Контрольные образцы по ГОСТ 18442-80
Контрольные образцы для капиллярной дефектоскопии предназначены для определения качества дефектоскопических материалов и технологии капиллярного контроля. Образцы по КД имеют искусственную, одиночную, тупиковую трещину с шириной раскрытия в соответствии с заданным классом чувствительности. Образцы по КД соответствуют требованиям ГОСТ 18442-80 и унифицированной методики РБ-090-14 (взамен ПНАЭГ-7-018-89).
Технические характеристики образцов: размер – 100х30х3 мм; материал – сталь 40Х13. Примерный ресурс использования образцов при использовании люминесцентных материалов – 100 раз, при использовании цветных материалов — 50 раз. После отработки ресурса по капиллярной дефектоскопии, образец можно использовать для магнитопорошкового контроля в соответствии с уровнем чувствительности, установленным при аттестации данного образца.
Класс чувствительности | ||
Длина трещины | Ширина раскрытия | |
I | не менее 3 | менее 1 |
II | не менее 3 | От 1 до 10 |
III | не менее 3 | От 10 до 100 |
IV | не менее 3 | От 100 до 500 |
Контрольный образец по КД должен храниться в сухом месте с влажностью воздуха не более 80% и температурой 20±10°С.
После проведения контроля, образец необходимо очистить одним из следующих способов:
- На контролируемую поверхность образца нанести слой проявителя, затем просушить на воздухе и выдержать не менее 30 минут после высыхания;
- Опустить в растворитель (ацетон, бензин, спирт) с выдержкой не менее 5-6 часов;
- Погрузить в растворитель (ацетон, бензин, спирт) с использованием ультразвуковой ванны, с выдержкой не менее 60 мин.
После очистки образец для капиллярной дефектоскопии необходимо прогреть в сушильном шкафу при температуре 100-120° с выдержкой 15-30 минут. Во избежание затирания проявителя в дефект, не попускается протирка контрольного образца влажной салфеткой. Каждый образец снабжен паспортом и сертификатом о калибровке содержащие фотографию трещины, ее параметры, режимы контроля и инструкцию по эксплуатации. Срок действия сертификата о калибровке – 1год с момента выдачи. Методика поверки (калибровки) содержится в рекомендациях Р 08-02-2000. Контрольный образец по КД входит в состав набора для капиллярной дефектоскопии и в перечень обязательного оборудования для аттестации лаборатории НК по капиллярному методу.
Контрольные образцы для капиллярной дефектоскопии и другие приборы неразрушающего контроля можно купить с доставкой до двери или до терминалов транспортной компании в следующих городах: Москва, Санкт-Петербург, Екатеринбург, Саратов. Амурск, Ангарск, Архангельск, Астрахань, Барнаул, Белгород, Бийск, Брянск, Воронеж, Великий Новгород, Владивосток, Владикавказ, Владимир, Волгоград, Волгодонск, Вологда, Иваново, Ижевск, Йошкар-Ола, Казань, Калининград, Калуга, Кемерово, Киров, Кострома, Краснодар, Красноярск, Курск, Липецк, Магадан, Магнитогорск, Мурманск, Муром, Набережные Челны, Нальчик, Новокузнецк, Нарьян-Мар, Новороссийск, Новосибирск, Нефтекамск, Нефтеюганск, Новочеркасск, Нижнекамск, Норильск, Нижний Новгород, Обнинск, Омск, Орёл, Оренбург, Оха, Пенза, Пермь, Петрозаводск, Петропавловск-Камчатский, Псков, Ржев, Ростов, Рязань, Самара, Саранск, Смоленск, Сочи, Сыктывкар, Таганрог, Тамбов, Тверь, Тобольск, Тольятти, Томск, Тула, Тюмень, Ульяновск, Уфа, Ханты-Мансийск, Чебоксары, Челябинск, Череповец, Элиста, Ярославль и другие города.
Контрольный образец для капиллярной дефектоскопии
Контрольный образец изготовлен в виде пластины 100 × 30 × 4 мм из стали 40Х13. В нем предусмотрена искусственная одиночная тупиковая трещина с шириной раскрытия в рамках заданного класса чувствительности. В комплект к каждому образцу прилагается паспорт с фотоснимком трещины, где отмечены режимы контроля, имеется метрологическое свидетельство с указанием параметров трещины, а также инструкция по очистке образца. Лучше всего использовать в процессе контроля комплект из 3-х образцов — контрольный, рабочий, экспертный.
Контрольный образец соответствует требованиям ГОСТ 18.442-80 и унифицированной методике ПНАЭ Г-7-018-89.
Технические характеристики образцов: размер – 100х30х3 мм; материал – сталь 40Х13. Примерный ресурс использования образцов при использовании люминесцентных материалов – 100 раз, при использовании цветных материалов – 50 раз. После отработки ресурса по капиллярной дефектоскопии, образец можно использовать для магнитопорошкового контроля в соответствии с уровнем чувствительности, установленным при аттестации данного образца.
Класс чувствительности | Размеры трещины, мкм | |
Длина трещины | Ширина раскрытия | |
I | не менее 3 | менее 1 |
II | не менее 3 | От 1 до 10 |
III | не менее 3 | От 10 до 100 |
IV | не менее 3 | От 100 до 500 |
Контрольный образец по КД должен храниться в сухом месте с влажностью воздуха не более 80% и температурой 20±10°С. В помещении не должно быть паров агрессивных веществ, вызывающих коррозию металлических поверхностей.
После проведения контроля, образец необходимо очистить одним из следующих способов:
- На контролируемую поверхность образца нанести слой проявителя, затем просушить на воздухе и выдержать не менее 30минут после высыхания;
- Опустить в растворитель (ацетон, бензин, спирт) с выдержкой не менее 5-6 часов;
- Погрузить в растворитель (ацетон, бензин, спирт) с использованием ультразвуковой ванны, с выдержкой не менее 60 мин.
После очистки образец для капиллярной дефектоскопии необходимо прогреть в сушильном шкафу при температуре 100-120° с выдержкой 15-30 минут. Во избежание затирания проявителя в дефект, не допускается протирка контрольного образца влажной салфеткой. Каждый образец снабжен паспортом и сертификатом о калибровке, содержащие фотографию трещины, ее параметры, режимы контроля и инструкцию по эксплуатации. Срок действия сертификата о калибровке – 1 год с момента выдачи. Методика поверки (калибровки) содержится в рекомендациях Р 08-02-2000. Контрольный образец по КД входит в состав набора для капиллярной дефектоскопии и в перечень обязательного оборудования для аттестации лаборатории НК по капиллярному методу.
Контрольный образец для капиллярного контроля
Контрольный образец для капиллярного контроля 1, 2, 3 или 4 класса чувствительности для определения качества дефектоскопических материалов и технологии капиллярного контроля по соответствующему классу чувствительности.
Контрольный образец для капиллярного контроля соответствует требованиям ГОСТ 18442-80 и унифицированной методики ПНАЭГ-7-018-89.
Контрольный образец для капиллярного контроля изготовлен из стали 40Х13 и имеет искусственную, одиночную, тупиковую трещину с шириной раскрытия в соответствии с заданным классом чувствительности.
Класс чувствительности | Размеры трещины, мкм | |
Длина трещины | Ширина раскрытия | |
I | не менее 3 | менее 1 |
II | не менее 3 | От 1 до 10 |
III | не менее 3 | От 10 до 100 |
IV | не менее 3 |
От 100 до 500 |
Контрольный образец по КД должен храниться в сухом месте с влажностью воздуха не более 80% и температурой 20±10°С. В помещении не должно быть паров агрессивных веществ, вызывающих коррозию металлических поверхностей.
После проведения контроля, образец необходимо очистить одним из следующих способов:
- На контролируемую поверхность образца нанести слой проявителя, затем просушить на воздухе и выдержать не менее 30минут после высыхания;
- Опустить в растворитель (ацетон, бензин, спирт) с выдержкой не менее 5-6 часов;
- Погрузить в растворитель (ацетон, бензин, спирт) с использованием ультразвуковой ванны, с выдержкой не менее 60 мин.
После очистки образец для капиллярной дефектоскопии необходимо прогреть в сушильном шкафу при температуре 100-120° с выдержкой 15-30 минут. Во избежание затирания проявителя в дефект, не допускается протирка контрольного образца влажной салфеткой. Каждый образец снабжен паспортом и сертификатом о калибровке содержащие фотографию трещины, ее параметры, режимы контроля и инструкцию по эксплуатации.
Гарантийный срок эксплуатации –
Образец для капиллярной дефектоскопии поставляется в комплекте с метрологической аттестацией.
Контрольные образцы для капиллярной дефектоскопии — ndv-xr.by
Контрольные образцы для капиллярной дефектоскопии — это небольшие, но очень важные аксессуары. Они незаменимы для проведения неразрушающей диагностики пенетрантивными веществами. С их помощью определяют чувствительность того или иного препарата, тем самым выявляя наиболее подходящий для соответствующей ситуации.
Контрольные образцы для капиллярной дефектоскопии: основные особенности
Стандартные образцы применяют для проверки флуоресцентных и просто красящих препаратов. Обычно для этих целей используются различные элементы. Каждый образец — это небольшая стальная пластина с покрытием или без него. На ней специально расположена трещина, которую и должен выявить пенентрант. Условно все аксессуары делятся на 4 большие группы в соответствии с классом чувствительности:
- Первый класс.
Имеют дефект самого маленького размера. Длина трещины обычно не менее 3 мкм, ширина ее раскрытия — не более 1 мкм.
- Второй класс. Оснащен дефектом длиной от 3 мкм и шириной в 1–10 мкм.
- Третий класс. Существенно отличается от первых двух. Длина трещины все также более 3 мкм, степень же раскрытия достигает 10–100 мкм.
- Четвертый класс. Самый низкий. Имеет дефект шириной в 100–500 мкм.
Вне зависимости от степени чувствительности используемого образца, алгоритм применения для каждого из них абсолютно идентичен. Процесс проверки состоит из нескольких этапов:
- Очистка специализированным составом или классическим растворителем.
- Просушивание при помощи сушильного оборудования на протяжение не менее 15–30 минут.
- Нанесение пенетранта и классический капиллярный контроль.
При использовании образцов крайне важно следовать рекомендациям, указанным в прилагающемся к аксессуару паспорте. Пренебрегая ими можно испортить принадлежность, что в дальнейшем исказит результаты проверок.
Если вы занимаетесь капиллярным контролем и планируете приобрести образцы, специализированные препараты или оборудование, то обязательно изучите каталог ООО «НДВ-Комплект». В нем мы собрали лучшую продукцию от известных производителей. Предлагаем своим клиентам доступные цены и удобную доставку товаров по всей Беларуси. Оформить заказ можно по телефону.
Стандартный образец для капиллярного контроля по цене всего 3300 грн
Описание
Назначение
Стандартный образец для капиллярного контроля предназначен для определения качества дефектоскопических материалов и технологии капиллярного контроля.
Соответствие стандартам
Образец соответствует требованиям ГОСТ 18442-80 и унифицированной методики РБ-090-14 (взамен ПНАЭГ-7-018-89).
На образце для капиллярного контроля находится искусственная, тупиковая трещина с шириной раскрытия с заданным классом чувствительности (см. таблицу).
Класс чувствительности | Размеры трещины, мкм | |
Длина трещины | Ширина раскрытия | |
I | не менее 3 | менее 1 |
II | не менее 3 | от 1 до 10 |
III | не менее 3 | от 10 до 100 |
IV | не менее 3 | от 100 до 500 |
Значения освещенности для выявления протяженных индикаторных следов дефектов типа трещин в зависимости от класса чувствительности приведены в таблице
Класс чувствительности |
Условия визуального выявления протяженных индикаторных следов дефектов (соотношение ширины следа и ширины раскрытия дефекта 10:1) |
|||||
Ультрафиолетовая облученность при использовании люминесцентных методов (Л, ЛЦ, ФЛ, ФЛЦ) | Освещенность, лк, при использовании цветных и яркостных методов (Ц, Я, ФЦ) для ламп | |||||
люминесцентных | накаливания | |||||
отн.![]() |
мкВт/см2 | комбинированная | общая | комбинированная | общая | |
I | 300-100 | 3000-1000 | 2500* | 750 | 2000* | 500 |
II | ||||||
III | 150±50 | 1500±500 | 2000 | 500 | 1500 | 400 |
IV | 75±25 | 750±250 | 750 | 300 | 500 | 200 |
* При цветном методе с диффузионным проявлением допускается принимать значения соответственно 4000 и 3000 лк.
Технические характеристики
Технические характеристики образца
Размер образца, мм | 105х30 |
Толщина образца, мм | 4,5 |
Материал | 40Х13 |
Шероховатость контролируемой поверхности Rа, не более, мкм |
1,25 |
Эталон контрольный образец для ЦД в наличии
Контрольный образец для цветной дефектоскопии
Модель: Эталон контрольный для ЦД
Страна происхождения: Россия
Статус: официальный дистрибьютор
Эталон контрольный образец для ЦД предназначен для цветной дефектоскопии. Контрольный образец используется в работе для проверки и определения качества дефектоскопических материалов, а так же образец применяется в технологии капиллярного контроля по соответствующему классу чувствительности. Эталон контрольный образец для цветной дефектоскопии выпускаются для контроля трех классов чувствительности. Образцы для цветной дефектоскопии изготовлены из стали, имеют тупиковую трещину с шириной раскрытия в соответствии с чувствительностью класса. Эталон контрольный образец для ЦД (для цветной дефектоскопии)
Эталон для ЦД предназначен для определения качества дефектоскопических материалов и технологии капиллярного контроля по соответствующему классу чувствительности. Контрольные образцы соответствуют требованиям РД-13-06-2006. Эталоны контрольные образцы для ЦД выпускаются для трех классов чувствительности (I ,II ,III). Контрольные образцы ЦД изготовлены из стали 15Х25Т, имеют искусственную одиночную тупиковую трещину с шириной раскрытия в соответствии с классом чувствительности. Ресурс использования образца для ЦД при применении в капиллярной дефектоскопии: — для люминесцентного набора – 100 раз — для цветного набора — 50 раз. Контрольный образец ЦД должен храниться в сухом месте с относительной влажностью не более 80% и температурой воздуха 20±10°С. В помещениях для хранения не должно быть паров агрессивных веществ, вызывающих коррозию металлических поверхностей.
Комплектация стандартного образца для цветной дефектоскопии (ЦД): контрольный образец, свидетельство о метрологической аттестации с характеристиками трех параметров дефекта, дефектограммой и сроком очередной поверки.
Контрольные образцы для капиллярной дефектоскопии — «Реахим-Фото СПб»
Описание
Предназначены для определения качества дефектоскопических материалов и технологии капиллярного контроля по соответствующему классу чувствительности. Контрольные образцы соответствуют требованиям ГОСТ 18.442-80 и методики ПНАЭГ-7-018-89.
Выпускаются для трех классов чувствительности (I ,II ,III).Контрольные образцы имеют искусственную одиночную тупиковую трещину с шириной раскрытия в соответствии с классом чувствительности.
Технические характеристики:
Класс чувствительности Длина трещины, мм Ширина раскрытия, мм
I не менее 3 менее 0,001
II не менее 3 0,001-0,01
III не менее 3 0,01
1. Назначение
Стандартный образец изготовлен из стали марки 40Х ГОСТ 5632-72 , имеет одиночный дефект в виде трещины и предназначен для оценки чувствительности дефектоскопических материалов, используемых для капиллярных методов неразрушающего контроля по ГОСТ 18442-80.
2. Описание и технические характеристики
- Материал образца – сталь 40Х по ГОСТ 5632-72 ;
- Размеры образца – 300 мм. – 1,0 мм. х 38 мм. – 0,34 мм. х 4,1 мм. – 0,12 мм.
- Шероховатость контролируемой поверхности R a > 2,5 мкм.
- Глубина трещины адекватна толщине азотированного слоя (100-200 мкм.)
- Геометрические параметры микротрещины представлены в таблице 1
Таблица 1
НОМЕР ОБРАЗЦА |
Кол-во трещин |
Размер микротрещин |
Примечание |
|
---|---|---|---|---|
Ширина раскрытия, мкм |
Длина, |
|||
46-2 |
1 |
2,0 |
38 |
II класс |
Контрольный образец должен храниться в сухом месте с относительной влажностью не более 80% и температурой воздуха 20±10°С. В помещениях для хранения не должно быть паров агрессивных веществ, вызывающих коррозию металлических поверхностей
Ресурс использования образца при применении:
- цветного набора для капиллярной дефектоскопии – 80 циклов;
- люминисцентного набора – 40 циклов.
Контроль проводился набором дефектоскопических материалов в составе — DP-51, D-100 , DR-60.
В случае не подтверждения качества образца при очередной аттестации, образец допускается использовать в магнитопорошковой дефектоскопии с дополнениями в паспорте о переходе на уровень чувствительности А, режим намагничивания – продольный.
3. Комплект поставки
В комплект поставки входит один образец для КД, паспорт, упаковка.
Penetrant Testing — обзор
Новые физические эффекты в гидродинамике пенетрантных испытаний
При пенетрантных испытаниях размерный эффект пенетрантной вязкости проявляется как на стадии заполнения микродефектов, так и в значительно большей степени при абсорбции пенетранта слой мелкодисперсного проявителя на стадии разработки. Физический смысл предложенной интерпретации эффекта размерной вязкости заключается в следующем. Эффект обнаружен в полярных жидкостях, молекулы которых не только сдвигающие, но и моментные напряжения действуют между компонентами такой микрополярной жидкости.В результате жидкие ассоциаты не только совершают поступательное движение, но и имеют собственные угловые скорости. Таким образом, энергия, затрачиваемая на абсорбцию жидкости на определенную глубину, расходуется на преодоление как сдвиговых, так и моментных напряжений между ассоциатами, т.е. при заданном перепаде давления расход жидкости уменьшается, а эффективная вязкость возрастает. В частности, было получено выражение для расчета смещения пенетрантного мениска в тупиковом цилиндрическом капилляре длиной l o и радиусом R от устья на глубину [1, 2] °:
(1 ) t = 6μHℓ02ψH6 cos θ [ν22− (1 − ψ) (ν + ψℓnψ − νψ)] x x (k∼H) 2 (k∼H) 2 + 3δ¯ [2− (k∼H) cth (k ∼H / 2)],
, где ψ = pk / (pk − pa); pk = 26 cos θ / H — капиллярное давление, μ H — табулированная сдвиговая вязкость пенетранта при заданной температуре; σ — коэффициент поверхностного натяжения; θ — угол смачивания; v = 1/10; Па — атмосферное давление; k∼ и δ¯ — параметры микроструктуры пенетранта.
Впервые разработан и использован метод определения микроструктурных параметров пенетрантов k∼ и δ¯. Полученные значения k∼ и δ¯ для некоторых пенетрантов, широко используемых в испытаниях пенетрантов, впервые были использованы для описания размерного эффекта проникающей вязкости в капиллярных дефектах различной геометрии и в пористых материалах [3].
Предлагаемая модель развития дефекта [4] основана на трех уравнениях, описывающих поглощение пенетранта, содержащегося в дефекте, пористым слоем сорбционного проявителя.Это уравнение Навье-Стокса для потока жидкости на фронте пропитки в слое проявителя и соотношение баланса массы жидкости, которое замыкает уравнения. Из-за нехватки места мы не будем приводить здесь вывод уравнений кинетики развития дефекта, который был описан в [4, 5], а только перечислим основные характеристики процесса, важные для качества и чувствительности теста. . Это проникающая вязкость μ и поверхностное натяжение σ, толщина h, пористость ρ, проницаемость и эффективный радиус R e слоя проявителя, остаточное заполнение полости дефекта пенетрантом перед нанесением проявителя на исследуемую поверхность n.
Последнее количество особенно важно для чувствительности теста. Поэтому полное двухстороннее заполнение тупиковых конических капилляров жидкими пенетрантами, сопровождающееся значительным (на 2 или 3 порядка) увеличением скорости растворения газа, запертого в капилляре, в жидкости, представляет особый интерес для теории. и практика пенетрантного тестирования [6]. Установлено, что некоторые жидкости (вода, ацетон, этиловый и бутиловый спирты и др.) Заполняют конические капилляры длиной 1 o ≲ 2 · 10 −3 м и радиусом R o ∼ 20 мкм, а не только от устья, но также и от тупика капилляра, где образуется и поднимается еще один столб жидкости.
Обе столбы жидкости движутся в капилляре навстречу друг другу и в момент слияния (полного заполнения капилляра) их объемы становятся сравнимыми по порядку величины. Некоторые специальные эксперименты показали, что эффект можно объяснить переконденсацией жидкости в канале из-за наличия двух менисков разной кривизны.
Проведенные эксперименты по определению влияния полного двухстороннего заполнения капилляров жидкостью на пенетрантное тестирование позволили выработать практические рекомендации по повышению чувствительности теста.Например, у сорбционных порошковых проявителей эффект снижает порог чувствительности теста. Между тем, замена суспензии порошкового проявителя с правильно подобранными физико-химическими свойствами существенно увеличивает чувствительность теста. Выбор осуществляется с помощью соотношений, лежащих в основе другого эффекта, который мы наблюдали в капилляре, когда две разные жидкости соприкасаются. Исследования кинетики миграции жидкостей после их соприкосновения в капилляре выявили особый тип взаимодействия, заключающийся в извлечении одной жидкости из капилляра другой [7].Мы предложили физическую модель процесса, основанную на предположении, что одна жидкость течет относительно другой по стенке капилляра в виде тонкой пленки. Термодинамический анализ [8] показал, что такой процесс действительно возможен, если свойства жидкости L 1 , контактирующей в капилляре с жидкостью L 2 , удовлетворяют соотношению
(2) δL1 cos θ1≥δL2cos θ2,
, где δL1,2 и θ 1,2 — поверхностное натяжение и угол смачивания капиллярного материала жидкостями L 1 и L 2 . Эксперименты показали, что соотношение (2) выполнялось для всех жидкостей, для которых наблюдался эффект экстракции, а именно для воды, ацетона, этилового и бутилового спиртов, реальных индикаторов и других жидкостей, используемых при пенетрантных испытаниях.
Эффект негистерезисный. Когда (2) не выполняется, жидкость L 1 блокируется в капилляре жидкостью L 2 , контактирующей с первым.
Исследования капилляров как модельных дефектов подтверждены реальными промышленными пенетрантными испытаниями.В [9] мы показали, в частности, что жидкая фаза проявителя оказывает существенное влияние на обнаружение дефектов и очень важна для процесса тестирования.
Принимая во внимание эффект извлечения одной жидкости из капилляра другой, можно выбрать лучшие составы наборов для пенетрантного тестирования и повысить надежность теста. Этот критерий мы использовали при разработке метода испытания пористых материалов.
Соотношение (2) должно соблюдаться при составлении новых наборов для отбора жидкостей, последовательно взаимодействующих друг с другом в процессе пенетрантного тестирования (шайба, индикатор, очиститель, жидкий носитель проявителя) и для замены новых материалов, более эффективных и экологически чистых, в используемые комплекты.
Инспекция пенетранта — обзор
Другие методы обнаружения трещин
Широко используются несколько других методов обнаружения трещин, включая магнитопорошковый контроль, дефектоскопию красителя и ультразвук. Для магнитопорошкового контроля и дефектоскопии красителей используются многие химические препараты. К ним относятся растворители, красители и «проявители». Многие из них удобно упакованы в аэрозоли. Другие состоят из ванн, в которые погружаются проверяемые детали.
Растворители, как правило, обладают обезжиривающим действием и поэтому вредны для кожи. Они могут вызвать дерматит в долгосрочной перспективе, если не свести к минимуму контакт с кожей. Как правило, они относительно летучие, выделяют пары, которые можно вдохнуть. Воздействие на здоровье зависит от воздействия и относительной токсичности растворителя. Они могут включать раздражение глаз и легких, головную боль, тошноту, головокружение и дурноту. Бессознательное состояние или даже смерть могут возникнуть в результате воздействия паров растворителей в больших количествах.
Когда-то предпочтительным вариантом были хлорированные растворители, поскольку они, как правило, негорючие. Стратегия заключалась в использовании растворителя с наименьшей токсичностью. Однако из-за опасений по поводу атмосферы многие обычные хлорированные растворители в настоящее время больше не используются. Это заставило работодателей выбирать альтернативы, некоторые из которых более токсичны, а некоторые легко воспламеняются. Таким образом, перед использованием растворителя следует изучить паспорт безопасности (MSDS) производителя, чтобы получить представление обо всех его свойствах, чтобы можно было принять меры для его правильного хранения и предотвращения воздействия паров и любых опасностей возгорания, которые могут возникают.Растворители всегда следует использовать в хорошо вентилируемых помещениях, чтобы избежать образования высоких концентраций паров.
Многие аэрозоли раньше содержали пропелленты на основе хлорированных углеводородов или хлорированных фторуглеродов (CFC), но теперь они не используются. В настоящее время используемые пропелленты включают некоторые легковоспламеняющиеся вещества, такие как бутан. Следует внимательно прочитать паспорт безопасности материала. Некоторые хлорированные растворители все еще используются. Они имеют тенденцию разлагаться в дуге с образованием чрезвычайно токсичных продуктов, таких как фосген и хлористый водород.Поэтому очень важно следить за тем, чтобы пары растворителя не попадали в места, где выполняется сварка.
Объемные запасы растворителей или аэрозолей следует хранить отдельно от рабочего помещения в контейнерах, соответствующих их свойствам, например: легковоспламеняющиеся вещества и препараты следует хранить в металлических шкафах с четкой маркировкой, указывающей на характер содержимого. В рабочем помещении следует держать только количество, необходимое для немедленной работы.
Если используются ванны для парового обезжиривания, они должны содержаться в хорошем рабочем состоянии — конструкция должна содержать пар, чтобы сотрудники не подвергались воздействию.
Следует по возможности избегать протирания предметов тканями, пропитанными растворителем, так как выброшенные салфетки могут представлять опасность пожара, и такая практика имеет тенденцию приводить к сильному воздействию на кожу и дыхательную систему.
Везде, где есть вероятность попадания капель жидкости в глаза, следует надевать средства защиты глаз. Персонал не должен есть или курить в местах, где есть растворители. Их следует тщательно мыть после работы, а также перед едой или курением.
История ИП
Капиллярное действие:
Сила, являющаяся результатом адгезии, когезии и поверхностного натяжения жидкостей, находящихся в контакте с твердыми телами, как в капиллярной трубке.
Флуоресценция:
Свойство вещества, такого как флюорит, излучать свет при воздействии на него лучистой энергии, такой как ультрафиолетовые лучи или рентгеновские лучи.
Черный свет:
Ультрафиолетовое или инфракрасное излучение, используемое для флуоресцентных эффектов, фотографии и т. Д. В темноте.
Ультрафиолетовый свет:
Свет, лежащий сразу за фиолетовым концом видимого спектра и имеющий длину волны короче, чем приблизительно 4000 ангстрем.
Введение и история
Пенетрантный контроль
Пенетрантный контроль — это метод, который используется для выявления дефектов поверхности путем вытекания цветного или флуоресцентного красителя из дефекта. Метод основан на способности жидкости втягиваться в «чистую» поверхность, разрушая дефект капиллярным действием. После периода времени, называемого «выдержкой», избыток пенетранта с поверхности удаляется и наносится проявитель. Это действует как промокашка.Он извлекает пенетрант из дефекта, чтобы выявить его наличие. Цветные (контрастные) пенетранты требуют хорошего белого света, тогда как флуоресцентные пенетранты необходимо использовать в затемненных условиях с ультрафиолетовым «черным светом».
Самый ранний метод проверки поверхности включал натирание технического углерода на глазурованную керамику, в результате чего технический углерод оседал в поверхностных трещинах, делая их видимыми. Позже в железнодорожных мастерских стало практикой проверять детали из железа и стали методом «масло-путассы».В этом методе тяжелая нефть, обычно доступная в железнодорожных мастерских, разбавлялась керосином в больших резервуарах, так что части локомотива, такие как колеса, могли быть погружены в воду. После удаления и тщательной очистки поверхность была покрыта тонкой суспензией мела в спирте, так что после испарения спирта образовался белый поверхностный слой. Затем объект подвергался вибрации, ударяя молотком, в результате чего остаточное масло в любых трещинах поверхности просачивалось наружу и окрашивало белое покрытие. Этот метод использовался со второй половины 19 века примерно до 1940 года, когда был введен метод магнитных частиц, который оказался более чувствительным для ферромагнитного железа и стали.
Другой (хотя и связанный) метод был введен в 1940-х годах. Исследуемая поверхность была покрыта лаком, и после высыхания образец приводился в колебание с помощью удара молотка. Вибрация вызывает растрескивание хрупкого слоя лака, как правило, вокруг поверхностных дефектов. Хрупкий лак (покрытие напряжений) используется в первую очередь для демонстрации распределения напряжений в детали, а не для поиска дефектов.
Многие из этих ранних разработок были выполнены Magnaflux в Чикаго, штат Иллинойс, США, в сотрудничестве с Switzer Bros., Кливленд, Огайо, США. Magnaflux разработала более эффективные проникающие масла, содержащие хорошо видимые (обычно красные) красители, для улучшения способности обнаружения дефектов. Этот метод, известный как метод пенетранта красителя с видимым или цветным контрастом, до сих пор довольно широко используется. В 1942 году Magnaflux представила систему проникающего контроля Zyglo, в которой флуоресцентные красители добавлялись в жидкий пенетрант. Эти красители затем будут флуоресцировать при воздействии ультрафиолетового света (иногда называемого «черным светом»), делая признаки трещин и других поверхностных дефектов более заметными для инспекторов.
Обзор общих методов неразрушающего контроля
Неразрушающий контроль является одной из функций контроля качества и дополняет другие, давно применяемые методы.
По определению, неразрушающий контроль — это проверка материалов на наличие поверхностных или внутренних дефектов или металлургического состояния без какого-либо нарушения целостности материала или его пригодности для эксплуатации.
Метод может применяться на основе выборки для индивидуального исследования или может использоваться для 100-процентной проверки материала в системе контроля качества производства.
Наиболее распространены пять методов неразрушающего контроля, каждый из которых имеет свои преимущества и недостатки, которые позволят определить, подходит ли он для вашего конкретного применения. Это следующие методы:
- Радиография
- Обнаружение трещин с помощью магнитных частиц
- Испытание на проникновение красителя
- Ультразвуковое обнаружение дефектов
- Вихретоковые и электромагнитные испытания
Радиография
Основы. Радиографический контроль позволяет обнаружить внутренние дефекты в черных и цветных металлах.Рентгеновские лучи, генерируемые электрически, и гамма-лучи, испускаемые радиоактивными изотопами, проникают через излучение, которое поглощается материалом, через который они проходят. Чем больше толщина материала, тем больше поглощение лучей. Эти лучи помогают сформировать скрытое изображение, которое можно проявить и зафиксировать аналогично обычной фотопленке.
Инструменты. Необходимы различные рентгенографические и фотографические аксессуары, включая радиомониторы, пленочные маркеры, индикаторы качества изображения и оборудование для темной комнаты.Также требуются рентгенографическая пленка и химикаты для обработки.
Преимущества. При рентгенографическом исследовании информация представлена наглядно. Предоставляется постоянная запись, которую можно просматривать в любое время и в месте, удаленном от теста. Этот тип тестирования полезен для тонких срезов и подходит для любого материала. Чувствительность заявлена на каждой пленке.
Недостатки. Радиография не подходит для некоторых типов тестовых ситуаций. Например, радиография не подходит для поверхностных дефектов и для автоматизации, если система не включает рентгеноскопию с усилителем изображения или другими электронными средствами.Рентгенография обычно не справляется с толстыми срезами, а само обследование может представлять опасность для здоровья. Необходимо оборудование для обработки и просмотра пленки, а также состав для экспонирования. При использовании этого метода луч должен быть точно направлен на двумерные дефекты. Также рентгенографический контроль не показывает глубину дефекта под поверхностью.
Контроль магнитных частиц
Основы. Магнитопорошковый контроль может обнаруживать поверхностные и приповерхностные неоднородности в магнитных материалах, в основном в ферритной стали и чугуне.Принцип заключается в создании магнитного потока в исследуемом изделии, при этом силовые линии проходят вдоль поверхности под прямым углом к предполагаемому дефекту. Когда силовые линии приближаются к неоднородности, они уйдут в воздух в устье трещины. Край трещины становится магнитно-привлекательными полюсами, северным и южным. Они обладают способностью притягивать мелкодисперсные частицы магнитного материала, например, железные начинки. Обычно эти частицы представляют собой оксид железа размером от 20 до 30 микрон.Они подвешены в жидкости, которая обеспечивает им подвижность на поверхности образца для испытаний, способствуя их перемещению к краям трещины. Однако в некоторых случаях они могут применяться в форме сухого порошка.
Инструменты. В основном, оборудование для обнаружения магнитных трещин бывает двух видов. Во-первых, для испытательных образцов, которые являются частью большой конструкции, или, например, для труб и тяжелых отливок, которые нельзя легко перемещать, оборудование принимает форму просто блока питания для генерации сильного тока.Для заводских приложений на небольших, более управляемых испытательных образцах, стендовое оборудование — с блоком питания, индикаторной системой чернил, рециркулирующей жидкость, и средствами для захвата заготовки и подачи тока или потока магнитного потока в методичном контролируемом манера — вообще предпочтительнее.
Преимущества. Магнитопорошковый контроль обычно прост в эксплуатации и применении. Это количественное тестирование, которое можно автоматизировать, помимо просмотра. Однако современные разработки в области автоматического распознавания дефектов можно использовать в деталях с простой геометрией, таких как заготовки и стержни.В этом случае специальная камера фиксирует изображение индикации дефекта и обрабатывает его для дальнейшего отображения и действий.
Недостатки. Этот тип неразрушающего контроля ограничен ферромагнитными материалами, а также поверхностными или приповерхностными дефектами. Магнитопорошковый контроль небезопасен; отсутствие индикации может означать, что дефектов нет или процесс не был выполнен должным образом.
Тестирование проникновения красителя
Основы. Испытание на проникновение красителя часто используется для обнаружения поверхностных дефектов в неферромагнитных материалах. Проверяемую деталь необходимо очистить химическим способом, обычно паровой фазой, чтобы удалить все следы посторонних материалов, жира, грязи и других загрязнений с поверхности, как правило, но также и изнутри трещин. Затем наносится пенетрант, который представляет собой тонкое жидкое масло, обычно окрашенное в ярко-красный или ультрафиолетовый флуоресцентный цвет, и оставляется в контакте с поверхностью в течение примерно 15 минут. Капиллярное действие втягивает пенетрант в трещину в этот период. Затем излишки пенетранта с поверхности полностью удаляются и наносится тонкий слой порошкового мела.По прошествии соответствующего времени проявки мел вытягивает краситель из трещины, образуя визуальное указание, увеличенное по ширине, в отличие от фона.
Инструменты. Можно использовать различные вещества, и их можно наносить разными способами, от простого нанесения с помощью аэрозольных баллончиков до более сложных средств, таких как автоматическое погружение в большие резервуары. Для более сложных методов требуются резервуары, оборудование для распыления и сушки.
Преимущества. Количественный анализ и определение проникающей способности красителя просты в выполнении и являются хорошим способом обнаружения трещин, разрушающих поверхность, в цветных металлах.Он подходит для автоматического тестирования, но с теми же ограничениями, что и при автоматическом распознавании дефектов при магнитопорошковом контроле.
Недостатки. Испытания на проникновение красителя ограничиваются только дефектами, разрушающими поверхность. Он менее чувствителен, чем некоторые другие методы, и требует значительного количества расходных материалов.
Ультразвуковая дефектоскопия
Основы. Этот метод обнаруживает внутренние и поверхностные (особенно удаленные поверхности) дефекты в звукопроводящих материалах.Короткий импульс ультразвука генерируется с помощью электрического заряда, приложенного к пьезоэлектрическому кристаллу, который колеблется в течение очень короткого периода с частотой, зависящей от толщины кристалла. Этому импульсу требуется конечное время, чтобы пройти через материал к границе раздела и отразиться обратно в зонд. Зондирование всех граней образца позволяет выявить трехмерный дефект, измерить его глубину и определить размер.
Инструменты. Современные ультразвуковые дефектоскопы являются полностью твердотельными, могут работать от батарей и, как правило, рассчитаны на работу в условиях рабочей площадки.Процесс можно автоматизировать, и сейчас он используется на многих литейных предприятиях.
Преимущества. Ультразвуковая дефектоскопия может использоваться для проверки толщины и длины до 30 футов. Этот тип тестирования может определить положение, размер и тип дефекта. Это портативный тип тестирования, который при необходимости обеспечивает исключительную чувствительность и может быть полностью автоматизирован. Для тестирования необходим доступ только к одной стороне, а расходные материалы не используются.
Недостатки. Постоянная запись недоступна, если не используются более сложные результаты испытаний и системы сбора данных.Оператор может решить, является ли образец дефектным, в то время как испытание выполняется. Показания испытаний требуют интерпретации, за исключением цифровых измерителей толщины стенок. Чтобы получить максимальную информацию из теста, необходимы значительные навыки. Наконец, очень тонкие срезы может быть трудно протестировать этим методом.
Вихретоковый контроль
Основы. Метод вихревых токов позволяет обнаруживать поверхностные или подповерхностные дефекты и измерять проводимость и толщину покрытия.Это испытание чувствительно к проводимости, проницаемости и размерам материала образца. Для проверки поверхности на наличие трещин в деталях одиночной или сложной формы обычно используются катушки с одной обмоткой с ферритовым сердечником. Зонд помещается на компонент и «уравновешивается» с помощью органов управления электронного блока. Когда зонд сканирует поверхность детали, обнаруживаются трещины.
Инструменты. Большинство вихретоковой электроники имеют фазовый индикатор, который позволяет оператору определять неисправные состояния.Некоторые подразделения могут проверять продукт одновременно на двух или более разных тестовых частотах. Эти устройства позволяют электронным способом нейтрализовать определенные нежелательные эффекты, чтобы улучшить обнаружение дефектов. Большинство автоматизированных систем предназначены для компонентов с простой геометрией.
Преимущества. Подходящий для автоматизации, вихретоковый контроль может определять ряд состояний проводящего материала, таких как дефекты, состав, твердость, проводимость и проницаемость. Информация может быть предоставлена в простых терминах, часто — с ходу или без ответа.Для получения более подробной информации о продукте можно использовать электронные блоки фазового дисплея. Доступны компактные портативные испытательные установки, и этот тип испытания не требует расходных материалов, за исключением датчиков, которые иногда можно отремонтировать. Этот метод является гибким благодаря множеству пробников и тестовых частот, которые можно использовать для различных приложений.
Недостатки. Многие параметры могут влиять на реакцию вихретокового сигнала. Это означает, что сигнал от желаемой характеристики материала (например, трещины) может быть замаскирован нежелательным параметром, таким как изменение твердости.В некоторых случаях требуется тщательный выбор датчика и электроники. Кроме того, испытания обычно ограничиваются условиями разрушения поверхности и небольшими подземными дефектами.
С Марком Уиллкоксом, управляющим директором, и Джорджем Даунсом можно связаться в Insight NDT Equipment Ltd., Kings Thorn, Herefordshire HRZ 8AW, England, 44-0-1981-541122, факс 44-0-1981-541133, www. insightndt.com.
Неразрушающий контроль — Проверка проницаемости красителя
Что такое проверка на проникновение красителя?
Dye Penetrant Inspection (DPI), также называемый Liquid Penetrant Inspection (LPI) или Penetrant Testing (PT), является одним из старейших и упрощенных методов неразрушающего контроля, самые ранние версии которого (с использованием смеси керосина и масла) относятся к 19 веку.
Жидкостный проникающий контроль используется для обнаружения любых связанных с поверхностью неоднородностей, таких как трещины от усталости, закалки и шлифования, а также трещины, пористость, неполное сплавление и дефекты в соединениях.
Принципы
DPI основан на капиллярном действии, при котором жидкость с низким поверхностным натяжением проникает в чистые и сухие неоднородности, разрушающие поверхность. Пенетрант может быть нанесен на тестовый компонент окунанием, распылением или кистью. По истечении достаточного времени проникновения избыток пенетранта удаляется и наносится проявитель.Разработчик помогает извлечь пенетрант из дефекта, где невидимая индикация становится видимой инспектору. Проверка проводится в ультрафиолетовом или белом свете, в зависимости от типа используемого красителя — флуоресцентный или нефлуоресцентный (видимый).
Материалы
Пенетранты классифицируются по уровням чувствительности. Видимые пенетранты обычно красного цвета и представляют самую низкую чувствительность. Флуоресцентные пенетранты содержат два или более красителя, которые флуоресцируют при возбуждении ультрафиолетовым (УФ-А) излучением (также известным как черный свет).Поскольку флуоресцентный проникающий контроль выполняется в затемненной среде, а возбужденные красители излучают яркий желто-зеленый свет, который сильно контрастирует с темным фоном, этот материал более чувствителен к дефектам.
При выборе уровня чувствительности необходимо учитывать множество факторов, в том числе среду, в которой будет проводиться испытание, качество поверхности образца и размер искомых дефектов. Также необходимо убедиться, что исследуемые химические вещества совместимы с образцом, чтобы исследование не вызвало стойкого окрашивания или разрушения.Этот метод может быть довольно портативным, потому что в его простейшей форме для проверки требуется всего 3 баллончика с аэрозолем, несколько безворсовых салфеток и достаточный видимый свет. Стационарные системы со специальными станциями нанесения, промывки и проявки более дороги и сложны, но приводят к большей чувствительности и увеличению пропускной способности образцов.
Этапы проверки
- Предварительная очистка:
Испытуемая поверхность очищается для удаления любой грязи, краски, масла, жира или любых отслаивающихся отложений, которые могут удерживать пенетрант от дефекта или вызывать несоответствующие или ложные показания.Методы очистки могут включать растворители, этапы щелочной очистки, парообразование или струйную очистку. Конечная цель этого шага — получить чистую поверхность, на которой любые дефекты будут открытыми, сухими и свободными от загрязнений. Обратите внимание, что если используется струйная очистка, она может «проработать» небольшие неоднородности детали, и ванна для травления рекомендуется в качестве обработки после струйной очистки. - Нанесение пенетранта:
Затем пенетрант наносится на поверхность испытуемого объекта.Пенетранту дают «время выдержки», чтобы проникнуть в любые дефекты (обычно от 5 до 30 минут). Время выдержки в основном зависит от используемого пенетранта, испытываемого материала и размера искомых дефектов.Как и ожидалось, меньшие дефекты требуют большего времени проникновения. Из-за их несовместимости необходимо соблюдать осторожность, чтобы не наносить пенетрант на основе растворителя на поверхность, которая должна быть проверена с помощью водосмываемого пенетранта.
- Удаление излишков пенетранта:
Затем излишки пенетранта удаляются с поверхности.Метод удаления зависит от типа используемого пенетранта. Обычно выбираются смываемые водой, удаляемые растворителем, липофильные постэмульгируемые или гидрофильные постэмульгируемые. Эмульгаторы представляют собой наивысший уровень чувствительности и химически взаимодействуют с маслянистым пенетрантом, что позволяет удалить его с помощью водяного спрея. При использовании средства для удаления растворителя и безворсовой ткани важно не распылять растворитель непосредственно на тестовую поверхность, поскольку это может удалить пенетрант с дефектов. Если избыток пенетранта не удалить должным образом, после нанесения проявителя он может оставить фон в проявленной области, который может скрыть признаки или дефекты.Кроме того, это также может привести к ложным показаниям, что серьезно затруднит вашу способность провести надлежащий осмотр.
- Применение проявителя:
После удаления избытка пенетранта на образец наносится белый проявитель. Доступны несколько типов проявителя, в том числе: неводный влажный проявитель, сухой порошок, водорастворимый и водорастворимый. Выбор проявителя определяется совместимостью пенетранта (нельзя использовать водорастворимый или суспендируемый проявитель с водосмываемым пенетрантом) и условиями проверки.При использовании неводного влажного проявителя (NAWD) или сухого порошка образец необходимо высушить перед нанесением, в то время как растворимые и суспендируемые проявители наносятся на часть, еще влажную после предыдущего шага. NAWD коммерчески доступен в аэрозольных баллончиках и может использовать ацетон, изопропиловый спирт или пропеллент, который является их комбинацией. Проявитель должен образовывать полупрозрачное ровное покрытие на поверхности.
Проявитель вытягивает пенетрант из дефектов на поверхность, чтобы сформировать видимую индикацию, широко известную как просачивание.Любые выходящие за пределы области участки могут указывать на расположение, ориентацию и возможные типы дефектов на поверхности. Для интерпретации результатов и определения дефектов по обнаруженным показаниям может потребоваться определенная подготовка и / или опыт. - Инспекция:
Инспектор будет использовать видимый свет достаточной интенсивности (обычно 100 фут-свечей или 1100 люкс) для видимого пенетранта красителя. Ультрафиолетовое (УФ-А) излучение адекватной интенсивности (обычно 1000 микроватт на квадратный сантиметр) наряду с низким уровнем окружающего освещения (менее 2 фут-кандел) для флуоресцентных проникающих исследований.Осмотр тестовой поверхности следует проводить через 10-30 минут, в зависимости от типа продукта. Эта временная задержка позволяет осуществить промокание. Инспектор может наблюдать образец для формирования индикации при использовании видимого красителя.Также хорошей практикой является наблюдение за показаниями по мере их формирования, потому что характеристики истечения являются важной частью интерпретации характеристик дефектов.
- Последующая очистка:
Испытательную поверхность часто очищают после проверки и регистрации дефектов, особенно если запланированы процессы нанесения покрытия после проверки.
Преимущества и недостатки
Основные преимущества и недостатки по сравнению с другими методами неразрушающего контроля:
Преимущества
- Высокая чувствительность (можно обнаружить небольшие разрывы).
- Некоторые ограничения по материалам (металлические и неметаллические, магнитные и немагнитные, а также проводящие и непроводящие материалы могут проверяться).
- Оперативное обследование больших площадей и объемов.
- Подходит для деталей сложной формы.
- Обозначения наносятся непосредственно на поверхность детали и представляют собой визуальное представление дефекта.
- Портативный (материалы доступны в аэрозольных баллончиках)
- Низкая стоимость (материалы и сопутствующее оборудование относительно недорого)
Недостатки
- Обнаруживаются только дефекты поверхностного разрушения.
- Проверять можно только материалы с относительно непористой поверхностью.
- Предварительная очистка имеет решающее значение, поскольку загрязнения могут маскировать дефекты.
- Металлические пятна от механической обработки, шлифования, дробеструйной или пароструйной обработки должны быть удалены.
- Инспектор должен иметь прямой доступ к проверяемой поверхности.
- Шероховатость и шероховатость поверхности могут повлиять на чувствительность контроля.
- Должно выполняться и контролироваться несколько технологических операций.
- Требуется дополнительная очистка допустимых деталей или материалов.
- Требуется обращение с химическими веществами и надлежащая утилизация.
Стандарты
Международная организация по стандартизации (ISO)
- ISO 3452-1, Неразрушающий контроль. Пенетрантный контроль. Часть 1.Общие принципы
- ISO 3452-2, Неразрушающий контроль. Пенетрантные испытания. Часть 2. Испытания проникающих материалов.
- ISO 3452-3, Неразрушающий контроль. Пенетрантное испытание. Часть 3. Стандартные образцы для испытаний. .
- ISO 3452-4, Неразрушающий контроль. Пенетрантный контроль. Часть 4: Оборудование .
- ISO 3452-5, Неразрушающие испытания. Испытания на проницаемость. Часть 5: Испытания на проницаемость при температурах выше 50 ° C.
- ISO 3452-6, Неразрушающий контроль. Испытание на проницаемость. Часть 6. Испытание на проницаемость при температурах ниже 10 ° C.
- ISO 3059, Неразрушающий контроль. Пенетрантный контроль и испытание магнитными частицами. Условия просмотра.
- ISO 12706, Неразрушающий контроль. Пенетрантное тестирование.
Словарь
. - ISO 23277, Неразрушающий контроль сварных швов. Проникающий контроль сварных швов. Уровни приемки .
Европейский комитет по стандартизации (CEN)
- EN 1371-1, Литье — Жидкостный проникающий контроль — Часть 1: Песок, литье под давлением и под низким давлением
- EN 1371-2, Литье — Жидкостный контроль — Часть 2: Отливки по выплавляемым моделям
- EN 10228-2, Неразрушающий контроль стальных поковок — Часть 2: Испытание на проницаемость
- EN 10246-11, Неразрушающий контроль стальных труб — Часть 11: Испытание на проницаемость бесшовных и сварных стальных труб для обнаружения поверхностных дефектов
Американское общество испытаний материалов (ASTM)
- ASTM E 165, Стандартная практика проверки проницаемости жидкостей для общей промышленности
- ASTM E 1417, Стандартная практика испытаний на проникновение жидкости
Американское общество инженеров-механиков (ASME)
- Нормы ASME по котлам и сосудам под давлением, раздел V, ст.
6, Исследование проникновения жидкости
- Нормы ASME по котлам и сосудам под давлением, раздел V, ст. 24 Стандартный метод испытаний на проникновение жидкости SE-165 (идентичный ASTM E-165)
Испытание на проникновение жидкости — Nortech Advanced NDT Ltd.
Проверка на проникновение жидкости (LPI), также известная как проверка на проникновение красителя (DP), является как распространенным, так и недорогим методом неразрушающего контроля, который можно использовать для идентификации поверхности. устранение дефектов во всех непористых материалах (металлы, пластмассы или керамика).Пенетрант может применяться ко всем материалам из цветных металлов, но для проверки компонентов из черных металлов предпочтительнее магнитопорошковое исследование из-за его способности обнаружения под поверхностью. LPI используется для обнаружения дефектов литья и поковки, трещин и утечек в новых продуктах, а также усталостных трещин на компонентах, находящихся в эксплуатации.
Пенетрантный контроль красителя включает капиллярность или капиллярное притяжение, когда жидкость имеет способность течь в тесные или узкие пространства без посторонней помощи — и даже в противовес таким естественным силам, как сила тяжести. Материалы, используемые при дефектоскопии красителя, позволяют видеть результаты капиллярного притяжения, собирать их в качестве данных и интерпретировать. В конечном счете, испытание на проникающую жидкость — очень эффективный метод определения степени неровностей поверхности многих материалов, в том числе тех, которые не видны сразу.
Преимущества (LPI):
Эффективен для большинства материалов, включая металлические, неметаллические, проводящие, непроводящие, магнитные и немагнитные,
Совместимость со сложными геометрическими формами
Используемые материалы очень портативны и доступны по цене
Визуальные, легко видимые результаты
Могут обнаруживать нарушения непрерывности в процессе эксплуатации, включая усталостные трещины, HIC, SCC и SOHIC
Процесс проверки жидким пенетрантом:
Предварительная очистка
Поверхность исследуемого материала должным образом очищена от любых загрязнений, которые могут помешать процедуре или привести к получению ложных или нерелевантных данных.
Нанесение пенетранта на деталь в вентилируемой испытательной зоне
На поверхность испытуемого объекта наносится жидкий пенетрант. Проникающий материал обычно представляет собой ярко окрашенную жидкость, обладающую очень низким поверхностным натяжением и капиллярным действием. Затем пенетранту позволяют «впитаться» в любые дефекты.
Удаление излишка пенетранта
Удаление излишка пенетранта с поверхности.
Нанесение белого проявителя
Проявитель извлечет пенетрант непосредственно из любых дефектов.Он будет формироваться на поверхности, образуя видимый признак, обычно называемый «просачиванием».
Инспекция
Для видимого пенетранта красителя инспекторы будут использовать свет соответствующей интенсивности. Ультрафиолетовое (УФ-А) излучение наряду с низким уровнем внешней освещенности используется для флуоресцентных проникающих исследований.
Очистка
После осмотра и сбора данных участок очищается.
Тест на проницаемость жидкости | United Gamma NDT and Engineering Co., ООО
Материалы для испытаний на проницаемость
Пенетрантные материалы, используемые сегодня, намного сложнее, чем керосин и путассу, впервые примененные железнодорожными инспекторами на рубеже 20-го века. Сегодняшние пенетранты тщательно разработаны, чтобы обеспечить желаемый инспектором уровень чувствительности. Для хорошей работы пенетрант должен обладать рядом важных характеристик. Пенетрант должен:
- легко распределяется по поверхности проверяемого материала, обеспечивая полное и равномерное покрытие.
- может быть вовлечен в поверхностные дефекты капиллярным действием.
- остаются в дефекте, но легко удаляются с поверхности детали.
- остаются текучими, поэтому их можно вернуть на поверхность детали через этапы сушки и проявки.
- должен быть хорошо виден или ярко флуоресцировать, чтобы легко видеть показания.
- не причинит вреда исследуемому материалу или инспектору.
Что такое пенетрант?
Это жидкость.Он обладает способностью проникать или проникать в мелкие отверстия, такие как трещины. С точки зрения метода проникающего контроля проникающий агент — это жидкость, которая имеет способность проникать в каждое доступное ему отверстие. Однако для целей осмотра требуется гораздо больше, чем способность распространяться и проникать через поверхность.
МЕХАНИЗМ ПРОБИВАНИЯ
Для хорошего пенетранта только поверхностное натяжение, смачивающая способность и вязкость имеют прямое влияние на проницаемость (способность проникать).
Проницаемость — это свойства пенетранта, которые заставляют его проникать в очень мелкие отверстия, такие как трещины.
Физические свойства проникающих материалов
- Вязкость
- Поверхностное натяжение
- Смачивающая способность
- Удельный вес
- Волатильность
- Температура воспламенения
- Растворимость
- Способность распространяться или ползать
- Допуск к загрязнениям
- Токсичность
- Запах / Отсутствие склонности к раздражению кожи
- Инертность или некоррозионность
- Мытье
Теоретически хороший пенетрант должен иметь:
- Хорошая смачивающая способность
- очень маленький угол контакта
- Высокое поверхностное натяжение
- Но этого трудно достичь — i.
е. иметь одновременно высокие значения cos θ (малые θ) и τ
- Поверхностное натяжение в жидкости является примером силы сцепления, когда молекулы притягиваются примерно к
молекулам. Сила сцепления стремится связать их вместе. - Смачивающее действие в жидкости является примером силы адгезии, когда молекулы притягиваются
инородным телом, а сила адгезии имеет тенденцию растекать жидкость
Жидкостный проникающий контроль (LPI) — один из наиболее широко используемых методов неразрушающего контроля (NDE).Его популярность можно объяснить двумя основными факторами: относительной простотой использования и гибкостью. LPI можно использовать для проверки практически любого материала, при условии, что его поверхность не слишком шероховатая или пористая. Материалы, которые обычно проверяются с помощью LPI, включают следующее:
- Металлы (алюминий, медь, сталь, титан и др.)
- Стекло
- Многие керамические материалы
- Резина
- Пластмассы
Не все пенетрантные материалы работают одинаково и не предназначены для одинаковых характеристик. Производители пенетрантов разработали различные составы для решения различных задач контроля. Некоторые приложения требуют обнаружения мельчайших возможных дефектов и имеют гладкие поверхности, с которых легко удалить пенетрант. В других приложениях размер отклоняемого дефекта может быть больше, и можно использовать пенетрант, составленный для обнаружения более крупных дефектов. Пенетранты, которые используются для обнаружения мельчайшего дефекта, также дают наибольшее количество не относящихся к делу признаков.
Тип пенетранта
Пенетрантные материалы бывают двух основных типов.Эти типы перечислены ниже:
- Тип 1 — флуоресцентные пенетранты
- Тип 2 — Видимые пенетранты
ПРОНИКНАЯ СИСТЕМА
Пенетрантные системы обычно идентифицируются по методу пенетрантного удаления
- Моющийся водой
- Постэмульгирование
- Удаляемый растворителем
Три системы являются общими для флуоресцентных и видимых
Подготовка поверхности
Одним из наиболее ответственных этапов дефектоскопии является подготовка поверхности. На поверхности не должно быть масла, жира, воды или других загрязнений, которые могут препятствовать проникновению пенетранта в дефекты. Образец также может потребовать травления, если были выполнены механические операции, такие как механическая обработка, шлифование или дробеструйная очистка. Эти и другие механические операции могут размазать металл по отверстию дефекта и предотвратить попадание пенетранта.
Пенетрантное приложение
После того, как поверхность была тщательно очищена и высушена, пенетрантный материал наносится распылением, кистью или погружением детали в ванну для пенетранта.
Проникающее жилище
Пенетрант остается на поверхности на время, достаточное для того, чтобы позволить как можно большему количеству пенетранта вытекать из дефекта или просочиться в него. Время пребывания пенетранта — это общее время, в течение которого пенетрант находится в контакте с поверхностью детали. Время выдержки обычно рекомендуется производителями пенетранта или требуется спецификацией. Время варьируется в зависимости от области применения, используемых проникающих материалов, материала, формы проверяемого материала и типа проверяемого дефекта.Минимальное время ожидания обычно составляет от пяти до 60 минут. Как правило, нет никакого вреда в использовании более длительного времени выдержки пенетранта до тех пор, пока пенетранту не дают высохнуть. Идеальное время выдержки часто определяется экспериментально и может быть очень специфичным для конкретного применения.
Материал | Форма | Тип несплошности | Время проникновения мин * |
---|---|---|---|
Латунь и бронза | отливки | пористость | 10 |
холодное закрытие | 10 | ||
штамповки и поковки | кругов | 10 | |
сварных швов | отсутствие плавления | 10 | |
трещины | 10 | ||
все формы | трещины | 10 | |
Магний | отливки | пористость | 10 |
холодные шлюшки | 10 | ||
штампованные и поковки | кругов | 10 | |
сварных швов | отсутствие плавления | 10 | |
пористость | 10 | ||
все формы | трещины | 10 | |
сталь | отливки | пористость | 10 |
холодные шлюшки | 10 | ||
штамповки и поковки | кругов | 10 | |
сварных швов | отсутствие плавления | 20 | |
пористость | 20 | ||
все формы | трещины | 20 |
Материал | Форма | Тип несплошности | Время проникновения мин * |
---|---|---|---|
Алюминий | отливки | пористость | 10 |
холодные шлюшки | 10 | ||
штамповки и поковки | кругов | 10 | |
сварных швов | отсутствие плавления | 10 | |
пористость | 10 | ||
все формы | трещины | 10 | |
Пластмассы | все формы | трещины | 10 |
Стекло | все формы | трещины | 10 |
Инструмент с твердосплавными напайками Инструменты | отсутствие плавления | 10 | |
пористость | 10 | ||
трещины | 20 | ||
Титан и инструменты для высоких температур | все | 20 или 30 | |
керамика | все формы | трещины | 10 |
пористость |
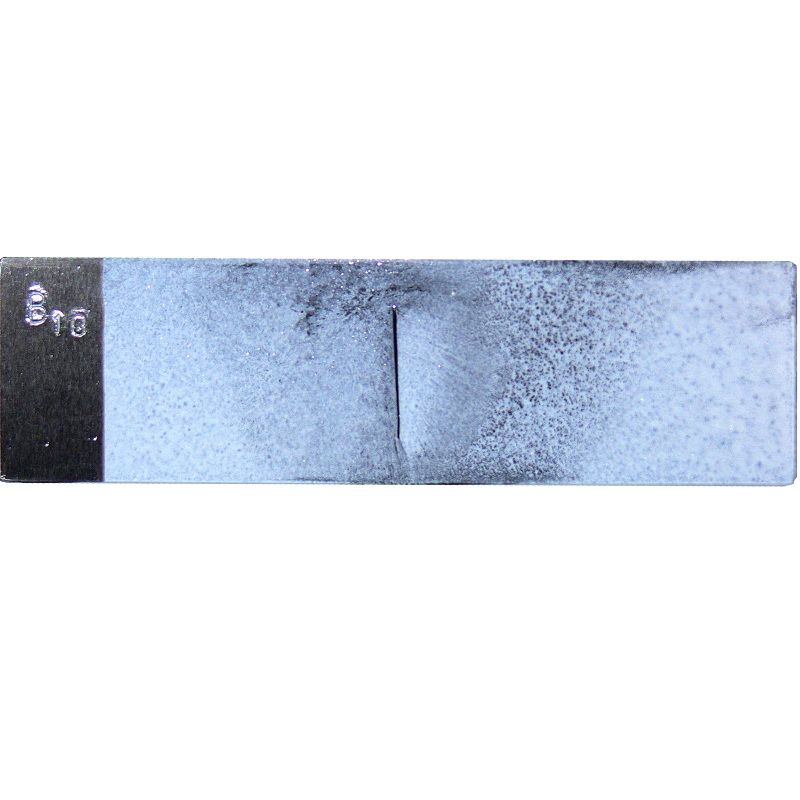