна десятитысячная дюйма (0.0025 мм). В особых случаях прецизионные притирочные станки могут производить детали с точностью до плюс-минус двух миллионных долей (0,00005 миллиметра). Из-за точных требований к размерам деталей и значительных сил резания, действующих на режущий инструмент, станки сочетают в себе вес и жесткость с деликатной точностью.
История
До промышленной революции 18-го века для резки и придания формы материалам для производства таких товаров, как кухонные принадлежности, вагоны, корабли, мебель и другие изделия, использовались ручные инструменты.После появления парового двигателя материальные товары производились на механических машинах, которые могли изготавливаться только станками. Станки (способные производить точные детали в больших количествах), а также приспособления и приспособления (для удержания работы и направления инструмента) были необходимыми инновациями, которые сделали массовое производство и взаимозаменяемые детали реальностью в 19 веке.
Самые ранние паровые двигатели страдали от неточности ранних станков, и большие литые цилиндры двигателей часто были неточно утомлены машинами, приводимыми в движение водяными колесами, и первоначально предназначались для выведения из пушки. В течение 50 лет с момента появления первых паровых двигателей были разработаны и разработаны основные станки со всеми основными характеристиками, необходимыми для обработки тяжелых металлических деталей. Некоторые из них были приспособлениями более ранних деревообрабатывающих станков; металлический токарный станок, полученный из токарных станков, которые использовались во Франции еще в 16 веке. В 1775 году Джон Уилкинсон из Англии построил высокоточный станок для расточки цилиндров двигателя. В 1797 году Генри Модсли, тоже из Англии и один из величайших изобретательных гениев своего времени, спроектировал и построил токарно-винторезный станок. Отличительной особенностью токарного станка Maudslay был ходовой винт для привода каретки. Направленный на шпиндель токарного станка, ведущий винт продвигал инструмент с постоянной скоростью и гарантировал точную резьбу винта. К 1800 году Модслей оснастил его токарным станком 28 сменными шестернями, которые нарезали резьбу с различными шагами, контролируя отношение скорости ходового винта к скорости шпинделя.
Формирователь был изобретен Джеймсом Насмитом, который работал в магазине Генри Модсли в Лондоне. В станке Насмита заготовка может быть прикреплена горизонтально к столу и обработана резцом с помощью возвратно-поступательного движения, чтобы выровнять небольшие поверхности, прорезать пазы или обработать другие прямые поверхности. Несколько лет спустя, в 1839 году, Насмит изобрел паровой молот для ковки тяжелых деталей. Другой ученик Модсли, Джозеф Витворт, изобрел или усовершенствовал множество станков и стал доминировать в этой области; на Международной выставке 1862 года экспонаты его фирмы занимали четверть всего пространства, посвященного станкам.
Великобритания пыталась удержать лидерство в развитии станкостроения, запретив экспорт, но эта попытка была обречена на промышленное развитие в других местах. Британские инструменты экспортировались в континентальную Европу и в Соединенные Штаты, несмотря на запрет, и новые инструменты были разработаны за пределами Великобритании. Среди них был фрезерный станок, изобретенный Эли Уитни, который был произведен в Соединенных Штатах в 1818 году и использовался Симеоном Нортом для производства огнестрельного оружия. Первый полностью универсальный фрезерный станок был построен в 1862 году Дж.Р. Браун из США и был использован для резки спиральных канавок в спиральных сверлах. Станок с револьверной головкой, также разработанный в Соединенных Штатах в середине 19-го века, был полностью автоматическим в некоторых операциях, таких как изготовление винтов, и он предвосхитил важные события 20-го века. Различные зуборезные машины достигли своего полного развития в 1896 году, когда американец Ф. У. Феллоуз разработал формирователь зубчатых колес, который мог быстро крутить практически любой тип зубчатых колес.
Производство искусственных абразивов в конце 19 века открыло новую область станков — шлифовальных станков.C.H. Нортон из Массачусетса наглядно проиллюстрировал потенциал шлифовальной машины, создав такую, которая могла бы размолоть коленчатый вал автомобиля за 15 минут — процесс, который раньше занимал пять часов.
К концу 19-го века произошла полная революция в обработке и обработке металлов, которая создала основу для массового производства и индустриального общества. В 20-м веке были представлены многочисленные усовершенствования станков, такие как многоточечные фрезы для фрезерных станков, развитие автоматизированных операций, управляемых электронными и жидкостными системами управления, и нетрадиционные методы, такие как электрохимическая и ультразвуковая обработка. Тем не менее, даже сегодня основные станки остаются в значительной степени наследием 19-го века.
Характеристики станков
Все станки должны иметь приспособления для удержания и крепления инструмента и средства для точного контроля глубины резания. Относительное движение между режущей кромкой инструмента и работой называется скоростью резания; Скорость, с которой необработанный материал входит в контакт с инструментом, называется движением подачи. Средства должны быть предоставлены для того и другого.
Поскольку перегретый инструмент может потерять свою режущую способность, необходимо контролировать температуру. Количество выделяемого тепла зависит от силы сдвига и скорости резания. Поскольку усилие сдвига изменяется в зависимости от материала, подлежащего резке, и материал инструмента изменяется с учетом его устойчивости к высоким температурам, оптимальная скорость резки зависит как от материала, который режется, так и от материала режущего инструмента. На это также влияет жесткость станка, форма заготовки и глубина резания.
Металлорежущий инструмент классифицируется как одна точка или несколько точек. Одноточечный режущий инструмент можно использовать для увеличения размера отверстий или расточки. Токарные и расточные работы выполняются на токарных и расточных станках. Многоточечные режущие инструменты имеют две или более режущих кромок и включают в себя фрезы, сверла и протяжки.
Существует два типа операций; Либо инструмент движется по прямому пути к неподвижной заготовке, как на формирователе, либо заготовка движется к неподвижному инструменту, как на строгальном станке.Необходимо предусмотреть разгрузочные или зазорные углы, чтобы поверхность инструмента ниже режущей кромки не терлась о заготовку. На режущих инструментах часто предусмотрены углы граблей, чтобы вызвать заклинивание при образовании стружки и уменьшить трение и нагрев.
Handy Tool: Расширение оправок для токарной обработки
У нас есть отличная страница с кратким описанием решений для токарных и токарных станков. Одна из лучших вещей в этом — это изящная таблица справа вверху, которая позволяет сравнивать и сопоставлять различные решения для рабочих столов с разных точек зрения. Страница подробно описывает каждое решение и содержит подробную информацию о:
- Цанги
- : включая преимущества и недостатки по сравнению с патронами с мягкими губками для ЧПУ.
- 3-челюстной патрон с мягкими челюстями: видео о том, как делать мягкие челюсти.
- 3-х кулачковых зажимных патрона
- Челюсти с 4 челюстями: Хотите узнать самый быстрый способ набора номера с 4 челюстями?
- 6-кулачковые патроны
- поворот между центрами
- Постоянное вращение лица: современная альтернатива повороту между центрами
- Расширяющие оправки
Последний новый раздел, который я только что добавил на страницу.
Расширяющие оправки— это не решение, которое вы используете каждый день, но они идеально подходят для:
— Удерживание тонкостенных деталей, которые могут быть деформированы при воздействии слишком большого давления внешней силой зажима.
— Удерживающие детали, внешние поверхности которых должны быть обработаны за одну операцию.
— Удерживающие детали, которые имеют много разных наружных диаметров, и особенности, которые иначе было бы трудно зажимать снаружи.
Они ограничены величиной силы резания, которая может быть приложена без вращения детали на оправке.
Расширяющие оправки захватывают деталь, расширяясь у стенок внутреннего отверстия. Вот типичный пример:
Как правило, они работают, затягивая в центре винт, который заставляет листья оправки расширяться и захватывать внутреннее отверстие детали.Можно обработать профиль на оправке, чтобы соответствовать детали со сложной внутренней геометрией. Также часто можно увидеть их с плечами, чтобы найти конец части и другие подобные функции.
Оправки не имеют большого диапазона движений, поэтому их обычно обрабатывают для нужд конкретной детали.
На фото изображен простой механический тип, но вы также можете приобрести расширяющиеся оправки с механическим приводом. Вот что делает Royal:
Механическая оправка, подобная этой, может быть хорошим выбором для вспомогательного шпинделя на токарном станке с ЧПУ, потому что они сцепляются без какой-либо возможности повреждения внешней поверхности и обеспечивают полный доступ для обработки этой поверхности за одну операцию.
Обязательно ознакомьтесь с другими решениями для рабочих столов на странице, и вы можете добавить эту страницу в закладки, чтобы была удобна быстрая справочная таблица вверху.
Как то, что вы читаете на CNCCookbook?
Присоединяйтесь к 100 000+ CNC’еров! Получайте наши последние сообщения в блоге прямо на вашу электронную почту один раз в неделю бесплатно. Кроме того, мы предоставим вам доступ к некоторым отличным справочным материалам с ЧПУ, включая:
- Наш большой список из более 200 советов и приемов с ЧПУ
- Наш бесплатный курс по основам программирования GCode
- И больше!
Просто введите ваше имя и адрес электронной почты ниже:
100% конфиденциальность: мы никогда не будем спамить вас!Больше статей вам может понравиться:
.
Инструмент для проверки станков на точность
ИНСТРУМЕНТ для ПРОВЕРКИ СТАНКОВ НА ТОЧНОСТЬ [c.239]Инструмент для проверки станков на точность включает проверочную линейку, щупы, уровень, контрольные оправки, индикатор и угольники. [c.239]
Для проверки станков на точность применяются точные и чувствительные инструменты и приборы поверочная линейка, простая контрольная линейка, лекальная и граненая стальные линейки, угольники, щуп, эталонные плитки, конусная и цилиндрическая оправка, индикатор, уровень, оптические приборы и т. д. [c.103]
Для выяснения влияния на точность обрабатываемых деталей жесткости самих деталей, инструмента и деталей станка производят проверки станков на жесткость. [c.433]
Для широкоуниверсальных станков класса точности П, на которых часто выполняют обработку отверстий мерным и регулируемым инструментом, предусмотрена проверка точности растачивания отверстий в чугунном образце (см.
Контроль осуществляется в следующем порядке. Рабочий, наладчик или производственный мастер вызывает контролера своего участка для контроля первых изготовленных деталей обрабатываемой партии. Деталь проверяют непосредственно у рабочего ме.ста или в контрольном пункте, если требуется применение стационарных приборов. Одновременно контролер проверяет соответствие ма- териала детали чертежу (по маркировке материала), правильность соблюдения технологического процесса, соответствие применяемого инструмента, исправность приспособления и точность соблюдения сроков периодической проверки оснастки и оборудования (по датам сроков очередной проверки, указанным на приспособлении и, на станке).
Для обеспечения высокого качества нарезаемых зубчатых колес необходимо периодически проверять оборудование, режущий инструмент, оправки, втулки и кольца на точность, а также контролировать правильность настройки станка. Зуборезные станки должны иметь паспорта точности, в которые заносятся результаты регулярной проверки точности станков. При нарушении точности или неисправности механизмов станка, влияющих на точность зубчатой передачи, работа на станке за исключением черновых проходов должна быть запрещена. [c.446]
Для проверки на геометрическую точность станка ГОСТом установлены параметры и методы проверки их. Проверка станков по нормам точности заключается в установлении точности изготовления, взаиморасположения, перемещения и соотношения движений рабочих органов станка, несущих заготовку и инструмент, путем измерений с помощью приспособлений и приборов, а также путем промеров обработанных на станках образцов деталей.

Завод-изготовитель несет ответственность за качество и режущую способность поставляемого инструмента и в случае рекламации обязан взять его обратно от потребителя. Для проверки режущих свойств инструмент подвергается испытанию в работе. В качестве обрабатываемого материала принимается сталь марки 40 или сталь Ст. 6 твердостью НВ 160—190. Испытание инструмента производится на соответствующих станках, удовлетворяющих требованиям их точности. В качестве охлаждающе-смазывающей жидкости применяют 5%-ный по весу раствор эмульсии в воде с расходом не менее 5 л мин. Проверяемый инструмент в зависимости от его вида должен обработать или определенное количество отверстий (например, инструмент для обработки отверстий), или пройти установленную общую длину прохода (например, фрезы и др.). Условия испытаний и режимы обработки указаны в соответствующих стандартах.
Методы и средства измерения основных поверхностей. Обработанная деталь всегда отличается от абсолютно точной детали формой и размерами. Чем меньше отличие, тем точнее будет деталь. Отклонения реальной поверхности детали от геометрической ограничиваются допуском на размер. Размеры обрабатываемых заготовок измеряют различными инструментами. Для менее точных измерений используют линейки, кронциркули и нутромеры, а для более точных — штангенциркули, микрометры, калибры и др. Линейка служит для измерения длин деталей. Наиболее распространены стальные линейки длиной 150—300 мм с миллиметровыми делениями. Кронциркуль — наиболее простой инструмент для приближенных измерений наружных размеров обрабатываемых заготовок. Для измерений внутренних размеров служит нутромер. Точность измерения линейкой, кронциркулем и нутромером не превышает 0,25 мм. Более точным инструментом является штангенциркуль, которым можно измерять как наружные, так и внутренние размеры обрабатываемых заготовок штангенциркуль можно использовать также для измерения толщины стенок детали и глубины выточки или уступа. Для контроля точности обработки деталей на металлорежущих станках и проверки точности самого станка применяют индикатор.
Износ отдельных частей и деталей станка ведет к потере точности его работы. Поэтому для определения неполадок станка, влияющих на точность и качество обработки, применяют проверку точности станков, которую производят лекальными линейками, проверочными угольниками, индикаторами, контрольными оправками и другими видами поверочных инструментов. Разработаны виды и приемы проверок точности станков, в которых регламентируются допустимые неточности в их работе. [c.49]
Индикаторы предназначены для проверки на точность узлов токарного станка, установки предварительно обработанных деталей, проверки биения, овальности, конусности цилиндрических поверхностей. В сочетании с нутромерами, глубиномерами и другими инструментами они используются для измерения внутренних и наружных размеров, параллельности, плоскостности и т. д.
Кинематическая погрешность возникает в зубчатом колесе в результате радиальных ошибок обработки — непостоянства радиального положения оси заготовки и инструмента, а также тангенциальных ошибок — погрешности обката зубообрабатывающего станка. Это дает возможность выявлять кинематическую погрешность колеса раздельным контролем геометрической составляюш,ей, нормируемой в стандарте радиальным биением зубчатого венца во или колебанием измерительного межцентрового расстояния за оборот колеса при комплексной двухпрофильной проверке Да и тангенциальной составляющей, выясняемой определением погрешности обката или же колебанием длины общей нормали в колесе Лд Ь. Поскольку контролем этих двух составляющих выясняется полная кинематическая погрешность колеса, стандарт разрешает компенсацию одной погрешности за счет другой. Например, тщательная установка колеса на станке позволяет не полностью использовать допустимое отклонение на геометрическую составляющую и вместо этого допустить некоторое превышение погрешности, возникающей от станка. Суммарная погрешность в этом случае не должна превышать допускаемой величины или суммы отклонений, предусмотренных стандартом для колес данной степени точности, т. е.
Отдельные авторы предлагают принимать размер, совпадающий с серединой поля допуска, в качестве настроечного для всех процессов обработки.

От качества наладки станка зависит точность изготовляемого зуборезного инструмента. Порядок наладки следующий. Наладчик просматривает качество прилегания и состояние центров в передней и задней бабках и их соосность.
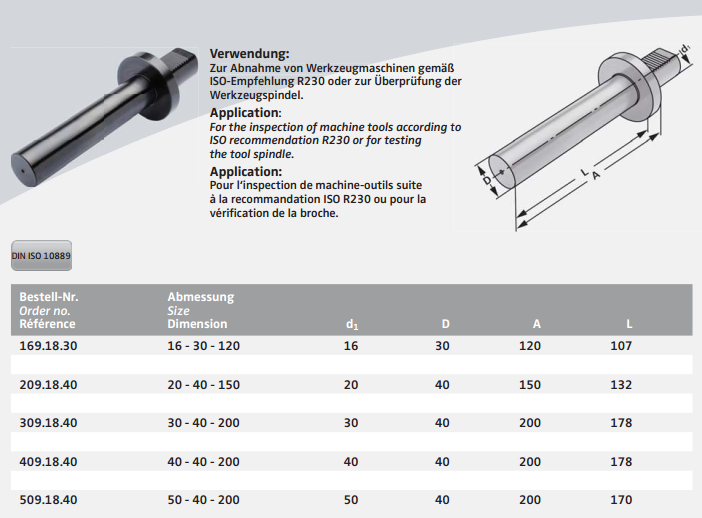
Метод установки и проверка сборки станков и механизмов автоматической линии. Вначале необходимо отладить и проверить собранные позиционные станки и механизмы, которые являются составной частью автоматической линии. После проверки оборудования устанавливают позиционные станки на расстоянии, равном шагу транспортера. Затем монтируют гидроприводы, блоки транспортеров, столы подъема и опускания, насосные станции для подачи смазочно-охлаждающей жидкости на режущий инструмент и смыва стружки. После этого собирают транспортеры подачи и возврата, затем собирают гидроцилиндры транспортеров, трубопроводы, а также монтируют силовую электропроводку для приведения в действие механизмов по удалению стружки и промывки спутника вместе с деталью в специальных камерах. После сборки автоматическую линию проверяют на точность. Вначале проверяют позиционные станки. Необходимо, чтобы горизонтальные планки столов находились в одной плоскости, при этом отклонение не должно превышать
[c.364]
Для определения отклонений осевого шага зубчатых колес от номинального значения [Рр пг) ГОСТ 5368—73 предусмотрены специальные станковые приборы. Этот показатель точности может быть проверен универсальным контактомером БВ-5028 с помощью специального приспособления. Контроль осевого шага особенно важен для крупногабаритных зубчатых колес, у которых погрешности данного показателя вызывают быстрый износ зубьев. Для проверки осевого шага крупногабаритных колес с модулем от 2 до 12 мм непосредственно на зубошевинговальном станке модели 5706 Челябинский завод мерительных инструментов выпускает прибор БВ-5014.
[c.191]
Новые или отремонтированные станки проходят испытания для проверки качества их изготовления или ремонта. С этой целью станки подвергают испытанию на геометрическую точность, на шероховатость поверхности и точность обработанных деталей. Перед испытанием станок устанавливают на фундамент, выверяют по уровню и проверяют геометрическую точность станка. Геометрическая точность станка определяется проверкой точности взаиморасположения, перемещения и соотношения движения рабочих органов, несущих обрабатываемую деталь и инструмент. Проверяемые параметры, методы контроля и нормы точности, в зависимости от конструкции станка и его точности, регламентированы соответствующими ГОСТами или специальными техническими условиями. [c.246]
Под наладкой токарно-револьверного станка понимается ряд мероприятий, выполняемых для того, чтобы на станке можно было обрабатывать заданные заготовки с требуемой чистотой, точностью и производительностью. В наладку станка на выполнение заданной работы входит установка закрепляющего обрабатываемую заготовку устройства (патрона, оправки и т. п.) установка державок для закрепления обрабатывающих инструментов, установка режущих инструментов установка упоров для обрабатываемого пруткового материала и режущих инструментов установка рукояток коробки скоростей и коробки подач для получения соответствующих требуемой скорости и требуемой подачи смазка станка перед его пуском подвод смазочно-охлаждающей жидкости сразу после начала резания выполнение двух-трех деталей и проверка их по соответствующим калибрам и шаблонам.
[c.108]
Одних геометрических проверок для станков недостаточно, так как при этом учитывают (или недостаточно учитывают) жесткость деталей станка, качество их обработки и сборки, не говоря уже о влиянии жесткости системы станок — приспособление— инструмент — заготовка на точность обработки. Государственными стандартами предусмотрена обязательная проверка точности станка путем обработки образца и одновременно проверка шероховатости поверхности обрабатываемой детали.
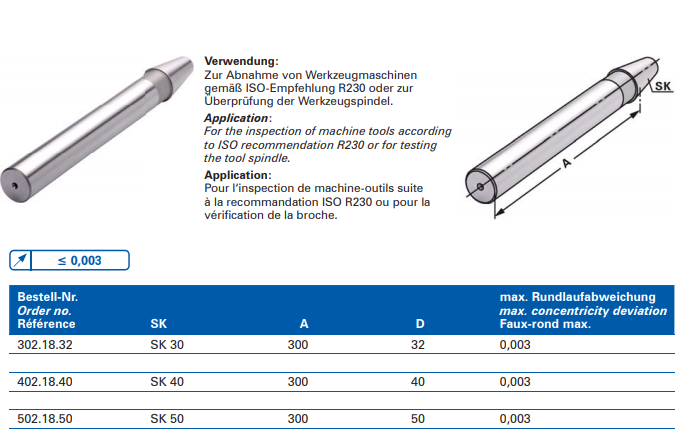
Нормальные приспособления к индикаторам включают стойку с круглым или с прямоугольным столиком для проверки калибров грубых классов точности и небольших изделий, стойку с призматическим основанием для проверки взаимного расположения деталей машин и станков в собранном виде и приспособление для проверки в центрах на биение инструментов и изделий. [c.640]
Контроль геометрической точности станка позволяет получить сведения о всех основных погрешностях изготовления и сборки станка, влияющих на точность обработки заготовок. Для этого стандартами предусмотрен ряд проверок, которые можно разделить на две группы А — проверки геометрических погрешностей станка, влияющих на точность положения заготовки на столе и на точность выполнения заданных перемещений заготовки по отношению к инструменту Б — проверки геометрических погрешностей станка, вызывающих погрешности положения инструмента по отношению к заготовке.
[c.9]
Контрольные диски служат для проверки точности вращения шпинделя и опорных шайб, фланцев круглопильных и шипорезных станков. Диск изготовляют достаточно жестким с параллельными плоскостями, которые используют при измерении торцового биения индикатором. Диск крепят на шпинделе вместо режущего инструмента и производят проверку при проворачивании шпинделя вручную. [c.60]
Перед чистовым проходом необходимо обязательно производить смену инструмента независимо от величины его притупления. Исключение допускается при машинном времени чистового прохода меньше 2—3 час. Смена инструмента, изменение режимов резания и остановка станка при чистовом проходе не допускаются. Перед чистовым проходом ответственных зубчатых колес с диаметром более 500 мм обязательно проводится контрольная проверка и выверка заготовки. Прежде чем выполнить чистовое нарезание зубьев, делают так называемый пробный заход по длине зуба, необходимый для получения обкатанного профиля и позволяющий делать промеры зубомерным инструментом. При пробном проходе проверяют размеры и чистоту поверхности профиля зуба, а также величину припуска, подлежащего снятию при чистовом проходе. При выборе станка для зубофрезерования рекомендуется назначать станок возможно меньшего размера, учитывая резкое повышение стоимости станка при увеличении его размеров. Однако, несмотря на это, при нарезании зубчатых колес 7 степени точности и выше диаметр нарезаемого колеса не должен превышать диаметра делительного больше чем на 50%. Наибольший модуль нарезаемого колеса при этом назначается на два модуля меньше, чем указано в характеристике станка, а вес заготовки не должен превышать допустимую грузоподъемность станка.
[c.436]
Многоцелевые станки с ЧПУ (обрабатывающие центры) с середины 70-х годов стали выпускаться в СССР и за рубежом во все возрастающих количествах. Они позволяют при применении спутников автоматизировать выпуск широкой номенклатуры корпусных деталей и являются одним из основных видов оборудования ГАП, Уже работают ГПС, обеспечивающие изготовление 100—300 деталей различных наименований. Обрабатывающие центры снабжены суппортами, шпинделями, подача которых контролируется встроенными датчиками, поворотными столами также со встроенными датчиками, что обеспечивает возможность программируемого поворота на большое число различных углов револьверными головками или магазинами с числом инструментов, составляющим десятки и сотни штук датчиками касания для проверки правильности и базирования спутников или деталей, контроля закрепления детали, распределения припусков и точности. Датчики касания могут быть использованы и как средства диагностирования. Установка на нуль датчиков станка может быть проверена с помощью датчиков касания (нулевых головок) и специальных базовых поверхностей на станине станка. Таким же образом могут быть измерены тепловые деформации шпинделя. Ряд станков оснащен средствами автоматизации загрузки устройствами автоматической смены поддонов-спутников и средствами распознавания маркировки поддонов. Предусматривается возможность загрузки и разгрузки поддонов с помощью автоматических транспортных тележек и промышленных роботов, применяются средства счета обработанных деталей и планирование смены инструмента по времени его работы.
Решаются вопросы диагностирования состояния инструмента. Для этого применяется ряд методов контроль по величине усилий резания (тензометрирование на резцедержке) контроль усилий, действующих на переднюю опору шпинделя (тензометрирование наружного кольца подшипника) определение
[c.145]
Методы контроля обработки зубчатых колес Целью контроля колес, кроме проверки их как готовой продукции, является также определение погрешностей зубонарезных и других станков, на которых производилась обработка, и выявление состояния, применяемого для обработки режущего инструмента. Контроль производится как по элементам точности (шаг, профиль, эксцентрицитет), так и комплексно — в зацеплении с эталоном. [c.183]
Соответствие основных положений разработанной методики фактическим результатам проверялось в производственных условиях. Отверстия в отлитых корпусных деталях из серого чугуна СЧ 28-48 растачивали на горизонтально-расточном станке мод. 2622 инструментом, оснащенным твердым сплавом В Кб и ВК8. Проверка расчетных параметров обработки на каждом технологическом переходе показала хорошую сходимость результатов (рис. 36). Разработанные методика и программа позволяют проследить изменение точности обработки по переходам от заготовки до готовой детали (кривая 1 на рис. 36, а). Для сравнения показано изменение точности по переходам определенной по таблице средней экономической достигаемой точности (кривая 2) и полученной экспериментально при растачивании отверстия с расчетными режимами обработки (кривая 3). Определение точности по таблицам дает погрешность, так как здесь не учитываются конкретные условия обработки. Аналогичное явление имеет место при изменении высоты неровностей Rz по переходам (рис. 36,6). На рис, 36, в показано изменение смещения оси растачиваемого отверстия по переходам. По сравнению с табличными данными большая погрешность возникает при нежесткой технологической системе (кривая 4).
[c.112]
Периодический контроль оснастки производится по специальному графику. График контроля производственной оснастки составляется отделом технического контроля и согласовывается с мастерами и с начальником цеха. Мастер должен, руководствуясь этим графиком, своевременно возвращать с рабочих мест в кладовую назначенные к проверке инструменты и приспособления. В тех случаях, когда приспособления, кондукторы или другая оснастка проверяется непосредственно на рабочем месте, мастер должен на необхо.цимое для проверки время освободить станок от работы и подготовить его и оснастку к проверке. Производственному мастеру следует повседневно руководствоваться правилом качество обработки и точность размеров обрабатываемых деталей прямо зависят от качества применяемых для обработки инструментов.
[c.330]
Следует сказать о некоторых особенностях безопасного труда и обслуживания станков строгальной группы с ЧПУ. Как правило, станки с ЧПУ обслуживают оператор и наладчик. Оператор должен соблюдать все правила безопасности работы на строгальных и долбежных станках, изложенные выше перед началом работы он должен проверить работоспособность станка с помощью тест-программы, проконтролировать работу устройств с ЧПУ, убедиться в подаче смазки, наличии масла в гидросистеме, проверить работу офаничивающих упоров.


На рабочем чертеже зубчатого колеса наряду с конструктивными размерами должны быть указаны (в табличке) 1) класс точности по ГОСТ 2) число г зубьев 3) модуль т ъ мм, а для колес непрямозубых — модули нормальный и торцевой в ММ-, 4) угол профиля исходного контура 5) номер сопряженного зубчатого колеса 6) угол р наклона косых (винтовых) зубьев или средний угол спирали криволинейных зубьев для конических к олес 7) направление зубьев (иравовинтовые или левовинтовые) 8) для исправленных колес коэфициент Е смешения исходного контура. Все эти данные обязательны. Рекомендуется, кроме тою, помещать в той же табличке 9) коэфициент /д высоты зуба 10) зуборезный инструмент (номер инструмента или его чертежа) и тип станка, на котором будет нарезаться колесо. Наконец, должны быть даны также размеры для проверки толщины зуба путем измерения по постоянной хорде или по общей нормали, в зависимости от принятого на заводе способа контро я. [c.258]
Ранее упоминались автоматизированные системы станков Призма и Рота , предназначенные для мелкосерийного производства (см. с. 76). В этих системах ЭВМ (производства народного предприятия Роботрон ) управляет отпуском заготовок со склада, их транспортировкой к месту обработки и закреплением в рабочем положении отбором нужных инструментов и закреплением их, обработкой, проверкой на точность обработки, снятием со станка обработанных полуфабрикатов и их дальнейшей транспортировкой, а также передает контрольную информацию на центральный пост управления и т. д. Это еще один пример комплексной автоматизации производства.
[c.83]
Токарь 5-г о разряда. Обработка деталей средней сложности по 2-му и 3-му классам точности на токарных станках различных моделей. Обтачивание и растачивание цилиндрических, конических и эксцентрических поверхностей. Нарезание наружных и внутренних остроугольных прямоугольных и трапецоидаль-ных однозаходных резьб. Глубокое сверление и чистовая обработка отверстий. Обработка точных фасонных выпуклых Т1 вогнутых поверхностей с применением шаблонов и приспособлений. Установление наивыгоднейшего режима резания, сообразуясь с инструментом и обрабатываемым материалом или по технологической карте. Подсчет и подбор шестёрен для нарезки резьбы и обточки конусов. Правильное применение режущего и мерительного инструмента, проверка правильности показаний мерительного инструмента. Заправка и заточка режущего инструмента средней сложности по шаблонам и угломеру. Выполнение работ по чертежам и эскизам средней сложности. Пользование паспортом станка и таблицами для нарезания резьбы. Определение причин ненормальной работы станка и предупреждение брака. Устранение мелких неисправностей станка и его регулировка, не требующие разборки.
[c.101]
Канал орудия большого калибра имеет обыкновенно четыре различных диаметра,, уменьшающихся по направлению к дулу. Расточка этого ступенчатого отверстия» совершается описанным выше способом. По окончании внутренней расточки ствол обтачивают снаружи, соблюдая особую точность в той части, на к-рую надевается кожух. Когда внутренняя труба ствола готова, то таким же порядком растачивают ш обтачивают кожух. Проверку размеров отверстия и наружного диаметра производяр точнейшими приборами. Окончательную расточку канала производят после соединения внутренней трубы с кожухом. Она по существу тождественна первоначальной расточке, с той лишь разницей, что работу производят еще более точно. Допуск составляет только 0,02 мм. Отверстие д. б. кроме того совершенно гладким, круглым, прямым и точно согласоваться с осью орудия. Ствол орудия закрепляют на специальном расточном станке, опирая дульный конец на особую опору и подпирая ствол еще в двух местах его длины, чтобы равномерно распределить вес и избежать прогибания. Предварительную расточку ведут до половины длины ствола, а затем его поворачивают и производят предварительную расточку заднего конца ствола, наблюдая чтобы обе расточки совпали. Окончательную расточку делают с заднего конца ствола, пропускал инструмент по всей длине ствола. Скорость резания не более 5 м/мин. Для последнего прохода длиной ок. 20 ж д. б. допущен только совершенно незначительный допуск благодаря притуплению инструмента. Этим же объясняется и крайне малая скорость резания.
[c.293]
Оправка контрольная КМ5 300 мм
***Внимание диаметр рабочей части может отличаться на несколько мм
Допуск конусности цилиндрической части на длину выше 150 мм: 12 мкр
Биение: =
Термообработанная
Производство: Россия
Контрольная оправка служит для измерения биения шпинделя. Также с помощью поверочной скалки можно выставить переднюю бабку токарного (и других) станка.
Биение выступающей цилиндрической части оправки следует измерять в соответствии с 5.612.2. Однако т.к. ось оправки может пересекаться с осью вращения в плоскости измерения, то для получения более достоверных данных измерения следует проводить в двух сечениях и , отстоящих друг от друга на определенном расстоянии (см. рисунок 94).
Рис. 94
Например, одно измерение следует провести у посадочного конца отверстия, а второе — на максимально возможном расстоянии от первого. Чтобы исключить влияние неправильной установки оправки в отверстии, особенно в случае конического отверстия, эти измерения следует повторить минимум четыре раза, каждый раз поворачивая оправку на 90° относительно шпинделя. В качестве результата принимается среднее значение по четырем измерениям.
В каждом случае радиальное биение следует измерять в вертикальной и горизонтальной плоскостях (положения и на рисунке 94).
Особые требования к вышеописанным методам:
— расстояния между точками измерения следует выбирать так, чтобы минимизировать воздействие боковой нагрузки на измерительный наконечник;
— следует учитывать, что при использовании контрольных оправок точную форму отверстия определить нельзя;
— измерение обработанной на станке цилиндрической детали показывает результат биения всего шпиндельного узла. Эта проверка не дает возможности оценить ни точность формы цилиндрического или конического отверстия, ни фактического положения отверстия относительно оси вращения;
— описанные выше методы применимы только для шпинделей на подшипниках скольжения, на шариковых или роликовых подшипниках;
— биение шпинделя с автоматическим центрированием во время вращения (например, с помощью гидравлики) следует измерять только при вращении на нормальной частоте вращения. В этом случае следует использовать приборы бесконтактного измерения, например емкостные датчики, электромагнитные или другие соответствующие измерительные приборы.
Галашев. Станки — Стр 24
Инструмент для проверки станков на геометрическую точность
Набор инструментов включает поверочную линейку, щупы, уровень, контрольные оправки, индикатор и угольники (рис.).
Рис. Контрольно-поверочный инструмент Поверочные линейки служат для проверки прямолинейности поверхностей. Длинные
линейки применяют для проверки прямолинейности направляющих станин. Поверочные линейки (рис.1 а) изготовляют из чугуна или стали. Для уменьшения коробления их снабжают ребрами.
Набор щупов (рис.1,в) представляет собой стальные пластины толщиной от 0,03 до 1мм. Щупы служат для определения зазора между обработанной поверхностью детали и плоскостью, наложенной на нее проверочной линейки или угольника. Щупами измеряют также зазоры между сопряженными поверхностями деталей. При работе со щупом необходимо осторожно, без больших усилий, вдвигать его в зазор, так как он может погнуться.
Уровень (рис.1 б) состоит из металлического корпуса 1, в котором расположена запаянная с обоих концов стеклянная трубка 2, наполненная жидкостью с пузырьком воздуха. Когда основание уровня находится в горизонтальной плоскости, пузырек стоит точно по средине трубки между нулевыми штрихами. При наклоне уровня пузырек перемещается в сторону
подъема. Если известна цена деления шкалы уровня, то можно определить угол наклона поверхности.
Контрольные оправки представляют собой точные шлифованные валики диаметром от 25 до 50 мм с точными центровыми отверстиями или коническим хвостовиком (рис.2). Как размеры оправок, так и взаимные расположения базовых поверхностей тщательно выдерживаются.
Индикаторы, применяемые при контроле геометрической точности станков, должны иметь цену деления от 0,002 до 0,01 мм и фиксироваться на массивной или магнитной стойке.
Для вопроса
Основные проверки геометрической точности токарного станка
При проверке токарного станка на точность контролируют направляющие станины, биение шпинделя и зазор ходового винта.
Проверка 1
Направляющие станины должны быть прямолинейными в продольном направлении. Непрямолинейность направляющих станин является дефектом, отражающимся на
прямолинейности получения образующей цилиндрической поверхности при точении по методу следа материальной точки. Основной причиной появления этого дефекта является износ направляющих в процессе эксплуатации станка. При некачественной чистке и нерегулярной смазке направляющие изнашиваются наиболее интенсивно. Причём износ их по длине неравномерный. Обычно наибольший износ на6людается в средней части и вблизи патрона, а
наименьший по концам направляющих. Износ направляющих станка можно обнаружить визуально и измерить с помощью измерительных приборов и инструментов. Чтобы определить величину износа или отклонение от прямолинейности, специальную проверочную линейку устанавливают на направляющую, а затем щупом измеряют зазор между ее поверхностью и линейкой.
Для станков нормальной точности допустимый износ не должен превышать 0,02 мм на длине 1000 мм (для станков с высотой центров до 300мм) и величины 0,03 мм на той же длине (для станков с высотой свыше 300мм).
Проверка 2
Направляющие станины задней бабки должны быть параллельны направляющим ка-
ретки.
При непараллельности направляющих задней бабки и каретки на деталях после точения с использованием центра задней бабки можно обнаружить чрезмерную конусность. причем величина конусности для разных деталей различна. Она зависит от длины обрабатываемой детали и от величины непараллельности направляющих. Эту проверку производят индикатором, закрепленным в резцедержателе каретки, которую перемещают по направляющим станины (рис.3). При этом штифт 1 индикатора упирается в направляющую задней бабки.
Рис. Проверка непараллельности на- | Рис. Проверка горизонтальности на- |
правляющих задней бабки и каретки. | правляющих станины |
Для станков нормальной точности допускаемое отклонение до 0,01мм (при высоте центров до 200мм) и до 0,02мм (при высоте центров более 200мм) на длине 1000мм.
Проверка 3
Направляющие станины должны быть горизонтальны.
Горизонтальность направляющих станин является проверкой правильности установ-
ки станка перед его эксплуатацией. Горизонтальность расположения направляющих координирует станок в пространстве и позволяет обеспечить правильную его загрузку при работе. Проверку производят уровнем 1 пузырькового типа (рис.4), передвигая линейку 2 с уровнем вдоль направляющих станины.
Допускаемое отклонение не более 0,05 мм на длине 1000 мм (для станков нормальной точности). Регулировку положения направляющих осуществляют специальными клиньями при монтаже станка на фундамент.
Проверка 4
Ось шпинделя должна быть параллельна направляющим станины в вертикальной и горизонтальной плоскостях.
Если ось шпинделя не является параллельной направляющим станины, то при обтачивании цилиндрической поверхности может быть получена поверхность однополостного гиперболоида вращения. Это объясняется тем, что траектория движения вершины резца и ось шпинделя скрещиваются. Для проверки отклонения оси шпинделя 1 от параллельности в коническое отверстие шпинделя вставляют контрольную оправку 5 (рис.5).
б)
а)
Рис. Проверка параллельности оси шпинделя направляющим станины в вертикальной
(а) и горизонтальной плоскостях (б).
На каретке 4 закрепляют индикатор 2 на стойке и устанавливают его так, чтобы штифт 3 индикатора касался оправки сначала в вертикальной (рис.5 а), а затем в горизонтальной
(рис.5 б) плоскостях. Перемещая каретку вдоль оправки на длине 300 мм, отмечают отклонения стрелки индикатора.
Для станков нормальной точности допускаемое отклонение от параллельности 0,01мм (в горизонтальной плоскости) и 0,01- 0,02 мм (в вертикальной плоскости).
Проверка 5
Шпиндель не должен иметь радиального биения.
Повышенное радиальное биение шпинделя приводит к появлению аналогичного биения на обрабатываемой детали при смене технологических баз. Кроме того, увеличивается вероятность появления вибраций при точении и ухудшение шероховатости обработки. Проверка радиального биения шпинделя производится индикатором, укрепленным в резцедержателе (рис.6 а). При проверке необходимо, чтобы штифт 1 индикатора упирался в шейку фланца шпинделя 2 при снятом патроне.
Для станков нормальной точности допускаемое отклонение0,01мм (при высоте центров до 350 мм) и 0,02 мм (при высоте центров более 350 мм).
Для вопроса
а)
б)
в)
Рис. Проверка радиального (а) и осевого (б) биения шпинделя, (в) биения переднего центра.
Проверка 6
Передний центр не должен иметь биения.
Биение переднего центра приводит к погрешности по радиальному биению детали, обрабатываемой в центрах. Проверка биения центра осуществляется аналогично проверке 5. Для проверки индикатор укрепляют в резцедержателе (рис.6 в) и его штифт 1 прижимают к концу 2 центра.
Допускаемые отклонения по биению центра аналогичны допустимым значениям по радиальному биению шпинделя (см. проверку 5).
Проверка 7
Шпиндель не должен иметь осевого биения.
Повышенное осевое биение шпинделя приводит к появлению непер пендикулярности торца обработанной детали относительно её оси, а также к повышенным погрешностям линейных размеров. Шероховатость об работки также повышается из-за возникновения вибраций. Проверка осевого биения шпинделя производится аналогично проверке 5,но штифт 1 индикатора (рис.6 в) должен упираться в торец 2 буртика шпинделя.
Допускаемые отклонения также аналогичны проверке 5.
Проверка 8
Шаг ходового винта должен быть одинаковым по длине винта.
Нестабильность шага ходового винта по длине винта приводит к нестабильности шага нарезаемой резьбы на различных участках детали. Это приводит к ухудшению собираемости изделий, имеющих резьбовые соединения. Точность шага ходового винта проверяют посредством специальной эталонной оправки 1, установленной между центрами передней и задней бабок (рис.7), и цилиндрической гайки 2, навертываемой на резьбовую оправку. В гайке имеется продольный паз, в который вводят шарик державки 3, фиксирующей гайку от поворота. В торец гайки упирается штифт индикатора 4, связанного с резцедержателем. Станок настраивают на шаг резьбы оправки при подаче от ходового винта станка. Включают станок и следят за показаниями индикатора.
Для вопроса
Для заметок на полях
Рис. Проверка точности шага ходового винта станка.
Для станков нормальной точности допускаемые отклонения на длине 100 мм 0,03 мм и для станков с высотой центров до 400 мм на длине 300 мм 0,05 мм.
Для вопроса
Контрольная оправка — Большая Энциклопедия Нефти и Газа, статья, страница 1
Контрольная оправка
Cтраница 1
Контрольная оправка — точно шлифованный стержень с цилиндрической измерительной частью и коническим хвостовиком, который служит для закрепления оправки в отверстии шпинделя станка. Оправками пользуются для определения, совпадают ли оси конического отверстия и шпинделя. Оправку плотно вставляют в шпиндель, затем, медленно вращая шпиндель, ведут отсчет биения с помощью индикатора в различных местах оправки.
[1]
Контрольная оправка представляет точный шлифовальный валик диаметром от 25 до 50 мм с точными центровыми отверстиями или коническим хвостовиком ( рис. 28), вставленным в коническое отверстие шпинделя. [3]
Контрольную оправку устанавливают в конусном отверстии стола или при помощи регулировочных устройств. Индикатор закрепляют на неподвижной части станка, мерительный штифт касается образующей оправки. Стол с оправкой приводят во вращение. [4]
Контрольную оправку устанавливают в конусном отверстии стола или при помощи регулировочных устройств. [5]
Диаметры контрольных оправок принимают равными 25 мм, 40 мм и 60 мм при длинах цилиндрической части, соответственно, 150 мм, 300 мм и 500 мм.
[6]
Устанавливают контрольную оправку в шпинделе фрезерной головки, выставляют ее параллельно направлению движения стола расточного станка и закрепляют предварительно. То же выполняют в двух взаимно перпендикулярных плоскостях. Закрепляют фрезерную головку окончательно. [8]
Один конец контрольной оправки представляет собой конус, соответствующий конусу в гнезде шпинделя проверяемого станка, а другой конец сделан цилиндрическим. Контрольные оправки бывают диаметром 25, 40 и 60 мм при длине цилиндрической части соответственно 150, 300 и 500 мм. [9]
При установке контрольной оправки в конусное отверстие необходимо, чтобы форма отверстия шпинделя была предварительно проверена на краску по калибру-пробке. На каждой из четырех продольных линий, наносимых на калибре, допускаются нестертые места длиной до 5 мм при общей их длине не более 30 % длины линии. При отклонениях выше допустимых демонтируют шпиндель и исправляют конусное отверстие шлифованием.
[10]
Один конец контрольных оправок представляет собой конус, соответствующий конусу в гнезде шпинделя проверяемого станка, а другой конец выполнен цилиндрическим. [11]
По образующим двух контрольных оправок, находящихся во втулках делительного устройства, с помощью индикатора на стойке выверяют и устанавливают корпус в горизонтальной плоскости. После выверки корпус крепят струбцинами к массивному угольнику. В этом положении шабрят все площадки, находящиеся в одной плоскости, параллельной контрольной плите. Для шабрения площадок, находящихся под углом 90, корпус поворачивают в призмах на 90 и выверяют по контрольным оправкам, находящимся в отверстиях фиксирующих втулок, с помощью контрольного цилиндра или индикатором на стойке. Чистовое растачивание отверстий под кондукторные втулки и контрольных отверстий для координации устанавливаемых на корпусе деталей ( призм, стоек, пластин и др. ) производят на коор-динатно-расточном станке после сборки корпуса со стойками. Приспособление, установленное на координатно-расточный станок, проверяют по цапфам и обработанным площадкам. Корпус при растачивании отверстий в двух позициях устанавливают поворотом и фиксацией его делительным устройством приспособления. Чистовая обработка площадок Б, Г Х, М, Л, Н, П, И вместо шабрения может быть произведена чистовым фрезерованием на координатно-расточном станке после сборки корпуса со стойками. При этом фрезеровать можно только на специально приспособленных для этой цели координатно-расточных станках. Такие станки оборудованы устройствами для сообщения столу, салазкам и шпиндельной бабке механических подач. Фрезерование производят при малой глубине резания ( менее 0 5 мм) при подаче до 200 мм / мин. На станках с винтовыми отсчетно-измерительными системами, у которых винты выполняют как отсчетно-измерительные функции, так и транспортные, фрезерование недопустимо.
[12]
На шпинделе крепят специальную контрольную оправку с индикатором, измерительный штифт которого касается рабочей поверхности стола. При проверке консоль должна быть застопорена на станине, а салазки — на консоли. Каждое измерение производят в двух положениях индикатора, смещенных относительно шпинделя на 180 в продольной и поперечной плоскостях.
[13]
Шестерня устанавливается на контрольной оправке в центрах делительной головки. Поверка производится индикатором, пуговка которого касается по концам измерительного ролика, вложенного во впадину зубьев. Поверка повторяется не менее чем в 3 местах по окружности. [14]
Шестерня устанавливается на контрольной оправке в центрах делительной головки. Поверка производится индикатором пу-гозка которого касается измерительного ролика, вложенного во впадину зуба. Затем ролик перекладывают в последующие впалины зубьев. Разрешается ролик перекладывать через 2 — 5 зубьев. Диаметры измерительных роликов изготовляются в зависимости от модулей шестерен с расчетом, чтобы, при вкладывании между зубьями, ролик касался делительной окружности.
[15]
Страницы: 1 2 3 4 5
Проверка на точность токарно винторезного станка
При проверке токарного станка на точность в основном проверяют направляющие станины, биение шпинделя и ходовой винт.
Направляющие станины должны быть прямолинейными в продольном направлении. При износе на них появляются канавки, царапины, иногда забоины. Износ можно обнаружить поверхностным осмотром и при помощи измерительных инструментов. Чтобы определить его величину, устанавливают проверочную линейку 1 (рис. 255) поочередно на направляющие 2, затем определяют на просвет и измеряют щупом зазор между их поверхностями и линейкой.
Допустимым считается такой износ станины: при высоте центров до 300 мм — 0,02 мм на длине 1000 мм; при высоте центров больше 300 мм — 0,03 мм на той же длине. У новых или отремонтированных станков на эту величину допускается только выпуклость станины, но не вогнутость.
Направляющие станины для задней бабки должны быть параллельны направляющим для каретки. Проверяют параллельность индикатором, закрепленным в резцедержателе на каретке (рис. 256), которую перемещают по станине; штифт индикатора упирают в направляющую для задней бабки. Допускаемое отклонение — до 0,01 мм для станков с высотой центров до 200 мм и до 0,02 мм — для станков с высотой центров более 200 мм.
Горизонтальность направляющих станины проверяют уровнем, как показано на рис. 257, передвигая линейку 2 с уровнем 1 вдоль направляющих станины. Допускаемое отклонение составляет 0,05 мм на длине 1000 мм.
Ось шпинделя должна быть параллельна направляющим станины в вертикальной и горизонтальной плоскостях. Для проверки в коническое отверстие шпинделя вставляют контрольную оправку и проверяют ее индикатором на отсутствие биения по всей ее длине. Затем закрепляют на каретке индикатор и устанавливают его так, чтобы штифт индикатора касался оправки сначала в вертикальной (рис. 258, а), а потом в горизонтальной (рис. 258, б) плоскости. Перемещая при каждой установке каретку вдоль оправки на длину 300 мм, отмечают отклонения индикатора, которые не должны превышать в вертикальной плоскости 0,01 мм для станков с высотой центров до 200 мм и 0,02 мм — для станков с высотой центров до 400 мм. В горизонтальной плоскости отклонения индикатора не должны быть более 0,01 мм для станков с любой высотой центров.
Отклонение оправки, считая вправо от бабки, допускается в вертикальной плоскости только вверх, а в горизонтальной плоскости — только в сторону резца.
Шейки шпинделя должны вращаться без биения. Шпиндель на биение проверяют индикатором, укрепленным в резцовой головке. При проверке необходимо, чтобы штифт 1 индикатора упирался в шейку 2 шпинделя (рис. 259, а). Допускаемой отклонение 0,01 мм при высоте центров до 350 мм и 0,02 мм при высоте центров более 350 мм.
Шпиндель не должен иметь осевого перемещения пр вращении. Проверку производят, как в предыдущей случае, но штифт 1 индикатора (рис. 259, б) упирают в торец буртика 2 шпинделя. Допускаемые отклонения те же, что и при проверке биения шейки.
Вершина переднего центра при вращении не должна иметь биения. Для проверки индикатор укрепляют в резцовой головке (рис. 259, в) и его штифт 1 упирают в конус 2 центра. Допускаемые отклонения такие же, как в предыдущих двух случаях.
Точность шага ходового винта проверяют точной резьбовой оправкой 1, устанавливаемой между центрами передней и задней бабок (рис. 260), и точной цилиндрической гайкой 2, навертываемой на резьбовую оправку. В гайке 2 имеется продольный паз, в который вводят шарик державки 3, несущей индикатор 4 и закрепленной в суппорте станка. Наконечник индикатора упирается в торец гайки, удерживаемой от вращения шариком державки. Станок настраивают на шаг резьбы оправки. Пустив станок с включенной разъемной гайкой, следят за показаниями индикатора. Допускаемые отклонения: 0,03 мм на длине 100 мм и 0,05 мм на длине 300 мм для станков с высотой центров до 400 мм.
Практическая проверка точности токарного станка. Помимо рассмотренных геометрических проверок, производят комплексную практическую проверку точности токарного станка. Целью проверки является оценка точности станка в работе при изготовлении деталей с цилиндрической и торцовой поверхностями. Во время этой проверки определяются получающиеся отклонения по овальности, конусности и плоскостности, которые не должны превышать отклонения, устанавливаемых ГОСТом: по овальности 0,01-0,02 мм и по конусности 0,02 мм на длине 1000 мм и вогнутости торца не больше 0,02 мм на диаметре 300 мм.
Говоря о точности токарного станка имеется ввиду соответствие данных паспорта оборудования следующим параметрам:
- перемещение тех элементов, на которых располагается заготовка;
- расположение тех поверхностей, с помощью которых базируется инструмент или заготовка;
- форма базовых поверхностей.
После окончательной сборки и проверки на заводе, а также после ремонтов станки получают акт о приемке, и только после этого, вводятся в эксплуатацию.
Требования к точности указываются в паспорте станков.
Выполнение измерения для выявления погрешностей следует производить регулярно в соответствии с нормативами ГОСТ.
Скачать ГОСТ 8-82 «Станки металлорежущие. Общие требования к испытаниям на точность»
Скачать ГОСТ 18097-93 «Станки токарно-винторезные и токарные. Основные размеры. Нормы точности».
В процессе использования токарного оборудования происходит износ его деталей, т.к. при обработке изделий появляются силы, которые производят различные деформации. При работе станок нагревается и под воздействием температуры образуются тепловые деформации. Все эти дефекты оказывают отрицательное влияние на качество обрабатываемых деталей. И для того чтобы восстановить паспортные показатели станка периодически следует ремонтировать изношенные детали.
Качественное испытание токарных станков в соответствии с государственным стандартом во многом зависит от того, насколько правильно он установлен на испытательном стенде. Установка на стенд должна происходить строго, соблюдая установочный чертеж. Самым распространенным методом, является установка на количество опор более 3-х. Отметим, что все двигающиеся части проверяемого станка должны находится в средних положениях.
Геометрическая точность токарного станка характеризует качество изготовления деталей, поэтому установка заготовки должна осуществляться на геометрическую правильную поверхность.
Для определения степени износа нужно установить линейку поочередно на каждую из направляющих станины. После этого, щупом определяется расстояние между направляющими и контрольной линейкой. Допустимое значение такого износа согласно государственного стандарта не должно превышать 0,02 мм.
Не мало важным фактором является соответствие горизонтальности направляющих станины. Определить ее можно с помощью перемещения специального уровня вдоль поверхности направляющих, который покажет значение имеющегося отклонения. Предельно допустимое отклонение по ГОСТ не может превышать значение 0,05 мм. А параллельность между направляющими станины для упорной (задней бабки) и каретки можно проверить с помощью специального измерительного индикатора. Его необходимо закрепить на каретке с суппортом и с помощью перемещения каретки выявить величину отклонения.
Также точность токарного станка поможет определить биение вращающегося шпинделя, в который крепится заготовка. Обязательно при этом соблюдать параллельность между осью шпинделя и направляющими станины. Во время проверки в отверстие вала устанавливают специальную контрольную оправку и на протяжении всей ее длины проверяют ее на биение.
Осуществляя технологическую проверку на точность стоит обратить внимание также и на вращение шеек вращающегося вала. Биение при их вращении — не допустимо. В резцовой головке необходимо закрепить индикатор, затем уперев его штифт в шейке шпинделя произвести измерения. По ГОСТ значение не должно превышать 0,01 мм. Не допустимым будет при вращении шпинделя, чтобы он отклонялся от оси.
Проверка биения шпинделя: а — проверка биения шейки шпинделя; б — проверка осевого перемещения шпинделя; в — проверка биения переднего центра
Также одним из важных измерений при проверке токарного станка на точность является определение точности шага ходового винта. Величина отклонения в соответствии с ГОСТ определяется с помощью следующей методики:
- в центры передней и задней бабки устанавливают резьбовую оправку;
- на эту оправку накручивают гайку в форме цилиндра и имеющую паз;
- в паз этой цилиндрической гайки устанавливается шарик державки;
- индикатор, закрепленный в державке, упирается в торцевую часть цилиндрической гайки;
- токарный станок настраивается на шаг резьбы;
- индикатор определяет отклонения.
Проверка точности шага ходового винта
Основные погрешности формы обрабатываемых заготовок:
- непрямолинейность;
- конуснообразность;
- отсутствие параллельности;
- некруглость;
- неконцентричность.
Инструмент, применяемые при испытаниях:
- контрольная линейка;
- уровень;
- щуп;
- угольник;
- измерительный индикатор;
- резьбовая оправка;
- контрольная оправка;
- цилиндрическая гайка;
- державка.
При выполнении измерений следует использовать только те инструменты, которые прошли метрологическую поверку с учтенной погрешностью.
Если вы нашли ошибку, пожалуйста, выделите фрагмент текста и нажмите Ctrl+Enter.
Лабораторная работа №1
ПРОВЕРКА ГЕОМЕТРИЧЕСКОЙ ТОЧНОСТИ ТОКАРНО-ВИНТОРЕЗНОГО СТАНКА 16К20
Задание
1. Ознакомиться с наиболее распространенными средствами и приемами проверки геометрической точности станка 16К20.
2. Составить отчет о проделанной работе.
Цель и задачи лабораторной работы
1.1. Ознакомиться с контрольно-измерительными устройствами и приемами работы при проверке геометрической точности станка и взаимного расположения механизмов на станке.
1.2. Ознакомиться с существующими нормами точности станков.
1.3. Научиться самостоятельно составлять схему проверки и производить необходимые измерения геометрических погрешностей токарно-винторезного станка.
1.4. Научиться анализировать результаты производственных проверок путем сравнения их с установленными в станкостроении нормами точности.
1.5. Составить отчет о проделанной работе.
Общие методические указания
В процессе создания станка новой конструкции и после изготовления серийного станка, а также после ремонта, перед пуском станка в эксплуатацию, проводятся разные по целям и объему экспериментальные исследования, испытания и проверки станка и его отдельных частей.
Геометрическая точность станка зависит от точности деталей, узлов и качества их сборки. Она должна контролироваться для каждого станка.
Влияние геометрической погрешности станка оценивается по взаимному расположению инструмента и обрабатываемой детали в статическом состоянии без воздействия на станок силы резания. Допустимые нормы точности станков и методы их проверки определяются ГОСТ 18097-88 в зависимости от их типов.
Оборудование, приспособления, инструмент
3.1. Проверка геометрической точности определяется на токарно-винторезном станке
3.2. Индикатор (с ценой деления 0,001 мм) на стойке с магнитным основанием.
3.3. Проверочная линейка с ценой деления, 1 мм
3.4. Проверочный уровень.
3.6. Контрольные оправки:
— цилиндрическая с конусом Морзе 5;
— торцовая с конусом Морзе 5;
— цилиндрическая с конусом Морзе 4;
— цилиндрическая с центровыми отверстиями;
3.7. Универсальный мостик.
3. 8. Набор плоскопараллельных мер.
Порядок выполнения работы
Перед выполнением измерений геометрических погрешностей токарного станка необходимо изучить паспортные данные станка, измерительные приборы и оправки, а также последовательность выполнения замеров. Измерения проводить в следующей последовательности:
4.1. Отклонение от прямолинейности направляющих суппорта станка (станины) в вертикальной плоскости (рис. 1.1).
4.1.1. Установить мостик на передней направляющей суппорта станка.
4.1.2. Параллельно к направляющей установить на мостике уровень.
4.1.3. Перемещая мостик по всей длине направляющей, снять показания уровня через каждые L= 300 мм.
4.1.4. Установить мостик с уровнем на задней направляющей и повторить замеры.
Отклонение определяют как наибольшую алгебраическую разность показаний шкалы уровня. Допустимые отклонения передней и задней направляющих 0..0,02 мм на длине 1000 мм. Вогнутость не допускается.
4. 2. Отклонение от прямолинейности продольного перемещения суппорта в вертикальной плоскости (рис. 1.2).
4.2.1. Установить уровень на суппорте около резцедержателя, параллельно направлению перемещения суппорта. Резцедержатель должен быть расположен как можно ближе к оси центров станка.
4.2.2. Перемещая суппорт в продольном направлении на всю длину хода, произвести измерение не более чем через 200 мм. Допустимое отклонение 0,025 мм на длине 800 мм. Вогнутость не допускается.
4.3. Отклонение от параллельности направляющих суппорта станка (станины) на отсутствие короблений (рис. 1.3).
4.3.1. Установить мостик на станине на направляющих суппорта станка.
4.3.2. Установить на мостике уровень перпендикулярно к продольным направляющим.
4.3.3. Перемещая мостик по всей длине станины, снять показания уровня через каждые 300 мм. Допускаемое отклонение 0,02 мм на длине 1000 мм.
4.4. Отклонение от прямолинейности продольного перемещения суппорта станка в горизонтальной плоскости (рис. 1.4).
4.4.1. Контрольную оправку, длиной отвечающей расстоянию между центрами, с цилиндрической измерительной поверхностью установить в центрах передней 4 и задней 5 бабок. Резцедержатель должен быть расположен как можно ближе к оси центров станка.
4.4.2. Установить и закрепить индикатор на суппорте 1 станка в резцедержателе, коснувшись измерительным наконечником боковой образующей контрольной оправки перпендикулярно к ее оси. Перемещая суппорт 1 станка в продольном направлении по длине оправки, сиять показания индикатора в точках А и Б.
Отклонение определяют как наибольшую алгебраическую разность показаний индикатора. Допускаемое отклонение 0,015 мм на длине 1000 мм.
4.5. Отклонение, от параллельности линии центров по отношению к направляющим станины в вертикальной плоскости (рис. 1.5).
4.5.1. Установить в центрах передней 1 и задней 5 бабок контрольную оправку 2 с цилиндрической поверхностью.
4.5.2. Закрепить индикатор 3 на суппорте 4 станка и, коснувшись его измерительным наконечником верхней образующей контрольной оправки в вертикальной плоскости перпендикулярно к ее оси в точке А, переместить суппорт на длину 700 мм и произвести измерение в точке Б.
4.5.3. Повернуть шпиндель на 180° и повторить измерения в точках А и Б. Отклонение определяют как среднюю арифметическую величину двух указанных измерений, каждая из которых определяется алгебраической разностью показаний индикатора на концах контрольной оправки. Допустимое отклонение О..0,03 мм.
4.6. Отклонение от параллельности перемещения задней бабки; по отношению к перемещению суппорта станка (рис. 1.6): а в вертикальной плоскости; б-в горизонтальной плоскости.
4.6.1. Установить суппорт 1 и заднюю бабку 4 в крайнее положение на направляющих станины (правое или левое). Пиноль 3 вдвинуть в заднюю бабку на 0,8 хода и закрепить.
4.6.2. Установить и закрепить индикатор 2 на суппорте станка, коснувшись измерительным наконечником образующую пиноли задней бабки перпендикулярно к ее оси.
4.6.3. Перемещая суппорт и заднюю бабку станка одновременно (при этом расстояние между суппортом и задней бабкой должно быть постоянным) на всю длину ее хода, снять показания индикатора не более чем через 0,3 длины хода с остановками для измерения и закрепления задней бабки.
Отклонение определяют как наибольшую алгебраическую разность показаний индикатора при первоначальном и последующем положениях задней бабки и суппорта.
Допустимое отклонение в вертикальной плоскости 0,04 мм, в горизонтальной плоскости 0,025 мм.
4.7. Отклонение параллельности направляющих задней бабки по отношению к перемещению суппорта станка (рис. 1.7).
4.7.1. Установить и закрепить индикатор на суппорте станка, коснувшись измерительным наконечником перпендикулярно поверхности направляющей задней бабки.
4.7.2. Перемещая суппорт станка по всей длине направляющих, снять показания индикатора.
4.7.3. Произвести замеры всех поверхностей направляющих задней бабки поочередно. Допустимое, отклонение по всей длине точения 0,015 мм.
4.8. Радиальное биение центрирующей поверхности шпинделя передней бабки (рис. 8).
4.8.1. Установить и закрепить индикатор 1 на неподвижной части станка, коснувшись измерительным наконечником перпендикулярно образующей конической поверхности шпинделя 2.
4.8.2. Вращая шпиндель станка в рабочем направлении, снять показания индикатора. При измерении шпиндель должен сделать не менее двух оборотов. Отклонение определяют как наибольшую алгебраическую разность показаний индикатора. Допустимое отклонение 0,008 мм.
4.9. Осевое биение шпинделя передней бабки (рис. 1.9).
4.9.1. Установить контрольную оправку 2 в конусное отверстие 1 передней бабки станка.
4.9.2. Установись и закрепить на неподвижной части станка индикатор 3, коснувшись измерительным наконечником центра поверхности оправки 2 вдоль оси шпинделя станка.
4.9.3. Вращая шпиндель в рабочем направлении, произвести измерения по показаниям индикатора. При измерении шпиндель должен сделать не менее двух оборотов. Отклонение определяют как наибольшую алгебраическую разность результатов измерений. Допустимое отклонение 0,008 мм.
4.10. Осевое биение торцевой поверхности опорного буртика фланца шпинделя передней бабки (рис. 1.10).
4. 10.1. Установить и закрепить на неподвижной части станка индикатор 1, коснувшись измерительным наконечником перпендикулярно торцевой поверхности опорного буртика шпинделя 2 на возможно большем расстоянии от его центра.
4.10.2. Вращая шпиндель в рабочем направлении, снять показания индикатора в двух взаимно перпендикулярных плоскостях диаметрально противоположных точках поочередно (в 4-х точках на поверхности фланца через каждые 90°). При каждом измерении шпиндель должен сделать не менее двух оборотов. Отклонение определяют как наибольшую алгебраическую разность показаний индикатора в каждом его положении. Допустимое отклонение — 0,015 мм.
4.11. Радиальное биение конического отверстия шпинделя передней бабки (рис. 1.11): а) -у торца; б) — на длине L=300 мм.
4.11.1. В коническое отверстие шпинделя (Морзе 5) установить контрольную оправку 3 с цилиндрической измерительной поверхностью.
4.11.2. На неподвижной части станка установить и закрепить индикатор 2, касаясь измерительным наконечником поверхности контрольной оправки в точке А в направлении ее оси, перпендикулярно образующей.
4.11.3. Вращая шпиндель в рабочем направлении, произвести замеры по показаниям индикатора. При измерении шпиндель должен сделать не менее двух оборотов.
4.11.4. Повторить измерения в точке Б. Замеры произвести 4-х кратно, меняя каждый раз положение оправки в конусном отверстии шпинделя через каждые 90° в 2-х взаимно перпендикулярных плоскостях. Отклонение определяют как наибольшую алгебраическую разность показаний индикатора в каждом его положении. Допустимые отклонения: у торца — 0,008 мм, на длине L = 300 мм — 0,025 мм.
4.12. Отклонение от параллельности оси вращения шпинделя передней бабки по отношению к продольному перемещению суппорта станка в плоскостях: а — вертикальной, б — горизонтальной (рис. 1.12).
4.12.1. Установить контрольную оправку 3 с цилиндрической измерительной поверхностью в конусное отверстие шпинделя 1.
4.12.2. Установить на суппорте 4 и закрепить в резцедержателе индикатор 2, касаясь измерительным наконечником в вертикальной плоскости перпендикулярно к образующей поверхности оправки в направлении к ее оси.
4.12.3. Перемещая суппорт в продольном направлении вдоль станины станка на всю длину хода L , снять показания индикатора.
4.12.4. Повернуть шпиндель на 180° и повторить замер.
4.12.5. Повторить измерение в горизонтальной плоскости.
Отклонение определяют как среднеарифметическую величину нескольких измерений в каждой плоскости, каждый из которых определяют как наибольшую алгебраическую разность показаний индикатора при перемещении суппорта.
Допустимое отклонение на расстоянии L = 300 мм:
а) в вертикальной плоскости 0..0,02 мм;
б) в горизонтальной плоскости 0..0,01, мм.
Свободный конец оправки может отклоняться вверх и в направлении к резцу.
4.13. Отклонение от параллельности продольного перемещения верхних салазок суппорта по отношению к оси вращения шпинделя передней бабки в вертикальной плоскости (рис. 1.13).
4.13.1. Установить контрольную оправку 3 с цилиндрической измерительной поверхностью в конусное отверстие шпинделя 1.
4.13.2. Установить в верхних салазках суппорта 4 и закрепить в резцедержателе индикаторный прибор 2, коснувшись измерительным наконечником перпендикулярно образующей измерительной поверхности оправки в направлении к ее оси в вертикальной плоскости.
4.13.3. Салазки верхнего суппорта установить таким образом, чтобы они в горизонтальной плоскости были отдалены на одинаковом расстоянии от концов оправки.
4.13.4. Перемещая верхние салазки суппорта вдоль оси шпинделя, произвести измерения не менее чем в трех поперечных сечениях оправки крайних и средних.
Для определения наибольшего показания индикатора в каждом из положений суппорта верхнюю часть его перемещают в поперечном направлении вперед и назад.
4.13.5. Повернуть шпиндель на 180° и повторить замер.
Отклонение определяют как среднее арифметическое двух указанных измерений, каждое из которых определяется как наибольшая алгебраическая разность показаний индикатора в указаниях положениях салазок суппорта. Допустимое отклонение от 0 до 0,020 мм на длине L=100 мм. Свободный конец оправки может отклоняться только вверх.
4.14. Отклонение от параллельности перемещений пиноли задней бабки по отношению к продольному перемещению суппорта в вертикальной и в горизонтальной плоскостях (рис. 1.14).
4.14.1. Установить заднюю бабку в положение, предусмотренное для проверки (см. п. 4.6) с учетом обеспечения хода каретки на длину L.
4.14.2. Вдвинуть пиноль 3 в заднюю бабку 4 и зажать.
1.14.1. Установить и закрепить индикатор 2 на верхнем суппорте станка, коснувшись измерительным наконечником в вертикальной плоскости перпендикулярно образующей поверхности в точке А в направлении к ее оси и снять показания.
4.14.1. Отжать пиноль и, выдвинув на длину больше L, снова зажать.
4.14.2. Переместить суппорт станка с индикатором в продольном направлении в сторону передней бабки к той же точке касания А на образующей пиноли задней бабки измерительным наконечником индикатора.
4.14.3. Повторить замеры в горизонтальной плоскости. Отклонение в каждой из плоскостей определяют как наибольшую алгебраическую разность показаний индикатора в двух указанных положениях пиноли и суппорта.
Допустимое отклонение на всей длине выдвижения:
а) в вертикальной плоскости — 0..0,02 мм;
б) в горизонтальной плоскости — 0..0,01 мм.
Свободный конец пиноли может отклоняться вверх и в сторону инструмента.
4.15. Отклонение от параллельности оси конусного отверстия пиноли задней бабки по отношению к перемещению суппорта станка в плоскостях: (рис. 1.15)
а) в вертикальной плоскости;
б) в горизонтальной плоскости.
4.15.1. Установить контрольную оправку 1 с цилиндрической измерительной поверхностью в конусное отверстие вдвинутой и зажатой пиноли 3 задней бабки.
4.15.2. Установить на суппорте 4 индикатор 2 так, чтобы его измерительный наконечник касался измерительной поверхности оправки в вертикальной плоскости перпендикулярно образующей в направлении к ее оси.
4.15.3. Переместить суппорт станка по станине в продольном направлении на длину L и снять показания индикатора. Отклонение определяют как наибольшую алгебраическую разность показаний индикатора в указанных положениях суппорта. Допустимые отклонения на длине L = 200 мм:
а) в вертикальной плоскости — 0..0,020 мм;
б) в горизонтальной плоскости — 0..0,020 мм.
Свободный конец оправки может отклоняться вверх и в сторону инструмента.
4.16. Отклонение от перпендикулярности перемещения поперечного суппорта по отношению к оси шпинделя станка (рис. 1.16).
4.16.1. Установить в конусное отверстие шпинделя станка специальный контрольный диск (линейку).
4.16.2. Установить и закрепить на поперечном суппорте станка индикатор так, чтобы измерительный наконечник касался перпендикулярно торцевой поверхности контрольного диска (линейки).
4.16.3. Перемещая поперечный суппорт на длину L, снять показания индикатора.
4.16.4. Повернуть шпиндель станка на 180° и повторить замер. Отклонение определяют как среднее арифметическое результатов двух замеров. Допустимое отклонение на длине L = 150 мм — 0..0,20 мм.
Допускается единственное отклонение, при котором обработанная торцевая поверхность будет только вогнутой.
4.17. Осевое биение ходового винта продольной подачи (рис. 1.17).
4.17.1. Установить шарик в центровое отверстие ходового винта.
4.17.2. Установить и закрепить на станине станка индикатор так, чтобы измерительный наконечник индикатора касался шарика через плоскопараллельные плитки по оси ходового винта. Вращая ходовой винт в правую сторону, снять показания индикатора. При этом обеспечить осевую нагрузку, которая может быть создана суппортом станка, перемещающегося после сопряжения ходового винта с ходовой маточной гайкой.
4.17.3. Повторить замер при вращении ходового винта в левую сторону. Допустимое отклонение 0,010 мм.
4.18. Осевое биение ходового винта поперечной подачи (То же, что и в п. 4.17).
Контрольные вопросы
5. 1. Точность станков и способы ее оценки.
5.2. От чего зависят и что характеризуют геометрические погрешности в металлорежущих станках?
5.3. Какими документами регламентируются нормы точности станков?
5.4. На что влияет геометрическая точность станка?
5.5. Перечислите методы повышения точности станков?
Не нашли то, что искали? Воспользуйтесь поиском:
Лучшие изречения: Сдача сессии и защита диплома — страшная бессонница, которая потом кажется страшным сном. 8623 — | 7077 — или читать все.
91.146.8.87 © studopedia.ru Не является автором материалов, которые размещены. Но предоставляет возможность бесплатного использования. Есть нарушение авторского права? Напишите нам | Обратная связь.
Отключите adBlock!
и обновите страницу (F5)
очень нужно
Регулярная проверка станков с помощью системы ballbar обеспечивает следующие преимущества:
Калибровочные инструменты Страница 353
Поверочные измерительные приборы Калибровочное устройство «Height Master» Страница 344 Калибровочное устройство «Check Master» Страница 348 Калибровочные инструменты Страница 353 343 Цифровое калибровочное
ПодробнееExitech Ltd) Danaher Precision Systems)
Лазерная система ML10 Gold Standard Высшее достижение среди лазерных измерительных средств, имеющих связь с первичными стандартами Высокая точность ± 0,7 млн -1 точность измерения длины с компенсацией
ПодробнееМУЛЬТИБРЕНДОВЫЙ БУТИК
ООО «Задел» www. zadelrf.ru +7(342)270-00-18 МУЛЬТИБРЕНДОВЫЙ БУТИК ДЕТАЛИ УЗЛЫ КОМПЛЕКТУЮЩИЕ ООО «ЗАДЕЛ» www.zadelrf.ru 618068, г. Пермь, ул. Данщина, 5 оф.204 Отдел продаж: +7 (342) 270-00-18, доб. 1603,
Оптические измерительные приборы
Оптические измерительные приборы P-1 TESA-SCOPE II 300V и 300V Plus Очень удобен для контроля деталей с плоскими поверхностями или других компонентов, используемых в высокоточной механике. Базовый прибор
ПодробнееНовый взгляд. на контроль тел вращения
34 Новый взгляд на контроль тел вращения Текст: Степан Жиделев Металлообрабатывающие предприятия сталкиваются с рядом задач, требующих современных и эффективных технологических решений. Одной из таких
ПодробнееКонтроль плоскостей. Добавил(а) Administrator :29 —
Измерительный инструмент, применяемый при контроле плоскостей, выбирается с учетом необходимой точности измерения, измеряемого размера, шероховатости измеряемой поверхности, типа производства (единичное,
ПодробнееПроизводственная программа: Серия VDM
Производственная программа: Серия VDM Эта серия базируется на традиционной концепции вертикального токарного станка с вертикальным шпинделем. На станках серии VDM могут обрабатываться детали диаметром
08 / содержание раздела
166 www.osnastik.ru 08 / содержание раздела Техническая информация 168 8.1. Резцедержатели для токарных станков по DIN 69880 VDI (ГОСТ 24900-81) 169 8.2. Вытягиватели прутка 178 8.3. Сверлильные и плавающие
Подробнее08 / содержание раздела
170 www.osnastik.ru 08 / содержание раздела Техническая информация 172 8.1. Резцедержатели для токарных станков по DIN 69880 VDI (ГОСТ 24900-81) 173 8.2. Вытягиватели прутка 182 8.3. Сверлильные и плавающие
ПодробнееСистемы зубоизмерительные серий GMS, GMSP, GMSL
Приложение к свидетельству 69833 Лист 1 об утверждении типа средств измерений ОПИСАНИЕ ТИПА СРЕДСТВА ИЗМЕРЕНИЙ Системы зубоизмерительные серий GMS, GMSP, GMSL Назначение средства измерений Системы зубоизмерительные
Подробнее1 ЗАО «ЧелябНИИконтроль», 2 ООО НПП «ЧИЗ»
НОВЫЕ МЕТОДИКИ И СРЕДСТВА ИЗМЕРЕНИЯ ГЕОМЕТРИЧЕСКИХ ПАРАМЕТРОВ РЕЗЬБОВЫХ И УПЛОТНИТЕЛЬНЫХ ПОВЕРХНОСТЕЙ ТРУБ И МУФТ НЕФТЕГАЗОВОГО СОРТАМЕНТА Сурков И.В. 1, Сурков В.И. 2, Котов В.А. 1 1 ЗАО «ЧелябНИИконтроль»,
ПодробнееКоординатно-измерительные машины IMPACT
Координатно-измерительные машины IMPACT Технология контактных измерений IMPACT Matrix Технология сканирования IMPACT Maxxum Компактность Скорость, Точность и Надежность СДЕЛАНО В ВЕЛИКОБРИТАНИИ Разработка
ПодробнееDMU 75 / 95 monoblock
www.dmgmori.com 5-осевые универсальные фрезерные станки DMU 75 / 95 monoblock Высокие технологии в стандартной комплектации Одновременная 5-осевая обработка по лучшей цене DMU 75 / 95 monoblock Высококачественное
ПодробнееROUNDTEST СЕРИИ RA-2200 PRE1361
Приборы для измерения формы ROUNDTEST СЕРИИ RA-2200 PRE1361 Система измерения круглости/цилиндричности, обеспечивающая высочайший уровень точности в своем классе, исключительную простоту эксплуатации и
ПодробнееЦИФРОВОЙ ИЗМЕРИТЕЛЬНЫЙ ПРИБОР
ЦИФРОВОЙ ИЗМЕРИТЕЛЬНЫЙ ПРИБОР вертикальный, с электроприводом, для измерения высоты ОСНОВНЫЕ ХАРАКТЕРИСТИКИ Многофункциональная система измерения с помощью процессора данных и цветного цифрового сенсорного
ПодробнееСледующая ступень точности
ГРС повышенной точности KG Следующая ступень точности Серия P Серия K Серия T Серия MILLFORCE 02 / Точность 03 / Сферы применения 04 / Техника станка 06 / Опции 07 / Технические данные Точность в совершенстве
ПодробнееСкоростная система сканирования SPRINT
Скоростная система сканирования SPRINT Качественно новый уровень скорости сканирования Исключительно высокая точность, обеспечивающая полное трехмерное измерение детали Уникальные возможности и области
ПодробнееВертикальные обрабатывающие центры с ЧПУ
Вертикальные обрабатывающие центры с ЧПУ Вертикальные обрабатывающие центры с ЧПУ (с линейными направляющими) Вертикальные обрабатывающие центры с ЧПУ Вертикальные обрабатывающие центры для обработки на
ПодробнееДинамичная обработка деталей
MILLFORCE 1 / MILLFORCE 2 / MILLFORCE 3 Динамичная обработка деталей P-СЕРИЯ K-СЕРИЯ T-СЕРИЯ MILLFORCE 02 / Применение 03 / Концепция станка 04 / Техника 05 / Опции и варианты оснащения 06 / Рабочая зона
ПодробнееФРЕЗЕРНАЯ ОСНАСТКА. tel.+48 (85) , fax +48 (85)
ФРЕЗЕРНАЯ ОСНАСТКА 207 ФРЕЗЕРНАЯ ОСНАСТКА От поворотных и фрезерных столов, и до делительных устройств и шпиндельного инструмента, все наши продукты проходят тщательный осмотр и должны соответствовать
ПодробнееТочная Тяжелая металлообработка
PR 150 / PR 160 / PR 200 / PR 260 Точная Тяжелая металлообработка P-СЕРИЯ K-СЕРИЯ T-СЕРИЯ MILLFORCE 02 / Применение 03 / Концепция станка 04 / Техника станка 05 / Опции и варианты оснастки 06 / Рабочие
ПодробнееSE 820 SE Токарно-винторезные станки с ЧПУ
Токарно-винторезные станки с ЧПУ SE 820 SE 1020 Универсальные центровые токарные станки предназначены для обработки массивных сивных вращательных деталей. Дают возможность обтачивать внешние и внутренние
ПодробнееСистемы зубоизмерительные серий GMS и GMM
Приложение к свидетельству 45064 Лист 1 об утверждении типа средств измерений ОПИСАНИЕ ТИПА СРЕДСТВА ИЗМЕРЕНИЙ Системы зубоизмерительные серий GMS и GMM Назначение средства измерений Системы зубоизмерительные
ПодробнееОбразовательные материалы Mitutoyo
Образовательные материалы Mitutoyo Образовательные материалы Mitutoyo Наименование Формат Объем Наличие 1 Набор настенных постеров 1 А1 3 постера В наличии 2 Набор настенных постеров 2 А1 3 постера В наличии
ПодробнееТиски лекальные ТИП 3320
Тиски лекальные ТИП 3320 Тиски лекальные изготовлены из высококачественной легированной стали. Твердость рабочих поверхностей достигает HRC58-62. Тиски лекальные стали. Твердость рабочих поверхностей достигает
ПодробнееСТАНКИ МЕТАЛЛОРЕЖУЩИЕ
ГОСУДАРСТВЕННЫЙ СТАНДАРТ СОЮЗА ССР СТАНКИ МЕТАЛЛОРЕЖУЩИЕ СХЕМЫ И СПОСОБЫ ИЗМЕРЕНИЙ ГЕОМЕТРИЧЕСКИХ ПАРАМЕТРОВ ГОСТ 22267 76 (СТ СЭВ 3719-82 СТ СЭВ 3722-82, СТ СЭВ 4141-83 СТ СЭВ 4145-83, СТ СЭВ 4148 83,
ПодробнееКомпания DMG MORI намерена
На выставке EMO компания DMG MORI впервые представит 7 новейших моделей станков 2015 DMG MORI Компания DMG MORI намерена подтвердить свой статус мирового лидера в области обработки металлов, представив
ПодробнееКонусные и параллельные испытательные стержни / оправки
Описание
ИСПЫТАТЕЛЬНЫЕ МАНДРЕЛИ / ИСПЫТАТЕЛЬНЫЕ ПАНЕЛИ
КОНУСНЫЕ ИСПЫТАТЕЛЬНЫЕ МАНДРЕЛИ
ПАРАЛЛЕЛЬНЫЕ ИСПЫТАТЕЛЬНЫЕ МАНДРЕЛИ
• Изготовлены с высокой точностью из легированной стали и подвергнуты термообработке с твердостью 62HRC + 2 HRC.
• Каждая деталь проверяется на концентричность в пределах 0,0001 дюйма и параллельность.
• Используется для проверки соосности между центрами, а также в шпинделях с конусом Морзе.
• Необходимый инструмент в мастерской для тестирования токарных станков.
• Устанавливается между передней и задней бабками.
Контрольные оправки используются для проверки центровки оси шпинделя станка.
Оправка с коническим хвостовиком служит для материального представления оси вращения, так что ось может быть проверена на соосность.
Оправка, установленная между центрами, обеспечивает опорную прямую линию, соединяющую две точки (центры), для проверки совмещения центров.
Испытательные оправки на конус
Код изделия No. Испытательные оправки на конус | Хвостовик | Размер, дюйм | Размер, мм |
---|---|---|---|
ABM-IMT-4000 | MT1 | 6 « | 150 |
ABM-IMT-4001 | MT2 | 11-1 / 8 « | 283 |
ABM-IMT-4002 | MT3 | 13-3 / 16 « | 335 |
ABM-IMT-4003 | MT4 | 15-1 / 4 « | 386 |
ABM-IMT-4004 | MT5 | 17-1 / 2 « | 442 |
ABM-IMT-4005 | MT6 | 19-7 / 8 « | 505 |
ABM-IMT-4006 | ISO 40 | 12 « | 300 |
ABM-IMT-4007 | ISO 50 | 12 « | 300 |
Другие размеры и большие размеры по запросу |
Параллельные испытательные оправки
Код изделия No. Параллельные испытательные оправки | Хвостовик, мм | Размер, мм |
---|---|---|
ABM-IMT-8510 | 40 мм | 300 мм |
ABM-IMT-8511 | 40 мм | 500 мм |
ABM-IMT-8512 | 40 мм | 600 мм |
ABM-IMT-8513 | 50 мм | 300 мм |
ABM-IMT-8514 | 50 мм | 500 мм |
ABM-IMT-8515 | 50 мм | 600 мм |
ABM-IMT-8516 | 60 мм | 300 мм |
ABM-IMT-8517 | 60 мм | 500 мм |
ABM-IMT-8518 | 60 мм | 600 мм |
ABM-IMT-8519 | 80 мм | 750 мм |
ABM-IMT-8520 | 80 мм | 900 мм |
ABM-IMT-8521 | 80 мм | 1000 мм |
ABM-IMT-8522 | 100 мм | 1200 |
Другие размеры и большие размеры по запросу |
ИСПЫТАТЕЛЬНЫЕ ПАНЕЛИ / ИСПЫТАТЕЛЬНЫЕ ПАНЕЛИ
ИСПЫТАТЕЛЬНЫЕ ПАНЕЛИ / ИСПЫТАТЕЛЬНЫЕ ПАНЕЛИ — Garvin Tools Поиск по категорииТОКАРНЫЕ ИНСТРУМЕНТЫ И ПРИНАДЛЕЖНОСТИ
18
ПОВОРОТНЫЕ СТОЛЫ И АКСЕССУАРЫ
4
НАБОРЫ И ИНСТРУМЕНТЫ ДЛЯ РЕМОНТА РЕЗЬБЫ
5
ПРЕЦИЗИОННЫЕ ИЗМЕРИТЕЛЬНЫЕ ИНСТРУМЕНТЫ
11
РАБОЧИЕ ГОЛОВКИ И ПРИНАДЛЕЖНОСТИ
6
ФОРМОВКА И РЕЗКА МЕТАЛЛА
2
МАГНИТНЫЕ И ПЕРЕДВИЖНЫЕ ИНСТРУМЕНТЫ
2
ЧАСОВЫЕ ИНСТРУМЕНТЫ И ОБОРУДОВАНИЕ
6
ЮВЕЛИРНЫЕ ИНСТРУМЕНТЫ И ОБОРУДОВАНИЕ
10
СМАЗОЧНЫЕ ИНСТРУМЕНТЫ И ОБОРУДОВАНИЕ
5
Искать по
ТОКАРНЫЕ ИНСТРУМЕНТЫ И ПРИНАДЛЕЖНОСТИ 18 ПОВОРОТНЫЕ СТОЛЫ И АКСЕССУАРЫ 4 НАБОРЫ И ИНСТРУМЕНТЫ ДЛЯ РЕМОНТА РЕЗЬБЫ 5 ПРЕЦИЗИОННЫЕ ИЗМЕРИТЕЛЬНЫЕ ИНСТРУМЕНТЫ 11 РАБОЧИЕ ГОЛОВКИ И ПРИНАДЛЕЖНОСТИ 6 ФОРМОВКА И РЕЗКА МЕТАЛЛА 2 МАГНИТНЫЕ И ПЕРЕДВИЖНЫЕ ИНСТРУМЕНТЫ 2 ЧАСОВЫЕ ИНСТРУМЕНТЫ И ОБОРУДОВАНИЕ 6 ЮВЕЛИРНЫЕ ИНСТРУМЕНТЫ И ОБОРУДОВАНИЕ 10 СМАЗОЧНЫЕ ИНСТРУМЕНТЫ И ОБОРУДОВАНИЕ 5- Изготовлен из закаленной легированной стали.
- Инструмент, необходимый для тестирования токарных станков.
Сопутствующие товары
Испытательная оправка, стержень оправки, оправка, оправка, मेंड्रेल в Ганди Нагар, Ченнаи, Jasmine Enterprises
Испытательная оправка, стержень оправки, оправка, беседка, मेंड्रेल в Ганди Нагар, Ченнаи, Jasmine Enterprises | ID: 12602711812Описание продукта
Благодаря нашему богатому отраслевому опыту и знаниям, мы предлагаем нашим клиентам испытательные оправки.Тестовая оправка хорошо известна на национальных рынках благодаря своей гладкой поверхности и безупречному дизайну. Этот продукт производится квалифицированными профессионалами в соответствии с отраслевыми стандартами из проверенного качества сырья и передовых технологий.
Характеристики:
- Превосходный дизайн
- Высокий уровень производительности
- Высочайшее качество
Заинтересовались данным товаром? Получите последнюю цену у продавца
Связаться с продавцом
Изображение продукта
О компании
Год основания 2003
Юридический статус Фирмы Физическое лицо — Собственник
Характер бизнеса Производитель
Количество сотрудников До 10 человек
Годовой оборот Rs.50 лакх — 1 крор
Участник IndiaMART с августа 2010 г.
GST33AGGPR6038M1Z0
Код импорта и экспорта (IEC) 04040 *****
Будучи ориентированной на клиента организацией, мы производим, продаем и поставляем широкий ассортимент фрезерных станков , станков и . Широкий спектр предлагаемых нами станков включает вертикальный фрезерный станок и горизонтальный фрезерный станок .Эти машины широко используются в различных отраслях промышленности и признаны за их характеристики и плавные функциональные возможности. Мы также предлагаем держатели с ЧПУ , держатели для обрабатывающих инструментов, сменные сверла и держатели для корончатого сверления, сменные резцы, режущие инструменты и автомобильные развертки , которые изготавливаются с использованием сырья оптимального качества в соответствии с отраслевыми стандартами. Наша компания поддерживается командой высококвалифицированных и преданных своему делу профессионалов, которые помогают нам в удовлетворении конкретных требований клиента.С их помощью мы также предоставляем нашим клиентам услуги по тестированию согласно их требованию. Кроме того, наш отдел исследований и разработок позволяет нам наилучшим образом удовлетворять растущие требования клиентов.
Видео компании
Вернуться к началу 1 Есть потребность?
Получите лучшую цену
Есть потребность?
Получите лучшую цену
У вас недостаточно прав для чтения этого закона в настоящее время
У вас недостаточно прав для чтения этого закона в настоящее время Логотип Public.Resource.OrgЛоготип представляет собой черно-белую линию улыбающегося тюленя с усами. Вокруг печати находится красная круглая полоса с белым шрифтом, в верхней половине которого написано «Печать одобрения», а в нижней части — «Public.Resource.Org». На внешней стороне красной круглой марки находится круг. серебряная круглая полоса с зубчатыми краями, напоминающая печать из серебряной фольги.Public.Resource.Org
Хилдсбург, Калифорния, 95448
Соединенные Штаты Америки
Этот документ в настоящее время недоступен для вас!
Уважаемый гражданин:
В настоящее время вам временно отказано в доступе к этому документу.
Public Resource ведет судебный процесс за ваше право читать и говорить о законах. Для получения дополнительной информации см. Досье по рассматриваемому судебному делу:
Американское общество испытаний и материалов (ASTM), Национальная ассоциация противопожарной защиты (NFPA), и Американское общество инженеров по отоплению, холодильной технике и кондиционированию воздуха (ASHRAE) против Public.Resource.Org (общедоступный ресурс), DCD 1: 13-cv-01215, Объединенный окружной суд округа Колумбия [1]
Ваш доступ к этому документу, который является законом Соединенных Штатов Америки, был временно отключен, пока мы боремся за ваше право читать и говорить о законах, по которым мы решаем управлять собой как демократическим обществом.
Чтобы подать заявку на получение лицензии на ознакомление с этим законом, ознакомьтесь с Сводом федеральных нормативных актов или применимыми законами и постановлениями штата. на имя и адрес продавца. Для получения дополнительной информации о постановлении правительства и ваших правах как гражданина в соответствии с нормами закона , пожалуйста, прочтите мое свидетельство перед Конгрессом Соединенных Штатов. Вы можете найти более подробную информацию о нашей деятельности на общедоступном ресурсе. в нашем реестре деятельности за 2015 год. [2] [3]
Благодарим вас за интерес к чтению закона.Информированные граждане — это фундаментальное требование для работы нашей демократии. Благодарим вас за усилия и приносим извинения за возможные неудобства.
С уважением,
Карл Маламуд
Public.Resource.Org
7 ноября 2015 г.
Банкноты
[1] http://www.archive.org/download/gov.uscourts.dcd.161410/gov.uscourts.dcd.161410.docket.html
[2] https://public.resource.org/edicts/
[3] https://public.resource.org/pro.docket.2015.HTML
Алюминиевые испытательные оправки
Power Dart Blower Condux 08030003 Воздуходувка Condux Power Dart представляет собой пневматическую штанговую систему, особенно подходящую для протяженных воздуховодов. Трехмоторная система позволяет выбрать скорость, соответствующую вашим потребностям. Когда все три двигателя включены, он будет подавать до 300 кубических футов в минуту (8,5 м3 / мин)воздуха при макс. давление, легко продувая полилинию 1⁄2 дюйма (13 мм) или измерительную ленту
на расстояние более 2 000 футов (610 м) в кабелепроводе диаметром до 6 дюймов (152 мм).
Детали:
Комплект держателя для Power Dart Blower Condux 08030011
Требуется генератор мощностью 3000 Вт. Модель на 110 вольт включает адаптер с поворотной вилкой на 30 А.
Оправка для испытания древесины 2 «X 6», наружный диаметр 1,75 дюйма, проводимость 08020634 Condux 08020634 Оправки для испытания древесины 2 «X 6»
Протяните через канал, чтобы проверить целостность соединения и проверить, нет ли круглого канала. Деревянный корпус со стальным концом
колпачков и проушинами.
Технические характеристики:
- Размер воздуховода: 2 дюйма (51 мм)
- Длина корпуса: 6 дюймов (152 мм)
- Макс.D.: 1,75 дюйма (44 мм)
- Грузоподъемность: 2,2240 фунтов (9964 Н)
Condux 08020600 Держатель для испытания древесины
Протягивание через канал для проверки целостности соединения и испытания на выход из круглого канала 2240 фунтов. (9964 Н) грузоподъемность деревянный корпус со стальными торцевыми заглушками и проушинами.
Технические характеристики:
- Размер воздуховода: 102 мм (4 дюйма)
- Длина: 11 1/2 дюйма (292 мм)
- Максимальный наружный диаметр: 3.56 (90 мм)
Condux 08020622 Держатель для испытания древесины
Протягивание через канал для проверки целостности соединения и испытания на выход из круглого канала 2240 фунтов. (9964 Н) грузоподъемность деревянный корпус со стальными торцевыми заглушками и проушинами.
Технические характеристики:
- Размер воздуховода: 4 дюйма (102 мм)
- Длина: 12 дюймов (304 мм)
- Максимальный наружный диаметр: 3,75 дюйма (95 мм)
Condux 08020660 Держатель для испытания древесины
Протягивание через канал для проверки целостности соединения и испытания на выход из круглого канала 2240 фунтов. (9964 Н) грузоподъемность деревянный корпус со стальными торцевыми заглушками и проушинами.
Технические характеристики:
- Размер воздуховода: 102 мм (4 дюйма)
- Длина: 152 мм (6 дюймов)
- Максимальный наружный диаметр: 3,56 (90 мм)
Condux 08020630 Держатель для испытания древесины
Протягивание через канал для проверки целостности соединения и испытания на выход из круглого канала 2240 фунтов. (9964 Н) грузоподъемность деревянный корпус со стальными торцевыми заглушками и проушинами.
Технические характеристики:
- Размер воздуховода: 102 мм (4 дюйма)
- Длина: 152 мм (6 дюймов)
- Максимальный наружный диаметр: 3,75 (95 мм)
Condux 08020632 Оправки для испытания древесины 2 «X 12»
Протяните через канал, чтобы проверить целостность соединения и проверить, нет ли круглого канала. Деревянный корпус со стальным концом
колпачков и проушинами.
Технические характеристики:
- Размер воздуховода: 51 мм (2 дюйма)
- Длина корпуса: 12 дюймов (304 мм)
- Макс. : 1,75 дюйма (44 мм)
- Грузоподъемность: 2,2240 фунтов (9964 Н)
Раздвижные оправки для крепления зубчатых колес | Журнал Indian Machine Tools
Раздвижные оправки, удерживающие шестерни между центрами, используются в процессе изготовления зубчатых колес, чаще всего при контроле зубчатых колес, где высокая точность и диапазон расширения являются ключевыми преимуществами
— Тимоти Зеноски
В сфере производства зубчатых колес процесс окончательной проверки является последним этапом перед отправкой зубчатого колеса конечному пользователю.Чтобы получить надежные данные проверки, необходимо высокоточное устройство для удержания шестерни или шестерни. Для проверки зубьев шестерни шестерню обычно устанавливают между центрами на метрологической машине. Никакого крепления не требуется. Для проверки зубьев шестерен, особенно шестерен, используемых в автомобилях, обычно используется оправка. После того, как шестерня установлена на оправке, оправка устанавливается между центрами метрологического станка. .
На рынке имеется множество различных оправок, используемых для проверки зубьев шестерен.Самым основным из них является цельная центрирующая оправка, которая спроектирована и изготовлена с учетом диаметра отверстия, а точность ограничена допуском отверстия шестерни. .
Раздвижные контрольные оправки — наиболее распространенный и предпочтительный метод проверки зубьев шестерен. Раздвижная оправка может быть механической, в большинстве случаев использующей цангу, или гидравлической, использующей гидравлическую жидкость для расширения тонкостенной втулки. Раздвижная оправка цангового патрона может вмещать различные отверстия шестерни в пределах ограниченного диапазона размеров за счет смены цанги.Цанга обычно активируется (расширяется) путем затягивания гайки или болта. Диапазон расширения типичной цанги составляет от 0,381 мм (0,015 дюйма) до 0,508 мм (0,020 дюйма). Точность составляет 0,0050 миллиметра (0,0002 дюйма) TIR (общее показание индикатора). Контрольные оправки гидравлического типа обычно более точны, чем оправки для захвата с ПДП 0,0025 мм (0,0001 дюйма). Диапазон расширения составляет примерно половину от диапазона расширения оправки. .
Выбор правильного типа проверочной оправки зависит от проверяемой детали.Для производителей, которые производят множество шестерен с разным диаметром отверстия, обычно предпочтительнее расширяющаяся оправка. При замене цанги одну оправку можно использовать для ряда отверстий шестерен. Более простая цельная центрирующая оправка в большинстве случаев используется производителями зубчатых колес с ограниченными размерами отверстия зубчатой передачи, и часто эти оправки производятся производителем зубчатых колес. .
Одним из распространенных типов расширительных оправок для контроля зубчатых колес является оправка LeCount®, которая была запатентована в 1866 году Уильямом ЛеКаунтом.Помимо достижений в производственных технологиях, за его 150-летнюю историю в этот продукт было внесено несколько изменений, но он по-прежнему считается одной из лучших в отрасли оправок для проверки зубьев шестерен благодаря большому диапазону расширения в сочетании с исключительной точностью и повторяемость. .
По сравнению с оправками для цангового или гидравлического контроля, расширительные оправки LeCount имеют диапазон расширения от 3,175 мм (0,125 дюйма) до 25,4 мм (1000 дюймов) для стандартных размеров отверстий от 6.От 350 миллиметров (0,250 дюйма) до 177,800 миллиметров (7,000 дюймов).
И этот большой диапазон размеров отверстий шестерни достигается всего с помощью всего 12 оправок. Корпорация Gleason, которая приобрела LeCount в 2007 году, гарантирует концентричность на уровне 0,0025 миллиметра (0,0001 дюйма) TIR или лучше во всем диапазоне размеров.
Как это работает
В конструкции оправки LeCount используется принцип трех параллельных расширяющихся губок, которые равномерно скользят по наклонным или коническим путям.Это дает оправке значительный диапазон расширения. .
Там, где другие раздвижные оправки в промышленности требуют активации инструмента, обычно гаечного ключа или шестигранного ключа, оправки LeCount активируются легким касанием. Постукивание по задней бабке оправки освобождает губки. Инструменты не требуются. .
Другие типы оправок Lecount
Шлицевой оправка
Многие шестерни имеют шлицевые отверстия. Большинство стандартных разжимных оправок не могут контактировать и центрироваться ни по делительному, ни по большому диаметру шлицевого отверстия.Шлицевой оправка LeCount работает по тем же принципам, что и стандартные оправки, за исключением того, что делительный диаметр шестерни притачивается к контактным кромкам трех разжимных кулачков. Их также можно сделать так, чтобы они контактировали с большим диаметром шлицевого отверстия.
Шлифовальная оправка
За прошедшие годы Глисон обнаружил, что многие оправки, требующие ремонта, изношены или повреждены из-за того, что они использовались для удержания шестерен во время операции шлифования. По этой причине Глисон спроектировал и разработал оправку LeCount G (шлифовальная), которая более прочна и выдерживает силы, возникающие во время шлифования.Путем поворота оправки для активации, в отличие от метода активации, используемого на контрольных оправках, обеспечивается постоянная удерживающая сила.
Оправка G также герметизирована, чтобы стружка, стружка и другие загрязнения не попадали в оправку и не вызывали чрезмерного биения. Точность производственной оправки G составляет 0,005 мм (0,0002 дюйма) TIR.
Ремонт
Изношенные или поврежденные оправкиLeCount могут быть отремонтированы и сертифицированы Gleason как новые.Оправка проверяется на соосность, разбирается и очищается, а изношенные или поврежденные компоненты заменяются. Оправка собирается и снова проверяется. Например, у одного клиента были оправки, которые сгорели при пожаре в помещении для осмотра. Оправки были черными от копоти, но были разобраны и отремонтированы.
Основным преимуществом восстановления оправок является стоимость: стоимость восстановления оправки составляет примерно 50 процентов от стоимости новой оправки.
Для получения дополнительной информации перейдите в gleason.com.
— Автор, Тимоти Зеноски, проработал в Gleason Workholding Group 29 лет и занимал должности инженера-конструктора, технического менеджера и начальника производства
Тимоти Зеноски
работал в Gleason Workholding Group в течение 29 лет и занимал должности инженера-конструктора, технического менеджера и начальника производства. В качестве глобального директора по управлению продуктами для фиксации заготовок Зеноски отвечает за линейку продуктов для фиксации заготовок с глобальной точки зрения.Gleason производит опоры в Германии, Индии и Китае, а также в Рочестере, штат Нью-Йорк. Gleason LeCount является частью Gleason Workholding Group в Рочестере. Штат компании состоит из четырех человек, которые производят сборки и тестируют более 700 инспекционных оправок в год.
Дата | Код HS | Описание | Место назначения | Порт погрузки | Единица | Количество | Стоимость (INR) | за единицу (INR) ) | ||||||||||||||
---|---|---|---|---|---|---|---|---|---|---|---|---|---|---|---|---|---|---|---|---|---|---|
Ноя 17 2016 | 84669390 | ЗАПЧАСТИ ДЛЯ СТАНКА И ПРИНАДЛЕЖНОСТИ: -КОНЕЧНЫЕ И ПАРАЛЛЕЛЬНЫЕ ИСПЫТАТЕЛЬНЫЕ ШТАНГИ / МАНДРЕЛИ 2MT 202605 (СТАЛЬ) | Соединенное Королевство | Туглакабад | PCS | 900 15,6 Ноя 17 2016 | 84669390 | КОМПЛЕКТУЮЩИЕ ИНСТРУМЕНТЫ И ПРИНАДЛЕЖНОСТИ: -КОНЕЧНЫЕ И ПАРАЛЛЕЛЬНЫЕ ИСПЫТАТЕЛЬНЫЕ ШТАНГИ / МАНДРЕЛИ 4MT 202615 (СТАЛЬ) | Соединенное Королевство | Туглакабад | PCS | 19,180 | Октябрь 07 2016 | 84669310 | ТОКАРНЫЕ ДЕТАЛИ ИСПЫТАТЕЛЬНЫЙ МАНДРЕЛЬ — MT3 | Германия | Коимбаторе | NOS | 1 | 5,501 | 5,501 | |
Октябрь 07 2016 | 84669310 | ЗАПЧАСТИ ДЛЯ ИСПЫТАНИЯ ТОКАРНЫХ ЧАСТЕЙ (A2-5 / ME50) | Германия | Coimbatore | NOS | 1 | 8,069 | 8,069 | ||||||||||||||
Сен 17 2016 | 84661010 | ИСПЫТАНИЕ ДЕТАЛЕЙ ФРЕЗЕРНОГО СТАНКА С ЧПУ WTMM / 50-330 / BT50-SK50 | Германия | Banglore Air Cargo | NOS | 1 | 11,007 | 11,007 | ||||||||||||||
Авг 02 2016 | 84661010 | ИСПЫТАНИЕ ДЕТАЛЕЙ ФРЕЗЕРНОГО СТАНКА С ЧПУ WTMM / 40-330 / SK40 | Германия | Banglore Air Cargo | NOS | 2 | 16,749 | 8,375 | ||||||||||||||
Июл 22 2016 | 84661010 | ИСПЫТАНИЕ ДЕТАЛЕЙ ФРЕЗЕРНОГО СТАНКА ЧПУ WTMM / 40-346 / HSK-A63 5056275 | Южная Корея | Banglore Air Cargo | NOS | 1 | 19736 | 19736 | ||||||||||||||
19736 | ||||||||||||||||||||||
Может 20 2016 | 84661010 | ДЕРЖАТЕЛИ ИНСТРУМЕНТОВ VDI, 92PD-4040300 TEST MANDREL | Германия | Bangalore | NOS | 3 | 33,669 | 11,223 | ||||||||||||||
Мар 12 2016 | 84669390 | СТАНКОВЫЙ ИНСТРУМЕНТ ИСПЫТАТЕЛЬНЫЙ МАНДРЕЛЬ | Соединенное Королевство | Нхава-Шева Море | ШТ. | 30 | 40,170 | 1,339 | ||||||||||||||
Мар 12 2016 | 84669390 | СТАНКОВЫЙ ИНСТРУМЕНТ ИСПЫТАТЕЛЬНЫЙ МАНДРЕЛЬ | Соединенное Королевство | Нхава-Шева Море | ШТ. | 30 | 38,162 | 1,272 | ||||||||||||||
Янв 29 2016 | 84661010 | ДЕРЖАТЕЛИ ДЛЯ ИНСТРУМЕНТОВ VDI, PD-5040300 ИСПЫТАТЕЛЬНЫЙ МАНДРЕЛЬ (МЫ ПРЕДНАЗНАЧЕНЫ ЗАЯВИТЬ НАГРАДЫ ПРИ ЭКСПОРТЕ ИЗ ИНДИИ (MEIS) | Германия | Banglore Air Cargo | 900 | Декабрь 16 2015 | 84661010 | TEST MANDREL WTMM / 40-330 / SK40 (5056226) | Германия | Banglore Air Cargo | NOS | 1 | 8,019 | 8,019 | ||||||||
Октябрь 23 2015 | 84669390 | СТАНКА ДЛЯ ИСПЫТАНИЯ СТАНКОВ (TEST MANDREL) | Норвегия | Нхава Шева Море | PCS | 5 | 7,360 | 1,472 | ||||||||||||||
Октябрь 23 2015 | 84669390 | СТАНКА ИСПЫТАНИЯ СТАНКОВ (ИСПЫТАТЕЛЬНЫЙ МАНДРЕЛЬ) | Норвегия | Нхава Шева Море | PCS | 5 | 9,684 | 1,937 | ||||||||||||||
Авг 24 2015 | 84661010 | ДЕРЖАТЕЛИ ИНСТРУМЕНТОВ Идентификационный знак-Y-30 ИСПЫТАТЕЛЬНЫЙ МАНДРЕЛЬ (ВЫСТАВОЧНЫЕ ТОВАРЫ) | Италия | Нхава Шева Море | НОМЕР | 1 | 138 | 138 | ||||||||||||||
Авг 10 2015 | 84661010 | ИСПЫТАНИЕ ДЕТАЛЕЙ ФРЕЗЕРНОГО СТАНКА С ЧПУ WTMM / 40-330 / SK40 5056226 | Германия | Banglore Air Cargo | NOS | 1 | 7,904 | 7,904 | ||||||||||||||
Июл 22 2015 | 84669390 | СТАНКОВЫЕ ИНСТРУМЕНТЫ TEST MANDREL MT-5 | Соединенное Королевство | Нхава Шева Море | PCS | 5 | 12,600 | 2,520 | ||||||||||||||
Может 11 2015 | 84669390 | TEST MANDREL | Соединенное Королевство | Нхава-Шевское море | PCS | 10 | 14,747 | 1,475 | ||||||||||||||
Апр 30 2015 | 84669310 | МАШИНА ДЛЯ ИСПЫТАНИЯ ТОКАРНЫХ ДЕТАЛЕЙ DMH SPECIAL A5SHORT TAPER, МЫ ПРЕДНАЗНАЧЕНЫ ЗАЯВИТЬ НАГРАДЫ ПОД MEIS, P. Leave a Reply
|